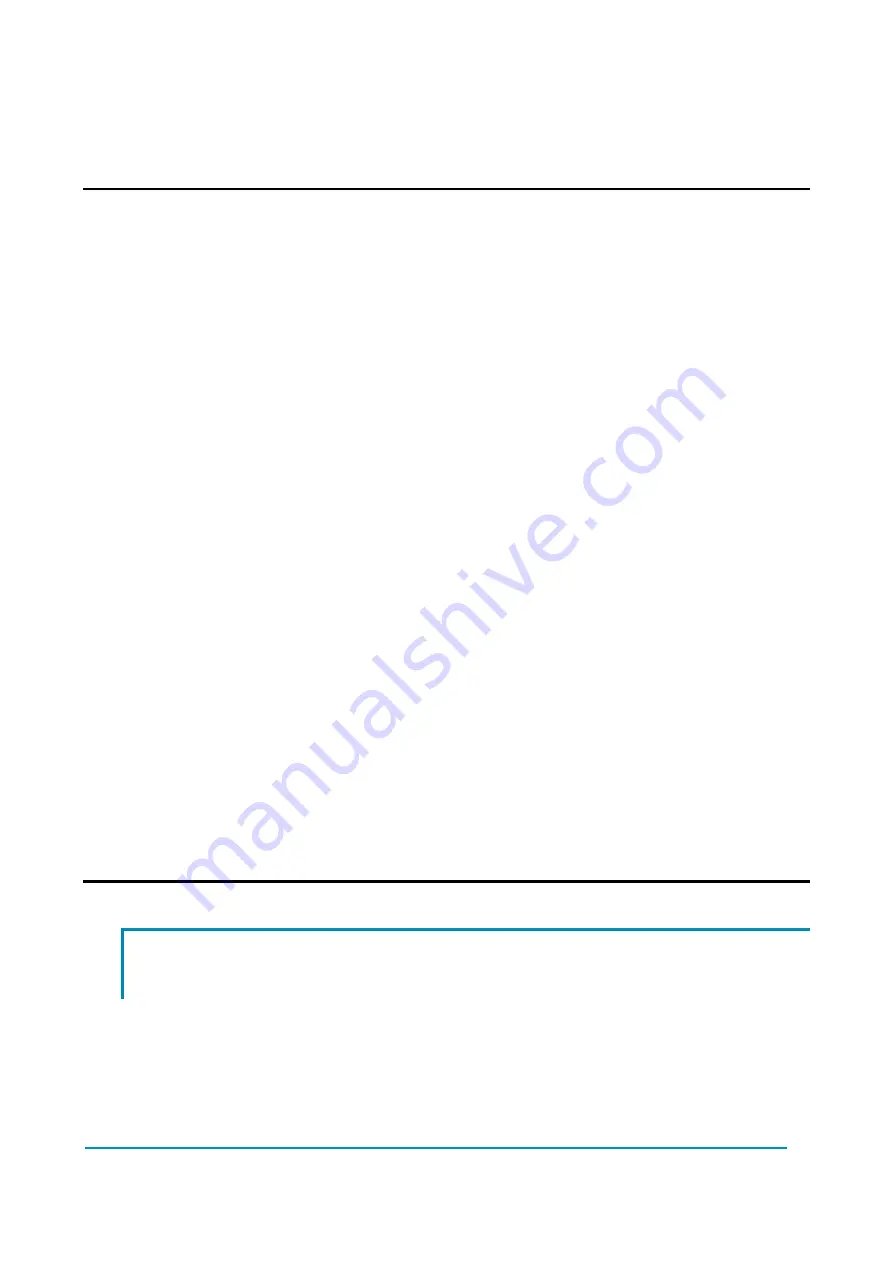
Page – 64/75
AFMNA0AA – EPS-BLI HYG – User Manual
11 SAFETY REQUIREMENTS &
RECOMMENDATIONS
U
According EN1175 and ISO13849, we consider the arrangement documented
in this manual suited to work in Manual Mode and Closed Loop Mode (target is
PLd and Category #3). Obviously, the lift truck manufacturer is responsible for
the final system and, to fulfill the norms, the lift truck manufacturer is called to
adopt special analysis, design principles and cares against the faults of the
components of the system that are not in charge of Zapi but affect the safety.
Particular attention must be paid for those of these components which cannot
be monitored/diagnosed by the Zapi assembly (let’s consider an example: the
shaft of the Steering handle is totally in charge of the Lift Truck manufacturer
and there is no chance the Zapi system can detect a failure in that component.
This component, in case fails to a loosened condition, compromises the
safety).
These analysis, design principles and cares pass through two steps:
1) The lift truck manufacturer, according its own FMEA can conclude that, a
fault in a component that is not redundant (and not covered by the diagnosis),
shall not lead to a loss of safety (no countermeasure required).
2) The lift truck manufacturer, according its own FMEA can conclude that, a
fault in a component that is not redundant (and not covered by the diagnosis),
shall lead to a loss of safety (a failure of that component must be avoided with
proper cares: fault exclusion case).
U
VERY IMPORTANT: among the components of the system that are not in
charge of Zapi there is the unit in the truck designated to lead the traction to a
safe state in case of an alarm in the steering system (typically a VMC = Vehicle
Master Control; but in general it can be any unit in the truck. In the next we
refer to this unit as a TMC = Traction Master Control). This is a major safety
issue and the LIFT TRUCK MANUFACTURER is responsible for coordinating
the communication between different suppliers and furthermore for testing
and validating that this alarm information will be properly handled in the
destination site and leading to a traction safe state when the steering system
is no longer operative. This problem is even more dramatic in case the unit
assigned to stop the traction IS NOT A ZAPI unit (see also 13.1).
11.1 Safety function of stopping the traction after an E-steering
controller alarm
In case of an alarm in the steering system, the role of the Zapi steering assembly
finishes when the STOP TRACTION REQUEST info (bit in a PDO) and the alarm code
(EMERGENCY or PDO frame) has been released on the CAN bus (see 10.1).