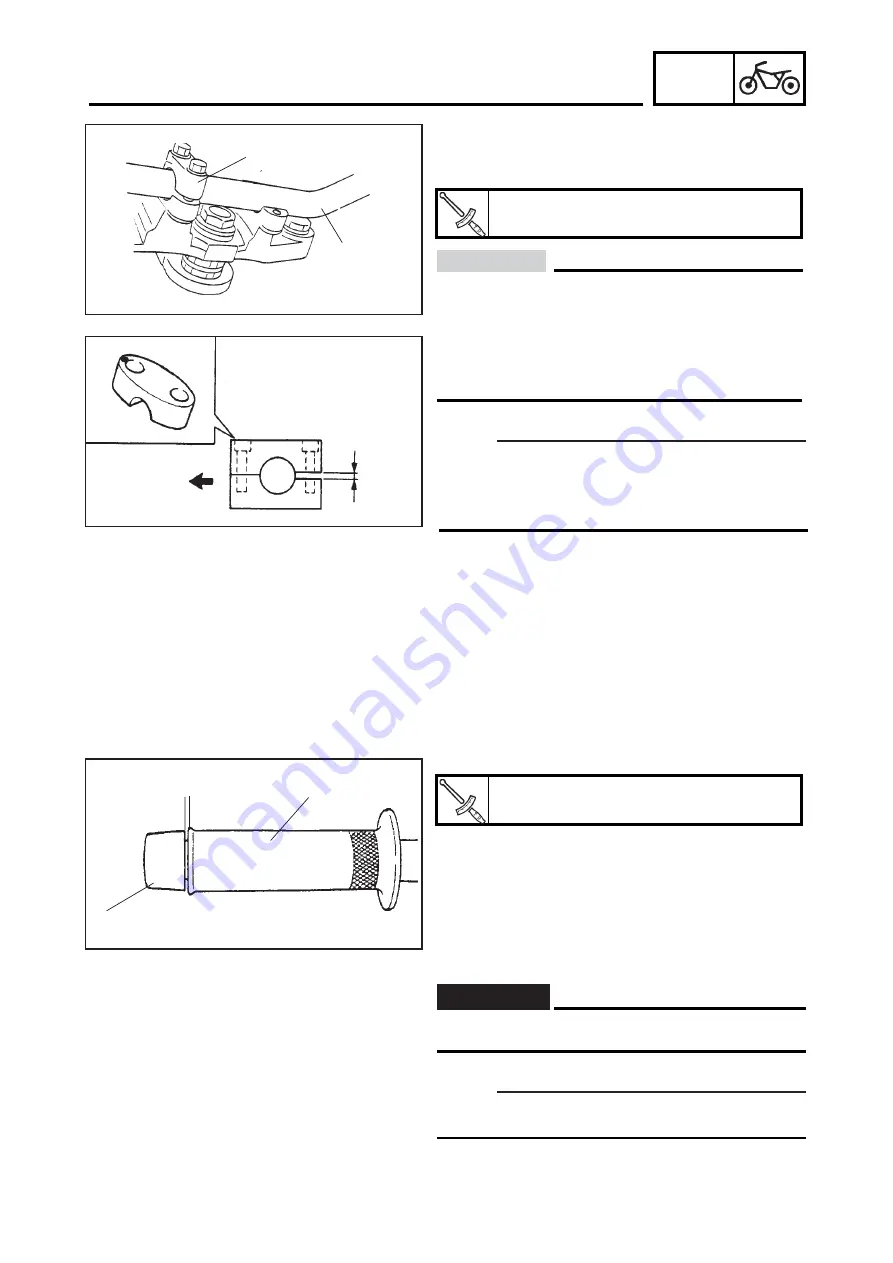
CHAS
HANDLEBAR
2. Install:
• handlebar
1
• handlebar upper holders
2
Handlebar upper holders
23 N.m (2.3 kgf.m, 17 ft.lb)
•
First, tighten the bolts on the front side of
the handlebar upper holder, and then the
rear side bolts.
•
Turn the handlebar completely to the left or
right. If there is any contact with the fuel
tank, adjust the handlebar position.
CAUTION:
3. Install:
• throttle grip
1
• grip end
2
Grip end bolt
4 N.m (0.4 kgf.m, 3.0 ft.lb)
TTTTTTTTTTTTTTTTTTTTTTTTTTTT
T
T
TTTTTT
T
T
T
T
a. Lubricate the handlebar left end with a thin coat
of rubber seal.
b. Slide the grip through the handlebar left end.
c. Wipe off any rubber seal excess with a clean
cloth.
Do not touch the handlebar lever until the
rubber seal is completely dry.
V
V
V
V
V
WARNING
T TT
T TT
T TT
T TT
T TT
T TT
T TT
T TT
T TT
T
T
T
T TT
T TT
T
T
T
T
There must be a 1 to 3 mm free play
a
between
the handlebar lever and its end.
NOTE:
4-57
1
2
a
b
Þ
a
1
2
•
The upper handlebar holders should be installed
with the arrow marks
a
facing forward.
•
Align the match marks
b
on the handlebar with
the upper surface of the lower handlebar holders.
NOTE:
Содержание YBR250 2007
Страница 1: ...YBR250 SERVICE MANUAL 5D1 F8197 E0 2007 ...
Страница 2: ......
Страница 359: ...YAMAHA MOTOR DA AMAZÔNIA LTDA ...