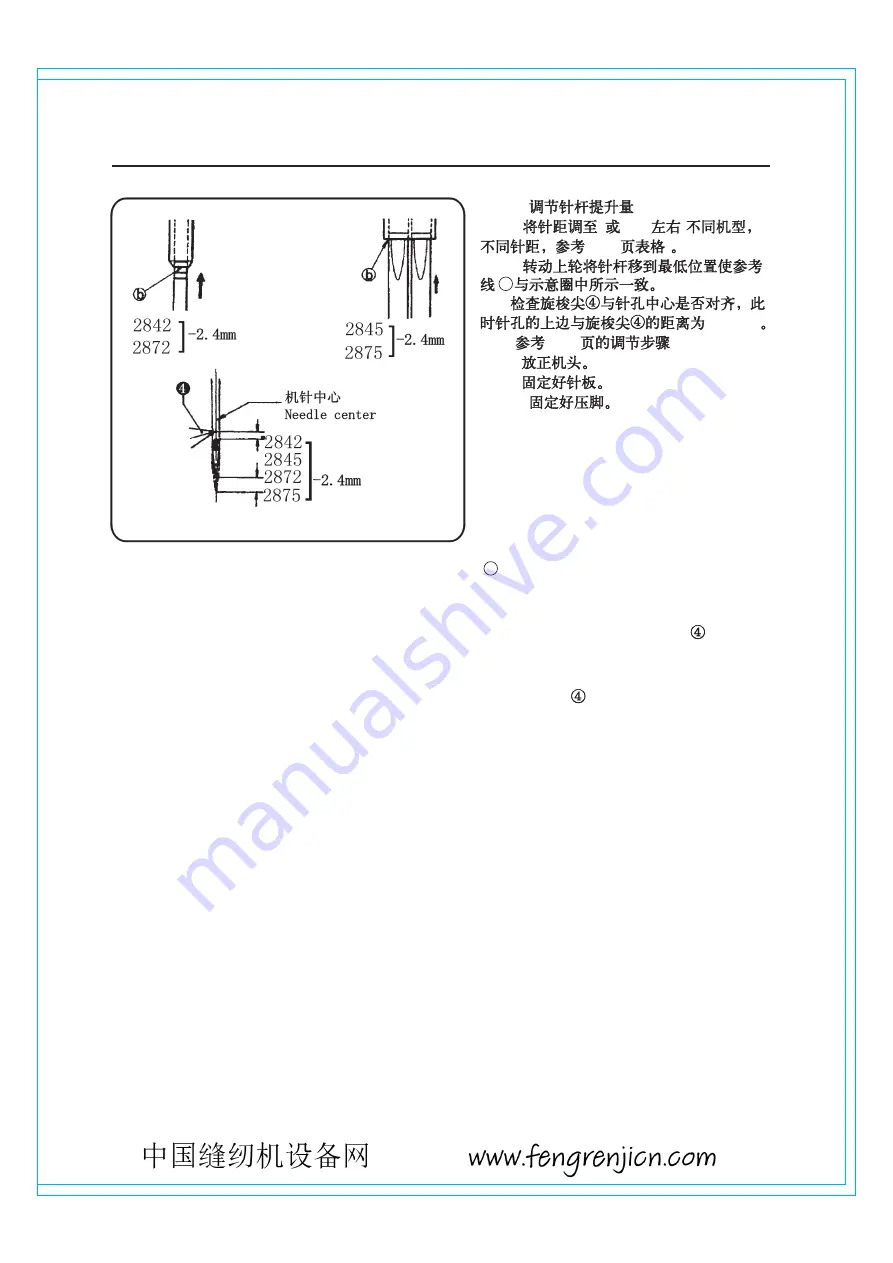
55
7. adjust the needle bar lift amount.
1) Set the stitch length to eight 2 ( approx.2
mm ) or 3 ( approx3ram ) on the scale,depending
on the model and specifications of the machine.
( Refer to the table on pages 33and34.)
2) turn the machine pulley to move the neelde
ar to its lowest position and adjust so that
reference line b is aligned as shown in the
illustration.
Check that the rotary hook tip
is aligned
with the center of the needle and that the distance
from the upper edge of the needle hole to the
rotary hook up
is 1-1.5mm at this time.
(Refer to pages 33 and 34 for the adjustment
procederes.)
8. Return the head to its original position.
9. Attach the needle plate.
10. Attach the presser foot.
7. adjust the needle bar lift amount.
1) Set the stitch length to eight 2 ( approx.2
mm ) or 3 ( approx3ram ) on the scale,depending
on the model and specifications of the machine.
( Refer to the table on pages 33and34.)
2) turn the machine pulley to move the neelde
ar to its lowest position and adjust so that
reference line b is aligned as shown in the
illustration.
Check that the rotary hook tip
is aligned
with the center of the needle and that the distance
from the upper edge of the needle hole to the
rotary hook up
is 1-1.5mm at this time.
(Refer to pages 33 and 34 for the adjustment
procederes.)
8. Return the head to its original position.
9. Attach the needle plate.
10. Attach the presser foot.
b
b
7.
1)
2
3mm
(
33-34
)
2)
1-1.5mm
(
33-34
)
8.
9.
10.
7.
1)
2
3mm
(
33-34
)
2)
1-1.5mm
(
33-34
)
8.
9.
10.
Содержание ZJ2842-BD
Страница 1: ......
Страница 2: ......
Страница 4: ......
Страница 6: ......
Страница 9: ......
Страница 10: ......
Страница 11: ......
Страница 15: ...2 ...
Страница 16: ...3 ...
Страница 17: ...4 ...
Страница 21: ...8 Kg Kg ...
Страница 23: ...10 ...
Страница 28: ...15 ...
Страница 52: ...39 ...
Страница 73: ...60 22 24 14 22 24 14 1 1 2 2 3 3 8 13 13 16 11 23 22 13 13 16 11 23 22 ...
Страница 75: ...62 2842 2872 2842 2872 4 4 5 5 6 6 2 6 2 6 13 13 16 21 2 5 13 13 16 21 2 5 32 16 25 20 21 16 25 20 21 ...