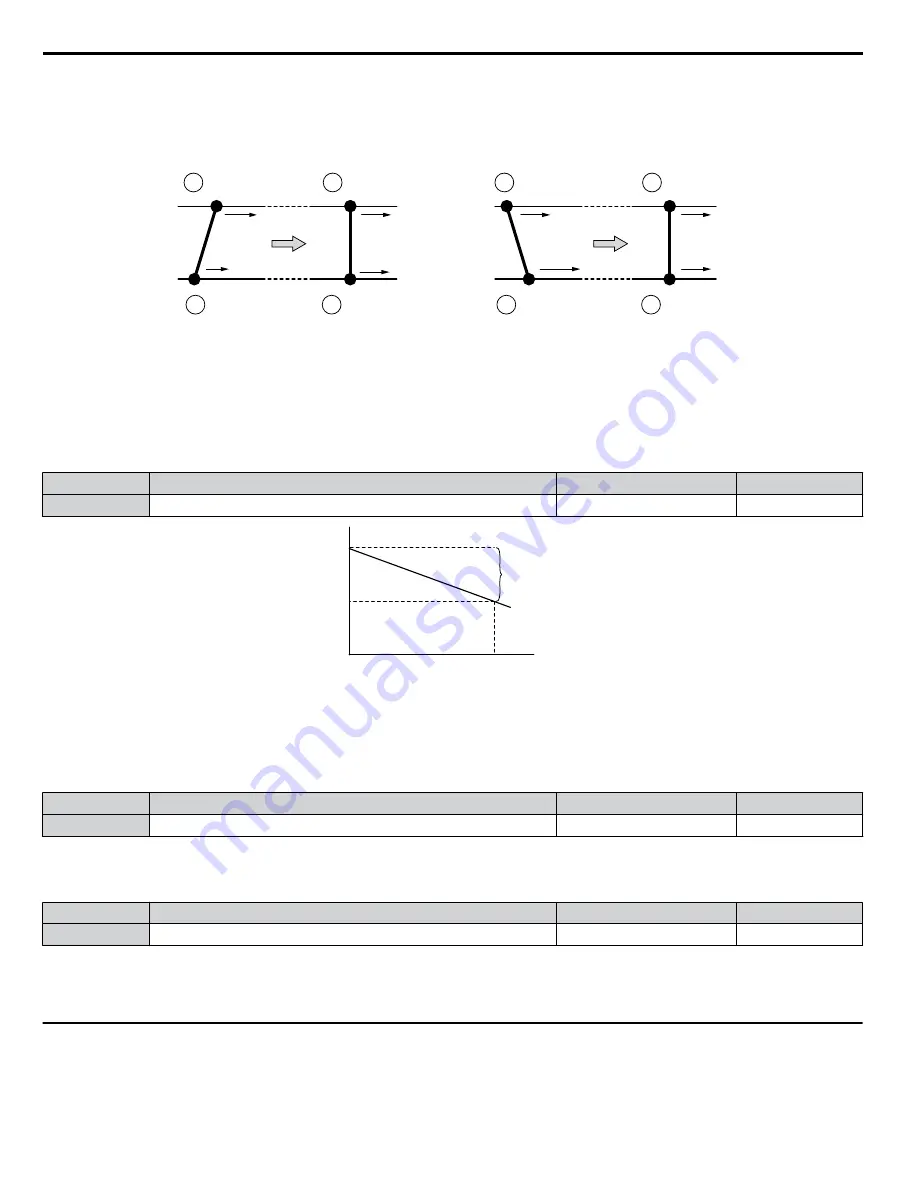
Droop control automatically balances the load level between two motors driving the same load. Droop control must be activated
in one of the drives controlling these motors. The drive in which Droop control is activated shifts the load from one motor to
another by automatically reducing the speed when the torque reference rises, and automatically increasing the speed when the
torque reference falls.
B
A
= 90% Load
= 90% Load
B
A
= 100% Load
= 80% Load
Droop Control increases the speed reference in
drive B accomplishing load balance
B
A
= 80% Load
= 100% Load
B
A
= 90% Load
= 90% Load
f
ref_A
= constant
f
ref_A
= constant
f
ref_B
increase
f
ref_B
decrease
Droop Control decreases the speed reference in
drive B accomplishing load balance
Motor A runs faster than B, pulling more load
Motor B runs faster than A, pulling more load
Figure 1.25 Droop Control Application
n
b7-01: Droop Control Gain
Sets the amount of speed reduction when the torque reference is 100%. The gain is set as a percentage of the maximum output
frequency. A setting of 0.0% disables the Droop control function.
No.
Parameter Name
Setting Range
Default
b7-01
Droop Control Gain
0.0 to 100.0%
0.0%
Speed
Torque
100%
Speed reference
Droop control gain
b7-01
0
Figure 1.26 Droop Control Gain
n
b7-02: Droop Control Delay Time
Adjusts the responsiveness of Droop control. Reduce the setting if the reaction time is too long, and increase the setting if
hunting occurs.
No.
Parameter Name
Setting Range
Default
b7-02
Droop Control Delay Time
0.03 to 2.00 s
0.05 s
n
b7-03: Droop Control Limit Selection
Enables or disables the droop control limit.
No.
Parameter Name
Setting Range
Default
b7-03
Droop Control Limit Selection
0, 1
1
Setting 0: Disabled
Setting 1: Enabled
u
b9: Zero Servo
The Zero Servo function is a position loop that can be used in CLV and CLV/PM control modes to lock the motor at a certain
position.
1.2 b: Application
44
YASKAWA ELECTRIC SIEP YEAHHP 01B YASKAWA AC Drive – A1000 HHP Programming Manual