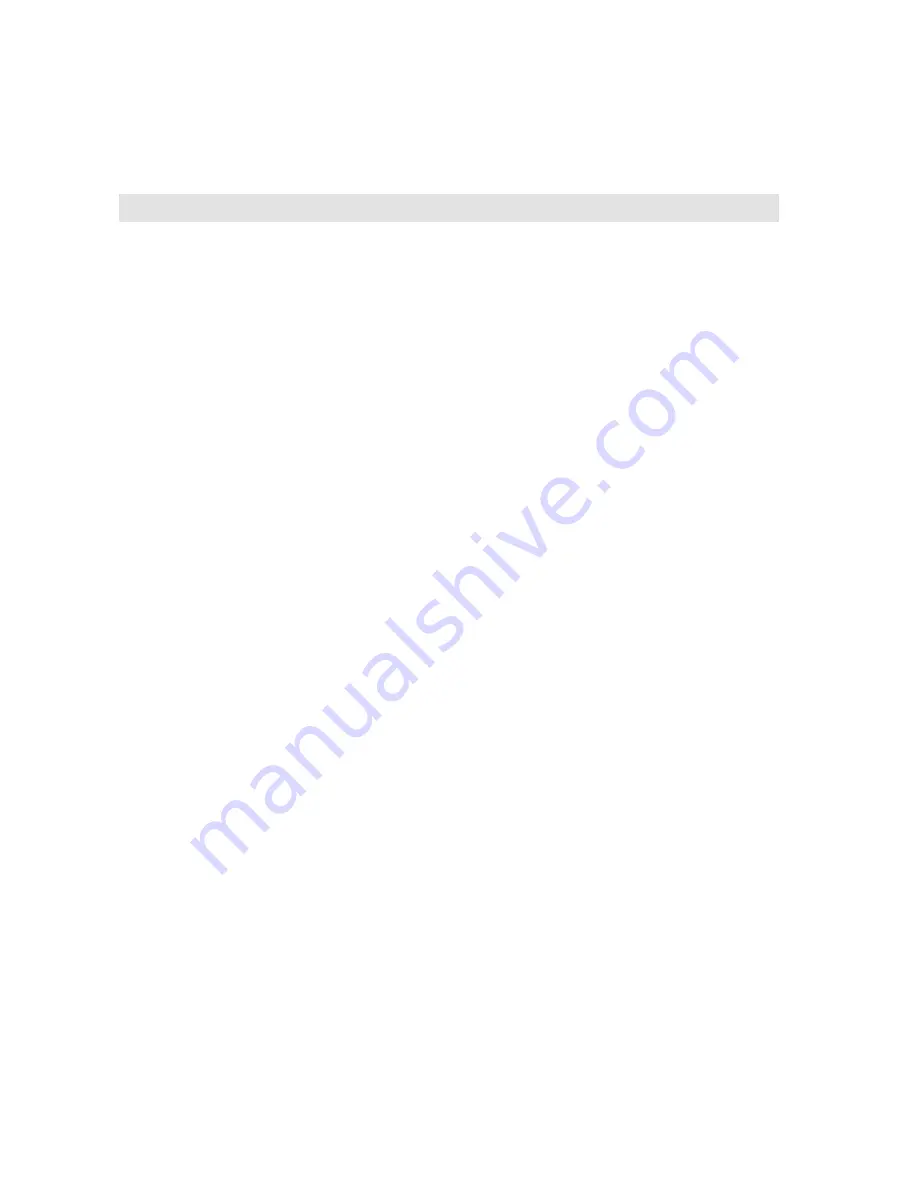
Attention!
Even after this switching off the actuator circuits are under voltage. Before any works on the actuator, e.g.
change of phase sequence in the actuator terminal board, the mains voltage should be disconnected.
Note:
In the auto-calibration regime the regulators ZP2 version 4 perform testing of the sense of rotation and report
the incorrect direction as an error. The sense of rotation is not tested in the regulation regime.
10. TECHNICAL PARAMETERS OF REGULATOR
Supply voltage
230 V +10 % -15 %, 50 – 60 Hz
Control signal
analog 0 – 20 mA, 4 – 20 mA, 0 – 10 V
logical – TEST, contact from the superior system
(simulation of breakdown situation)
– MO, MZ state of actuator limit switches *)
– TP state of thermal relay
Output signal
power outputs
2x relay 8 A, 230 V, protected by a fuse F1, 8 A
central breakdown
(KOK contact)
– pilot-light switch 24 V, 2 W
5x LED
( power supply, breakdown, setting, opening, closing)
brake
control signal 2 mA
(signal for additional module)
actuator position
PWM
(signal for additional module)
Position transmitter
current transmitter 4 – 20 mA **)
Regulator linearity
0.5 %
Regulator in-sensitivity
1 – 10 %
(adjustable)
Error messages
TEST mode
reaction transmitter failure limit switches are transposed *)
missing control signal actuator has been switched off by
a limit switch in the interposition *)
Respond to failure
reaction transmitter failure
actuator to Test position, error message
missing control signal
actuator to Test position, error message
TEST mode
actuator to Test position, error message
Setting elements
communication connector
(for computer connection)
2x button for setting parameters without a computer
Range of operating
temperatures
-25 °C – 75 °C
Dimensions
75 x 75 x 25 mm
*) A limit switch means a position switch or moment switch of actuator connected so that it can stop the actuator
motion in given direction. During the auto-calibration, the regulator ZP2 measures the reaction signal at which limit
switches switch off the actuator (for both motion directions) and stores it in the memory as the parameter. While
regulating, the limit switch status is being permanently monitored. If the actuator is switched off by the limit switch in
the position which does not correspond to the position ascertained during the auto-calibration, the regulator will
analyze this state to be an error. Such a state can occur e.g. when the moment switch is used as the limit switch
and valve seizes in the course of regulation.
**) If a two-wire current transmitter (e.g. CPT1 type) is used, the transmitter is supplied with the supply voltage
of 24Vss if the signal is brought out from the actuator it is active.
Setting of regulator parameters by functional push-buttons
After fitting the actuator with the regulator on the valve, proper function of the regulator is to be ensured by setting
parameters of the regulator and starting auto-calibration; this can be best carried out when the piping where
the valve with actuator is fitted is filled with process medium.
The regulator parameters can be set by push-buttons on the regulator
(the parameter being set is indicated by LED
diodes D3, D4 on the regulator)
or by PC connected to the regulator.
This manual serves as instructions for setting parameters of the regulator ZP2.RE version 4
(marking on the label
of the case of the regulator single-chip computer, e.g. EHL SERVO V4.28” 2004)
by push-buttons. Special instructions
are to be issued for setting the regulator by the computer
(the computer can also be used for setting other parameters
than those described in these instructions and various diagnostic data can be obtained).
15
Содержание MODACT MOK 1000
Страница 2: ...ZPA Pe ky a s is certified company in accordance with ISO 90001 as amended...
Страница 37: ...NOTE...
Страница 38: ...NOTE...