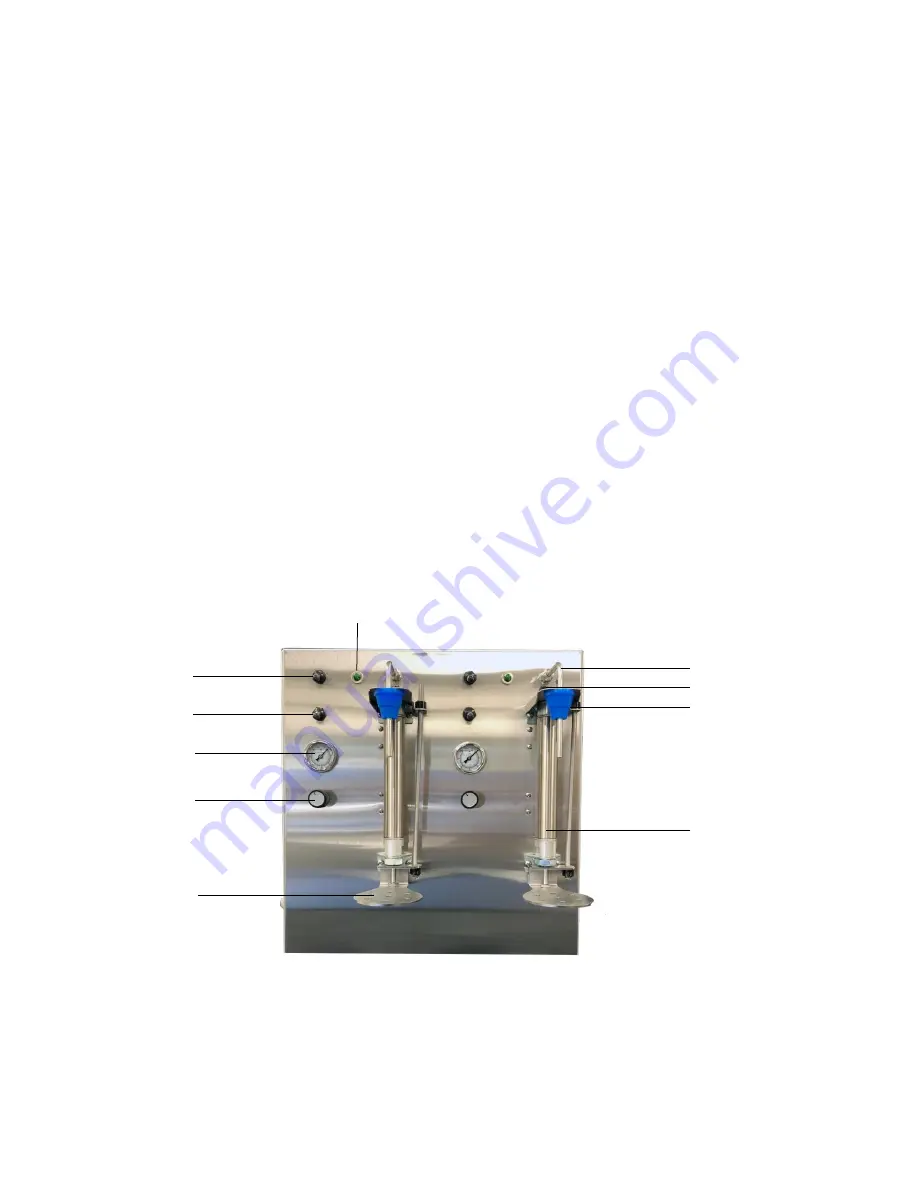
2
Know Your Filler
1. Fill indicator light
2. Fill sequence start / stop switch
3. Quick pressure release switch
4. Interior bottle pressure gauge
5. Interior bottle pressure adjustment knob
6. Bottle foot rest
7. Upper spout / product filling
8. Lower spout / pressurizing, venting & level sensing
9. Bottle neck filling stopper
10. Pneumatic ram
265 Prado Road, Suite 1 | San Luis Obispo, CA 93401 | 805.541.0100 | xpressfill.com | [email protected]
6
| XpressFill Systems LLC
The below diagram highlights the important features on your filler, which will be referenced throughout this manual.
Being familiar with each of these and their functions will make your filling experience easier.
1
2
3
4
5
6
7
8
9
10