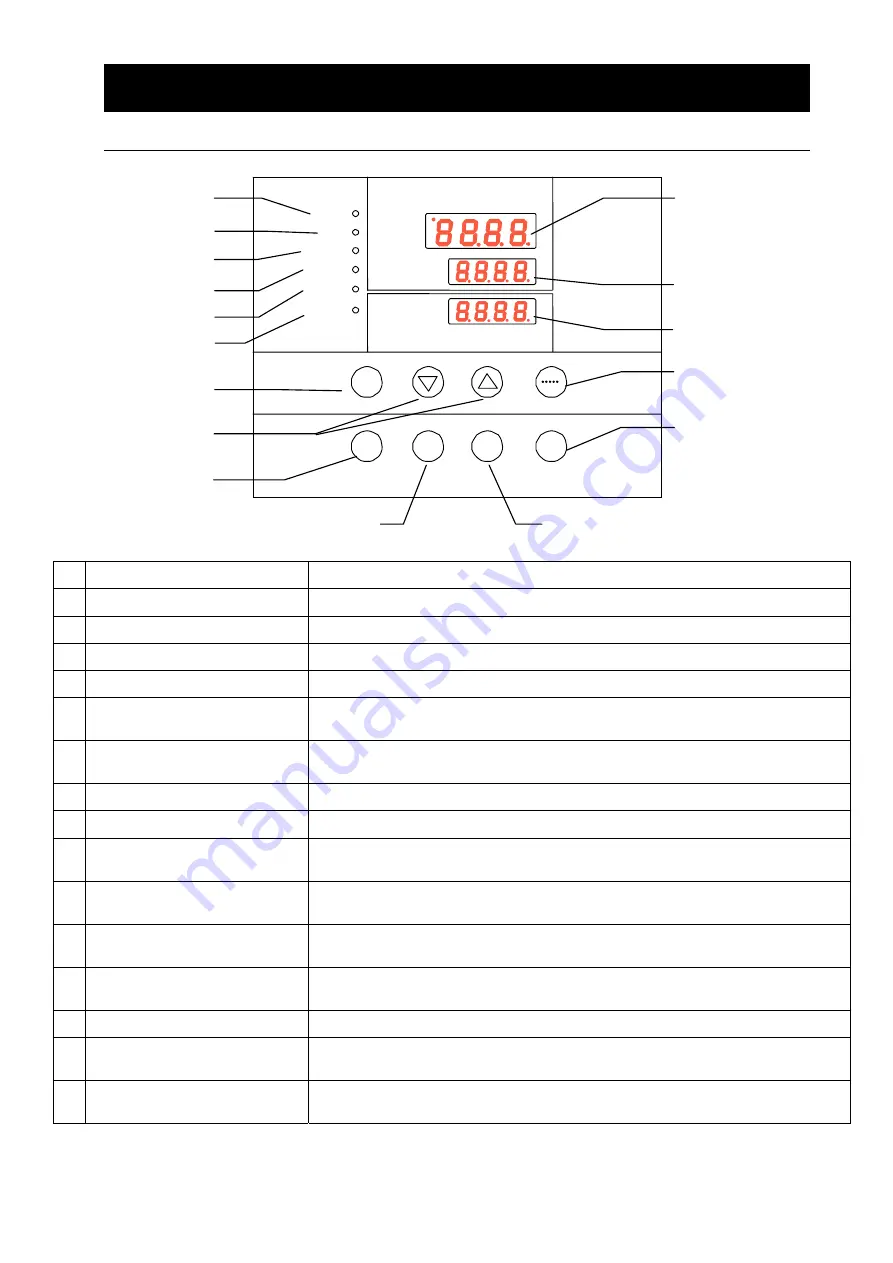
11
3.
Description and Function of Each Part
Operation Panel
①
START/STOP Key
Start/stop the operation.
②
▲▼ Key
Use for rising UP/lowering DOWN the setting value.
③
ENTER Key
Settle the inputted value.
④
FIXED TEMP Key
Choose the fixed temperature operation.
⑤
TIMER Key
Choose the timer operation (Quick Auto Stop/Auto Stop/Auto Start).
⑥
PROGRAM Key
Choose the program operation or program creation mode. (3 types and 6
modes programs)
⑦
SUBMENU Key
Use for setting the overheating prevention temperature, calibration offset
temperature, key lock function, or program repeat function.
⑧
HEATER Lamp
Light while the heater works.
⑨
ALARM Lamp
Light up when an error occurs. (Buzzer sounds simultaneously.)
⑩
AUTO STOP Lamp
Blink while setting quick auto stop timer or auto stop timer.
Light while quick auto stop timer or auto stop timer is running.
⑪
AUTO START Lamp
Blink while setting auto start timer.
Light while auto start timer is running.
⑫
FIXED TEMP Lamp
Blink while setting fixed temperature operation.
Light while fixed temperature operation is running.
⑬
PROGRAM Lamp
Blink while setting program operation.
Light while program operation is running.
⑭
Measurement Temp. Display
Display the measured temperature, setting character, alarm information.
⑮
Setting Temp. Display
Display the setting temperature, setting value for timer mode, remaining
time.
⑯
Overheating Prevention
Temp. Display
Display the setting temperature for overheating prevention device.
⑥
⑤
Measured temp.
℃
Heater
Alarm
Auto stop
Auto start
Enter
Set temp.
Over temp.
protector
Fixed temp.
Start
Program
Stop
Fixed temp.
Timer
Program
Submenu
①
⑦
⑯
⑮
⑭
⑧
⑨
⑩
⑪
⑫
③
②
④
⑬