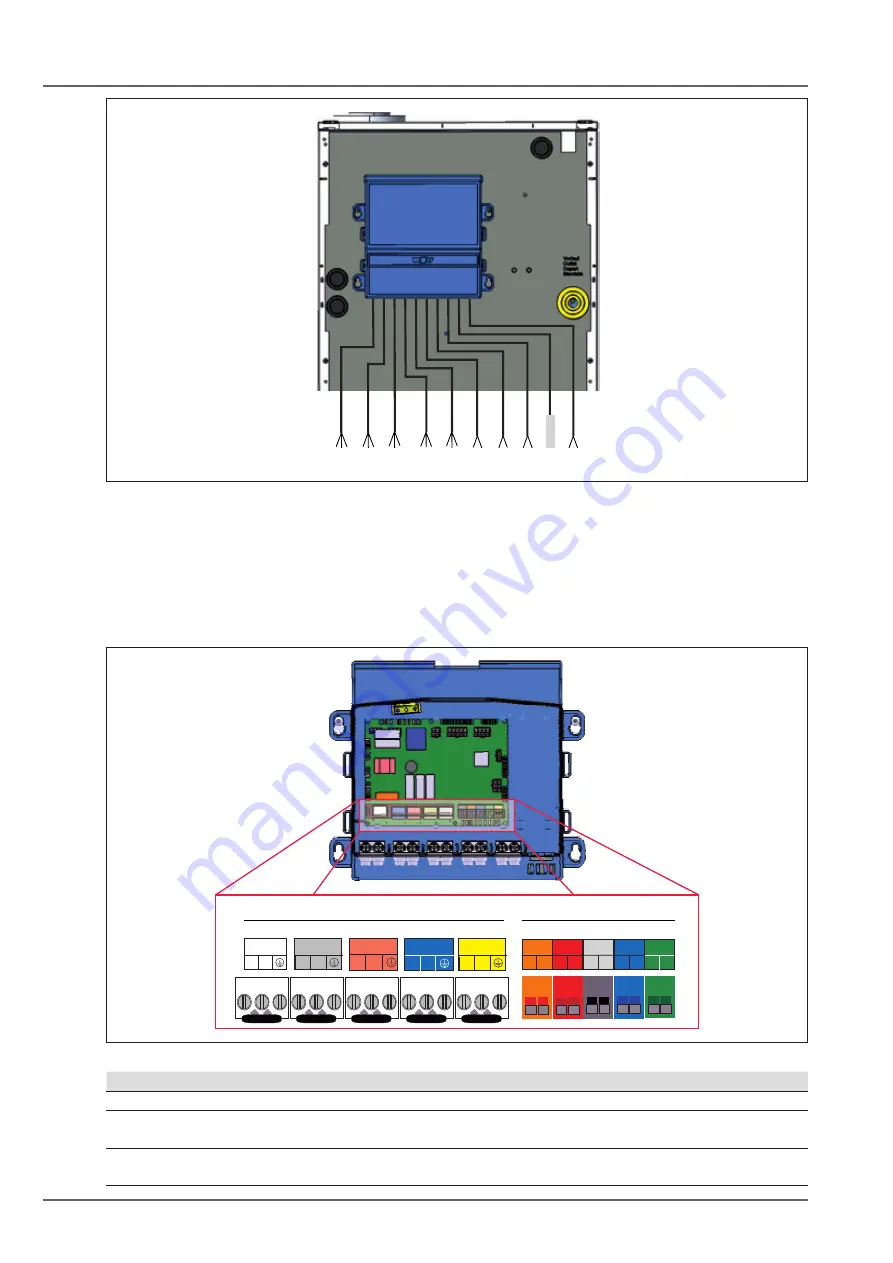
Installation
44 | WOLF GmbH 3066501_201910
Fig. 5.23 Terminal box electrical connection
q
Power supply 230 V
w
Z1 supply 230 V
e
Feed/heating circuit pump
r
Cylinder primary pump (PP)
t
A1 programmable output
y
E1 programmable input
u
E2 common sensor
i
Outside sensor
o
Cylinder sensor
a
eBus
Terminal assignment in terminal box
E2
a b
Netz
N
L1
Z1
N
L1
A1
N
L1
ZHP
N
L1
L1
LP
N
SF
1 2
AF
E1
eBUS
+
-
1 2
a b
1 2
1 2
1 2
1 2
1 2
E2
a b
230VAC
≤ 24 V
Fig. 5.24 Terminal box terminal assignment
Terminal
Explanation
Mains
Power supply
Z1
230 V output when ON/OFF switch is in the ON position
Maximum of 1.5 A per output, no more than 600 VA in total
ZHP (FHP) Feed / heating circuit pump control
Maximum of 1.5 A per output, no more than 600 VA in total