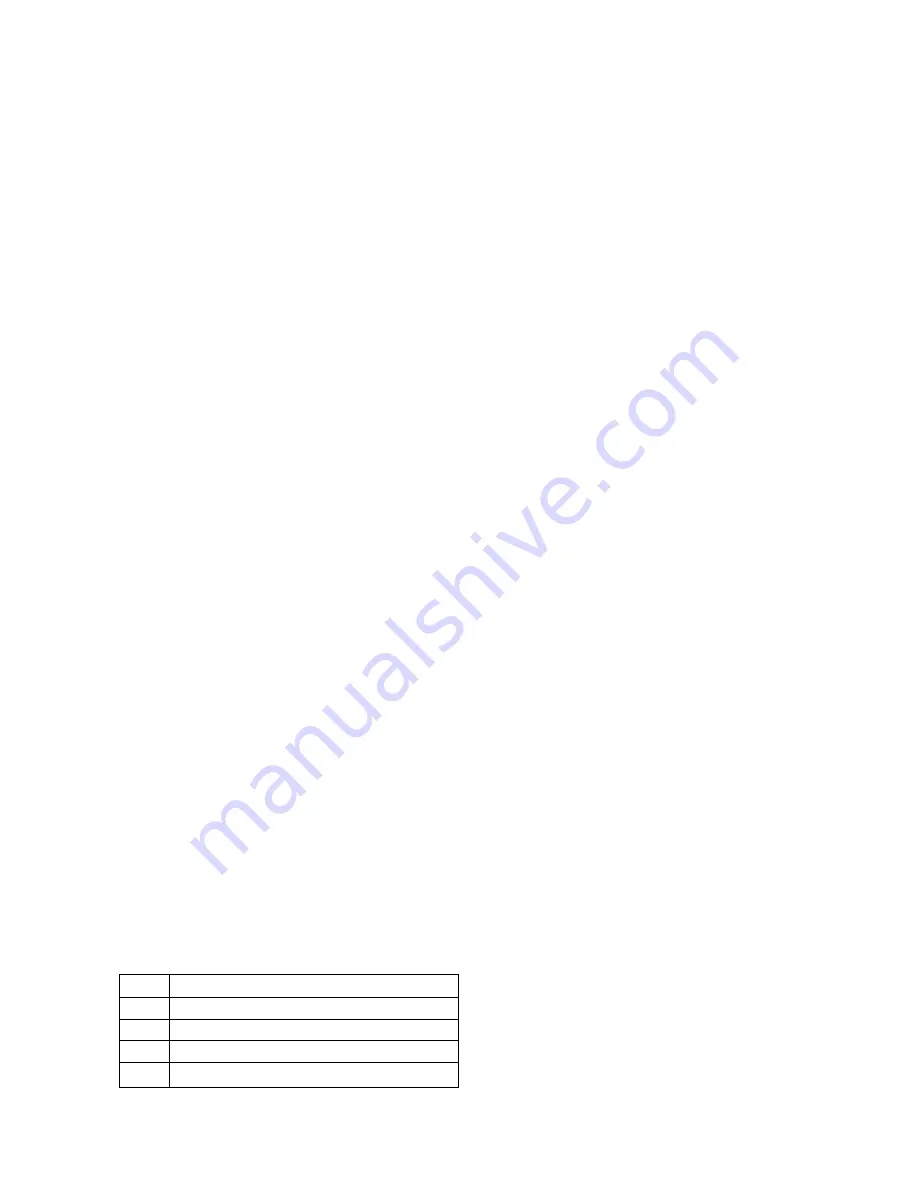
11
Caution!
The transmitter CPT 1Az must not be connected without checking the supply voltage. The transmitter outlet
conductors must neither be connected to the electric actuator frame nor to the earth, not even accidentally.
Before the supply voltage is checked, it is first necessary to disconnect the transmitter from the supply mains.
Measure the voltage on terminals of the electric actuator to which the transmitter is connected – this can best be done
using a digital voltmeter of input resistance at least 1 M
Ω
. This voltage should fall within the range of 18 – 25 V DC; in no
case may it exceed 30 V
(otherwise the transmitter can be damaged).
Then, connect the transmitter so that the positive
pole of the power source is connected to the positive pole of the transmitter, i.e. to the pin with red insulator
(r)
+
(nearer
to the transmitter centre).
The terminal with white coating
(wired to the terminal 52)
is connected to the negative pole
of the transmitter
(white insulator).
In the latest design variants the red conductor is plus and the black one is minus.
A milli-ammeter, preferentially a digital one with accuracy at least 0.5 %, is temporarily connected in series with the transmitter.
The output shaft is moved to the position CLOSE. The signal value should decrease. If this is not the case, the output shaft should
be rotated in the CLOSE direction until the signal starts decreasing and the output shaft reaches the CLOSE position.
Then, loosen the screws of the transmitter shim plates so that the whole transmitter can be turned to set the current
to 4 mA, and retighten the screws of the shim plates. Thereafter, move the output shaft of the electric actuator to
the position OPEN. Using the resistance trimmer on the transmitter face
(nearer to the edge)
set the current to 20 mA.
The trimmer has 12 turn and no stops. Hence, it cannot be damaged.
In case the correction of the current 20 mA was considerable repeat adjustment for 4 mA and 20 mA once again.
Disconnect the milli-ammeter. The screw secured by a drop of varnish situated nearer to the centre must not be turned.
Retighten the countershafts fixing the transmitter shim plates and secure with a drop of varnish against loosening.
After completing the adjusting procedure, check voltage on the transmitter terminals using a voltmeter. The voltage
should fall within the range of 9 – 16 V with current 20 mA.
Note:
The transmitter characteristics has two branches: the descending one and the ascending one with respect to
the CLOSE position. The characteristics is selected by turning the transmitter body.
Current position transmitter DCPT – setting
1. Set of end-limit positions
Before starting the setting, verification must be carried out that the end-limit positions are within the range
60° – 340° of revolution DCPT. Otherwise, after setting, an error arises
(LED 2x).
1.1. Position “4 mA”
Set the drive into the required position and press the push-button
“4” until LED blinks
(about 2 s)
.
1.2. Position “20 mA”
Set the drive into the required position and press the push-button
“20” until LED blinks
(about 2 s).
2. Setting of sense of rotation
The sense of rotation is specified by viewing from the side of the panel DCPT.
2.1. Rotating anti-clockwise
Press the push-button
“20”, then the push-button “4” and keep them depressed until LED blinks.
2.2. Rotating clockwise
Press the push-button
“4”, then the push-button “20” and keep them depressed until LED blinks.
When the sense of rotation is changed the end-limit positions “4 mA” and “20 mA” remain valid but the working
range
(track DCPT)
between these points is changed to a complement of the original working range. In this
way, the permitted working range can be exceeded
(LED 2x)
– it can be smaller than 60°.
3. Error messages
In case of an error the diode LED blinks an error code:
1x
Sensor position out of working range
2x
Working range incorrectly set
3x
Off the tolerance level of magnetic field
4x
Wrong parameters in EEPROM
5x
Wrong parameters in RAM
Содержание MODACT MOK 1000
Страница 2: ...ZPA Pe ky a s is certified company in accordance with ISO 90001 as amended...
Страница 37: ...NOTE...
Страница 38: ...NOTE...