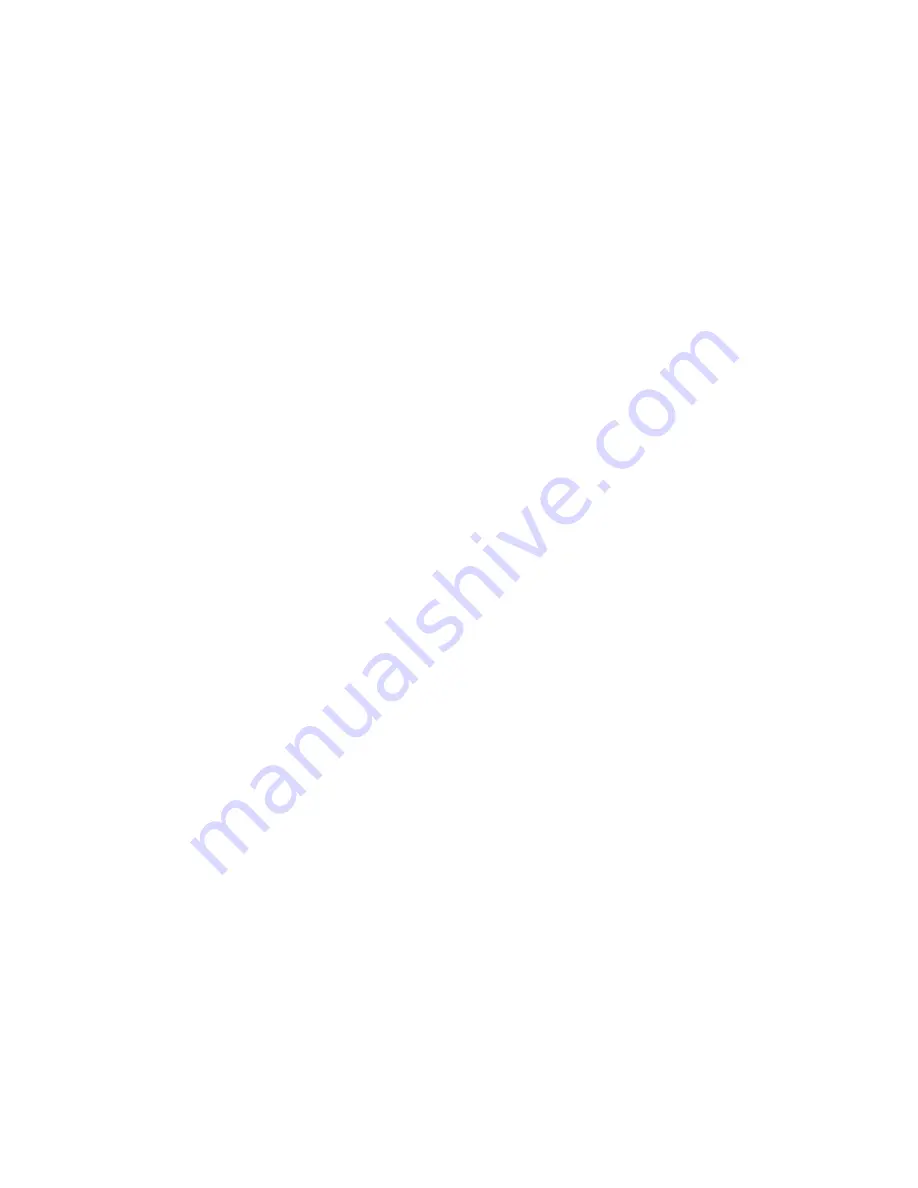
13
The microcomputer includes:
– A/D converters for input and feedback signals processing.
– Memory of parameters.
– Power supply source with mains transformer.
– Output relays for controlling the actuator
(they switch on the electric motor or power switches).
– Input circuits for connection of end micro-switches and contact of thermal relay.
– Circuits for input of analog signals.
– Push-buttons and signal lamps which can be used for entering parameters of regulation
(the signal lamps serve
also for indication of regulation state and type of errors).
– Connectors for connection of the regulator with the actuator.
– Connector for service connection of the regulator with PC.
The regulator has the following functions:
– Parameters of regulation can be entered by push-buttons on the regulator or from PC with is connected to
the regulator via a communication module.
– After entering the parameters of regulation, auto-calibration is accomplished during which the regulator is finding
parameters of the actuator and the valve.
– After auto-calibration has been completed, the regulator sores the entered and measured parameters into
the memory of parameters.
– Input and feedback signals and state of end micro-switches are checked.
– The actuator is controlled according to the input and feedback signals, state of end micro-switches, regulation
parameters and parameters of the actuator.
– It monitors and records into its memory of parameters total operation time and total number of closings of
the output relays.
– It ascertains whether, during regulation or setting the regulator, any failure occurs; if so, the type of failure
is evaluated and indicated; according to entered parameters, the regulator sets the actuator output shaft and stores
the parameters of the found-out failure into its memory.
– It provides for connecting PC which can be used for entering parameters of regulation and monitoring the regulator
operation.
The program memory is of ROM type, the memory of parameters of regulation and parameters of the actuator
is of EEPROM type; consequently, the memory content is not damaged by switching off mains voltage.
Speed of rotation of the actuator output shaft is given by the actuator type and variant; it cannot be influenced by
the regulator.
Connection of actuator with regulator and three-phase electric motor to mains voltage
The actuator with three-phase electric motor should be connected to mains voltage so that it is stable
during operation with regulator; i.e. if the actuator is in a balanced position and is brought out of this position
by an external intervention
(e.g. by the hand wheel)
it is automatically brought back to this balanced position
by action of the regulator. Therefore, a correct sequence of phases of mains voltage should be observed.
Moreover, position and moment switches of the actuator should be correctly connected so that drive of
the actuator is switched off by particular switch when either of the limit positions of the output shaft is reached
(unless switching off has already been performed by the regulator).
Attention:
If the actuator is connected to three-phase voltage with opposite phase sequence than that one with which
it has been set and tested, it starts to be unstable, i.e. the actuator output shaft is brought to one of its limit positions.
When the limit position is reached, the actuator electric motor is not switched off as, in this case, the limit micro-switch
acts on the contactor for motion in opposite direction. In this way, the actuator or the controlled valve can be damaged.
The sequence of phases can also be changed during repairs and modifications in circuits of distribution of
three-phase voltage for feeding actuators!
After the mains voltage is connected to the actuator, the actuator can spontaneously be started even
if control signal has not yet been connected to the regulator as the regulator has evaluated this state as an
error and the output shaft of the actuator is set according to the entered parameter.
In case that the connected mains voltage has opposite sequence of phases than that for which the actuator
has been set in the factory, the actuator does not stop even if the limit switches have been opened.
Therefore, during installing and putting the actuator into operation, measures should be adopted that
spontaneous starting of the actuator cannot happen even in case that mains voltage is accidentally switched
Содержание MODACT MOK 1000
Страница 2: ...ZPA Pe ky a s is certified company in accordance with ISO 90001 as amended...
Страница 37: ...NOTE...
Страница 38: ...NOTE...