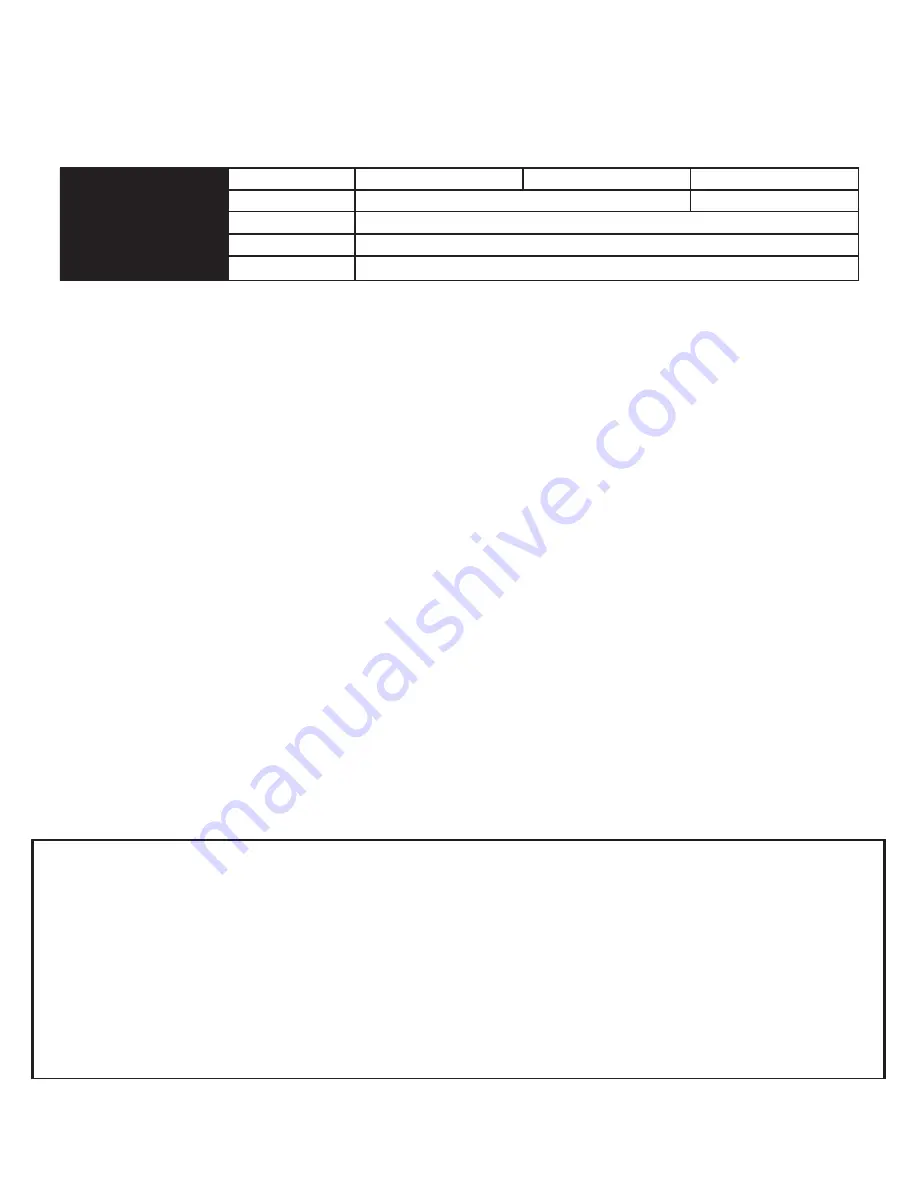
INSTALLING THE CONDENSING UNIT (continued)
Liquid Line King Valve
This location is used to charge the system with liquid refrigerant
and identify the high side pressure of the system.
Calculating Subcooling
To determine the subcooling of the system, calculate the difference between the
high side pressure of the system
(converted to temperature)
and the
temperature of the liquid line
. The temperature of the liquid line will be taken on
the exterior of the condensing unit, about 4" away from the housing.
*Saturation temp — liquid line temp
5
-15
°F
SUBCOOLING REQUIRED FOR WARRANTY APPROVAL
Ceiling Mount H.E. 9000/12000
Line Set Length
<25ft
26-50ft
50-100ft
Suction Line
Horizontal Tubing
5/8
”
3/4
”
Vertical Rise
5/8"
Liquid Line
Horizontal Tubing
3/8
”
Vertical Rise
3/8
”
•
Remove the nitrogen from the system
•
Remove the nitrogen tank from the manifold and attach the manifold to the vacuum pump
•
Install service caps on the valves.
•
After confirming that there is fresh oil in the vacuum pump, connect the hose from the manifold to the
pump.
•
Start the pump and run it until micron gauge reads
2
50 microns or less.
•
Once vacuum of
2
50 microns or less is achieved, d
isconnect the vacuum pump from the system.
•
Remove the micron gauge from the access valve.
•
Close the valves on the manifold
Pressure Test
After the line set has been connected securely to the evaporator and condensing unit, remove valve stem caps from low pressure
(suction) and high pressure (liquid) valves on condensing unit.
If desired, r
emove (schrader) valve cores from valves using valve core
removal tool
to pull vacuum faster
.
Ensure service valve stems are in the back-seated position.
If valve cores have been removed, they
should be reinstalled in valves after pressure testing, vacuum, and charging procedures are complete
.
Connect charge hoses of the manifold gauge to the service ports on the outdoor unit’s low pressure and high pressure valves. Leave
gauge manifold knobs in closed position until nitrogen is ready to be admitted into the system. Connect service hose from service
port on manifold to nitrogen regulator. Set nitrogen tank regulator to approximately
2
25
psi. Open both high side and low side gauge
manifold knobs SLOWLY at the same time to admit nitrogen into the system until the gauge manifold reads
225
psi, then close gauge
manifold knobs. Let pressure stand for minimum of 10 minutes. Use soapy solution to check flare connection points for leaks. If no
leaks are present and pressure is maintained after 10 minutes of pressure test
,
p
roceed with evacuation process. If any leak is
detected, it must be corrected before moving onto evac
u
ati
o
n process.
Air Evacuation/ Vacuum
Note:
For adjusting the service valves on the condensing unit a
3
/
16
" allen wrench is needed.
Line set piping size is determined by the unit size and the line set length. Determine the length before selecting the size.
For the vertical rise on the suction and liquid lines refer to the line set piping diagrams above. When the condensing unit is
mounted abo
ve
the evaporator unit
the liquid line needs to have
oil saving bends placed every 1
5'.
Line Set Piping Size
Page 35
08/04/21
Содержание Twin Ceiling Mount H.E. CM12000
Страница 29: ...CEILING MOUNT WIRING DIAGRAM KDT Page 27 08 04 21...
Страница 30: ...CEILING MOUNT WIRING DIAGRAM 24V Page 28 08 04 21...
Страница 31: ...CONDENSING UNIT WIRING DIAGRAM Page 29 08 04 21...
Страница 61: ...WhisperKOOL 1738 E Alpine Ave Stockton CA 95205 1 800 343 9463 www whisperkool com...