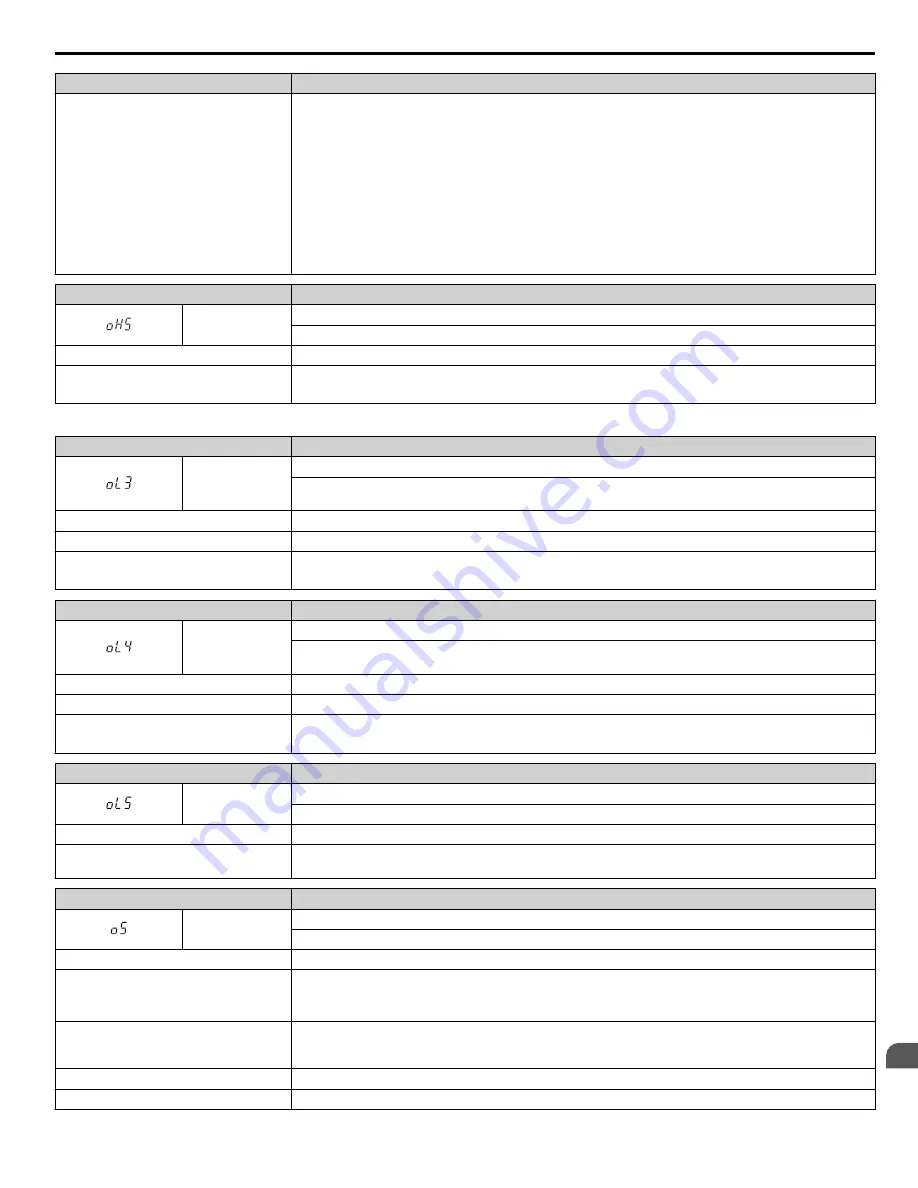
Digital Operator Display
Minor Fault Name
Motor has overheated.
• Check the load size, accel/decel times, and cycle times.
• Decrease the load.
• Increase accel and decel times (C1-01 to C1-08).
• Adjust the preset V/f pattern (E1-04 through E1-10). This involves reducing E1-08 and E1-10.
Note:
Refrain from lowering E1-08 and E1-10 excessively to prevent a reduction in load tolerance
at low speeds.
• Check the motor-rated current.
• Enter motor-rated current on motor nameplate (E2-01).
• Ensure the motor cooling system is operating normally.
• Repair or replace the motor cooling system.
Digital Operator Display
Minor Fault Name
oH5
Motor Overheat (NTC Input)
The motor temperature exceeded the level set to L1-16 (or L1-18 for motor 2)
Cause
Possible Solutions
Motor has overheated.
• Reduce the load.
• Check the ambient temperature.
Digital Operator Display
Minor Fault Name
oL3
Overtorque 1
Drive output current (or torque in OLV, CLV, AOLV/PM, and CLV/PM) was greater than L6-02 for longer
than the time set to L6-03.
Cause
Possible Solutions
Inappropriate parameter settings.
Check parameters L6-02 and L6-03.
There is a fault on the machine side (e.g.,
the machine is locked up).
• Check the status of the machine.
• Remove the cause of the fault.
Digital Operator Display
Minor Fault Name
oL4
Overtorque 2
Drive output current (or torque in OLV, CLV, AOLV/PM, CLV/PM) was greater than L6-05 for longer than
the time set to L6-06.
Cause
Possible Solutions
Parameter settings are not appropriate.
Check parameters L6-05 and L6-06.
There is a fault on the machine side (e.g.,
the machine is locked up).
• Check the status of the machine being used.
• Remove the cause of the fault.
Digital Operator Display
Minor Fault Name
oL5
Mechanical Weakening Detection 1
Overtorque occurred, matching the conditions specified in L6-08.
Cause
Possible Solutions
Overtorque occurred, triggering the
mechanical weakening level set to L6-08. Check for the cause of mechanical weakening.
Digital Operator Display
Minor Fault Name
oS
Overspeed
The motor speed feedback exceeded the F1-08 setting.
Cause
Possible Solutions
Overshoot is occurring.
• Increase the settings for C5-01 (Speed Control Proportional Gain 1) and reduce C5-02 (Speed Control
Integral Time 1).
• If using a Closed Loop Vector mode enable Feed Forward Control and perform Inertia Auto-Tuning.
Incorrect speed feedback scaling if terminal
RP is used as speed feedback input in V/f
control
• Set H6-02 to value of the speed feedback signal frequency when the motor runs at the maximum speed.
• Adjust the input signal using parameters H6-03 through H6-05.
Incorrect PG pulse number has been set
Check and correct parameter F1-01.
Inappropriate parameter settings.
Check the setting for the overspeed detection level and the overspeed detection time (F1-08 and F1-09).
2.5 Alarm Detection
YASKAWA ELECTRIC SIEP YEAHHP 01B YASKAWA AC Drive – A1000 HHP Programming Manual
209
2
Troubleshooting