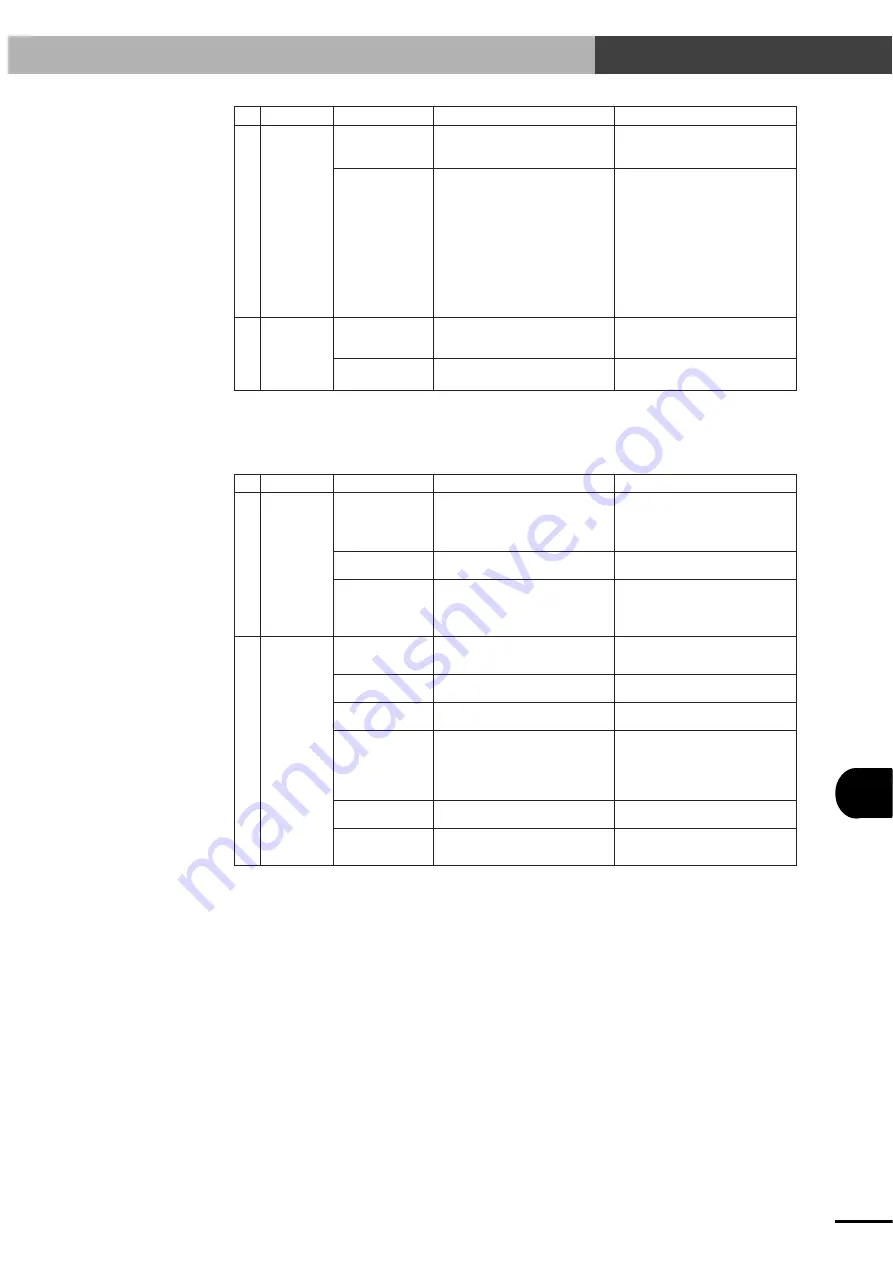
13-
9
13
TROUBLESHOOTING
13-3 Troubleshooting for Specific Symptom
Items to Check
• Check the motor wire and resolver
signal wire connections.
• Check whether the robot setting
displayed on the TPB matches the
robot actually used.
• Check the speed parameter (PRM17).
Action
• Correct the connections.
• Try Initialize the parameters.
• If they do not match, initialize the
parameters.
• Correct the parameter.
No.
7
8
Possible Cause
Motor and/or
resolver are
miswired.
Parameter error
Parameter setting
error
Speed setting was
changed.
1)
2)
1)
2)
Symptom
Robot starts
moving at high
speed when the
power is turned
on.
* The DRCX
controller has
a safety
circuit to
detect wire
breakage, but
check the
points listed
on the right
anyway.
Robot speed is
abnormally fast
or slow.
13-3-2 Relating to the I/O
Items to Check
• Check the wiring.
• Check the operation with the manual
instruction of the TPB general-purpose
output. (Refer to "7-4 Manual Control
of General-Purpose Output".)
• Connect the TPB and check the
program.
• Measure the voltage at the PLC input
terminal.
ON: 0.5V or less
OFF: +IN COM (+24V)
• Connect the TPB and check the
operation.
• Connect the TPB and check the
operation.
• Check that the signal pulse width is
50ms or more.
• After canceling emergency stop, allow
at least 200ms before inputting a
dedicated command before inputting a
dedicated command.
• Check the signal by using the TPB DIO
monitor.
• Check the signal input (by using a PLC
monitor, etc.).
Action
• Make the correct wiring by referring to
the connection diagram.
• Change the program.
• Replace the DRCX controller if the
output transistor is defective.
• Reperform return-to-origin.
• Eliminate the cause of error by
referring to the error message.
• Increase the signal pulse width ("on"
duration).
• Increase the delay time.
• Switch on the interlock signal.
• Turn off the dedicated command input.
No.
1
2
Possible Cause
Wiring to external
devices is
incorrect.
Misprogramming
Output transistor
is defective.
Return-to-origin
has not yet been
completed.
Program cannot be
run.
Signal pulse width
is too narrow.
Time interval
before inputting a
dedicated command
after canceling
emergency stop is
too short.
Interlock signal
remains off.
Another dedicated
command input is
on.
1)
2)
3)
1)
2)
3)
4)
5)
6)
Symptom
Output signal
cannot be
controlled.
* In cases other
than cause 2,
the output
signal cannot
be controlled
even with the
manual
instruction of
TPB general-
purpose output.
Robot will not
move even
with dedicated
command
input.
Artisan Technology Group - Quality Instrumentation ... Guaranteed | (888) 88-SOURCE | www.artisantg.com
Содержание DRCX
Страница 3: ...Artisan Technology Group Quality Instrumentation Guaranteed 888 88 SOURCE www artisantg com ...
Страница 9: ...vi MEMO Artisan Technology Group Quality Instrumentation Guaranteed 888 88 SOURCE www artisantg com ...
Страница 129: ...7 12 MEMO Artisan Technology Group Quality Instrumentation Guaranteed 888 88 SOURCE www artisantg com ...
Страница 207: ...9 16 MEMO Artisan Technology Group Quality Instrumentation Guaranteed 888 88 SOURCE www artisantg com ...
Страница 233: ...10 26 MEMO Artisan Technology Group Quality Instrumentation Guaranteed 888 88 SOURCE www artisantg com ...
Страница 281: ...12 10 MEMO Artisan Technology Group Quality Instrumentation Guaranteed 888 88 SOURCE www artisantg com ...
Страница 310: ...MEMO Artisan Technology Group Quality Instrumentation Guaranteed 888 88 SOURCE www artisantg com ...