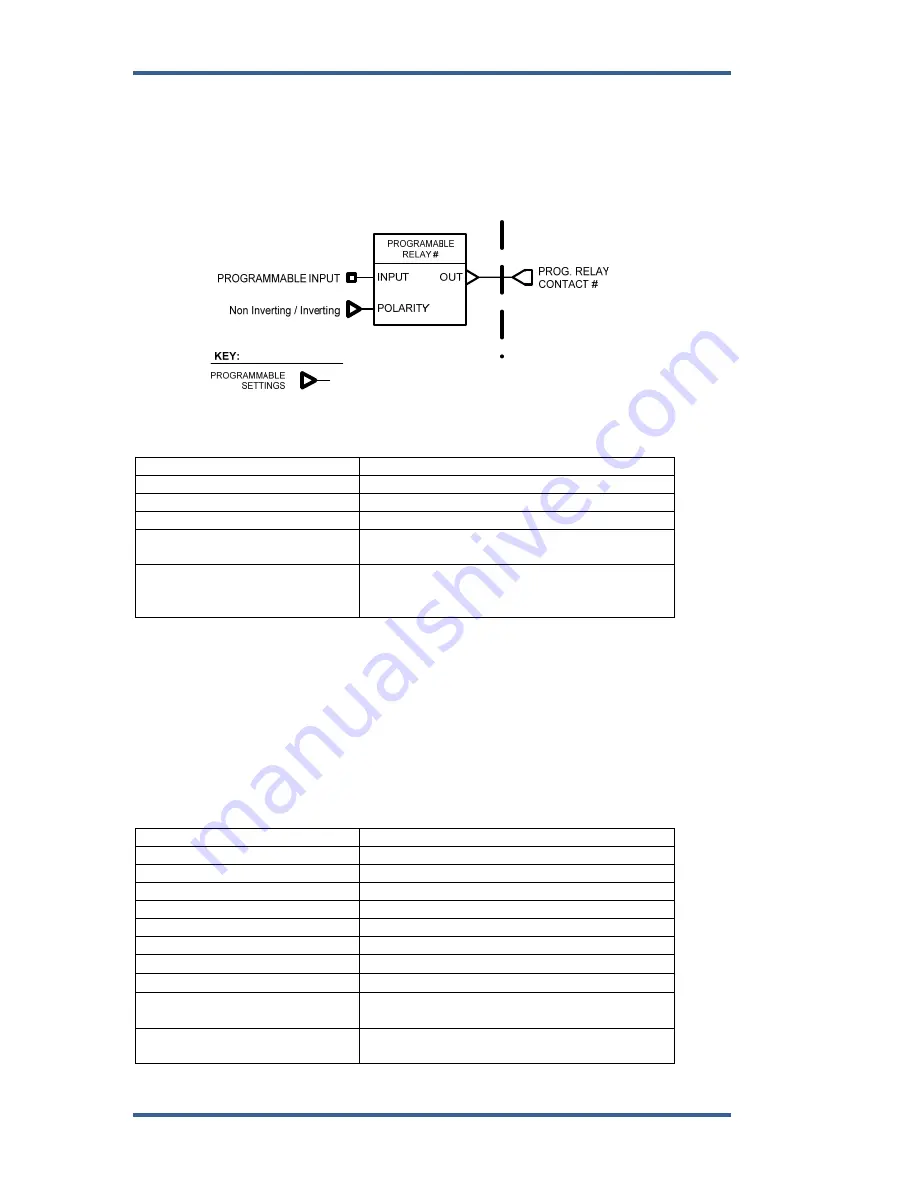
ProTechTPS Total Protection System
Manual 26710V1
68
Woodward
Configurable Relay Outputs
Each module has 3 configurable Relay Outputs. Each relay output can be
configured to reflect the state of any Boolean value within the module. Each
output can be configured to be inverting or non-inverting. If configured as
non-inverting, the relay will energize when the configured input is true. The first
configurable relay is defaulted to the output of the Alarm Latch.
Figure 3-12. Programmable Relay Output Diagram
Programmable Relay Output Specifications
Number of Channels
3
Output Type
SPST Solid-state, Normally Open
Current Rating
1 A
Voltage Rating
24 V (32 V max)
Isolation
500 Vac from output to chassis and output to
all other circuits
Signal Cable Length
Must be limited to 1000 ft / 305 m (low
capacitance
16 AWG / 1.3 mm²)
Table 3-6. Programmable Relay Output Specifications
Analog Output
A single 4–20 mA output is provided on each module to indicate the speed
sensed by that module. The 4–20 mA range can be configured to any speed
range desired. The accuracy of the analog output is better than ±0.5% of 20 mA
over the temperature range of the product.
Shielded twisted pair cable is required when connecting to the analog outputs.
Analog Output Specifications
Number of Channels
1
Output Type
4–20 mA, isolated
Max Current Output
25 mA
Accuracy
±0.1% at 25 °C, ±0.5% over temperature
Resolution 12
bit
Response Time
< 2 ms (2 to 20 mA)
Min Current Output
0 mA
Min Resistive
0
Max Resistive Load
500
at 25 mA
Isolation
500 Vac from output to chassis and output to
all other circuits
Signal Cable Length
Must be limited to 1000 ft / 305 m (low
capacitance 16 AWG / 1.3 mm²)
Table 3-7. Analog Output Specifications
Содержание ProTech TPS
Страница 36: ...ProTechTPS Total Protection System Manual 26710V1 34 Woodward Figure 2 7 Inside View of ProTechTPS ...
Страница 37: ...Manual 26710V1 ProTechTPS Total Protection System Woodward 35 Figure 2 8 ProTechTPS Control Wiring Diagram ...
Страница 62: ...ProTechTPS Total Protection System Manual 26710V1 60 Woodward Figure 3 8 Simplex Trip Block Assembly ...
Страница 63: ...Manual 26710V1 ProTechTPS Total Protection System Woodward 61 Figure 3 9 Dual Redundant Trip Block Assembly ...
Страница 74: ...ProTechTPS Total Protection System Manual 26710V1 72 Woodward Figure 3 14 Start Logic Diagram ...
Страница 122: ...ProTechTPS Total Protection System Manual 26710V1 120 Woodward Advanced Menu ...
Страница 124: ...ProTechTPS Total Protection System Manual 26710V1 122 Woodward Declarations ...