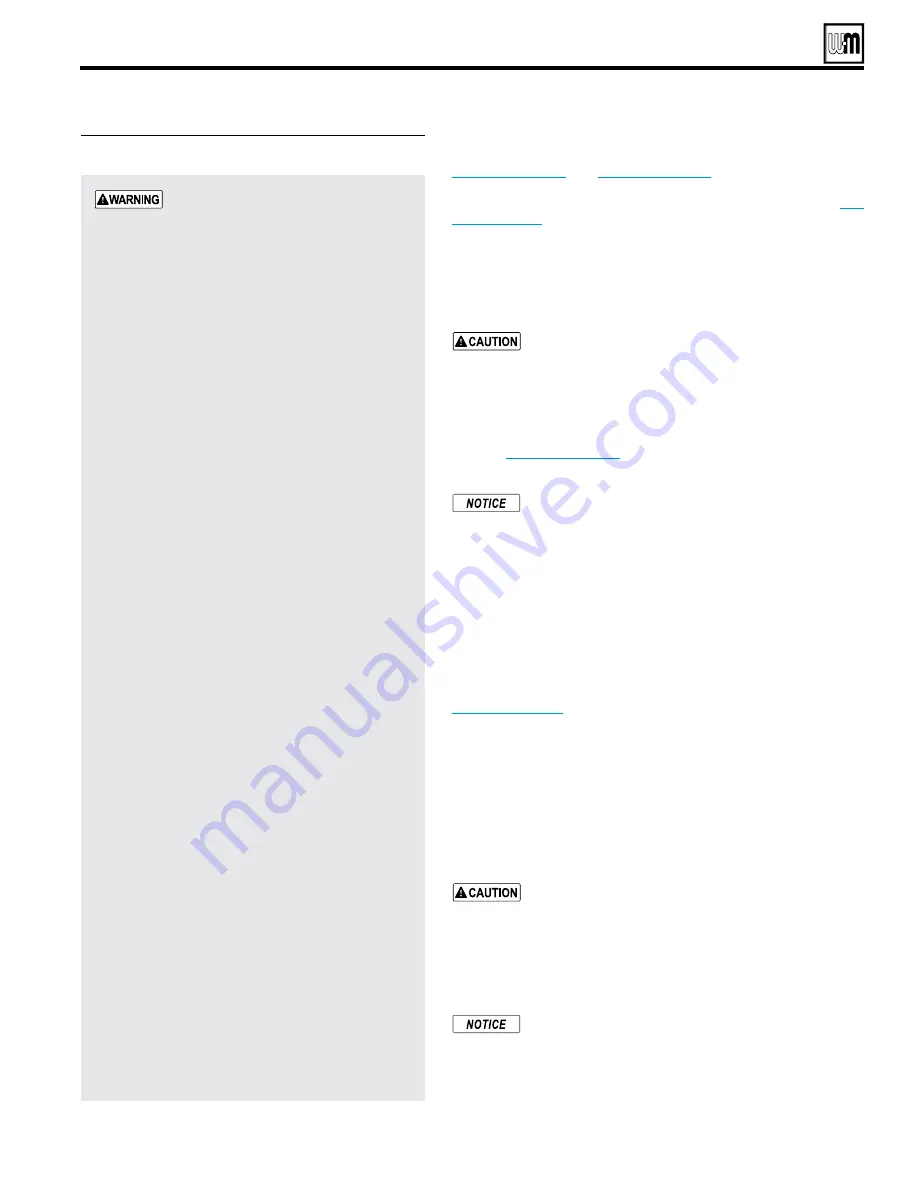
Part number 550-143-010/1021
13
GV90+
series
2
gas-fired water boiler – boiler manual
Figure 13
Relief valve installation guidelines
Install water piping
(continued)
To avoid water damage or scalding
due to relief valve operation, as per
local or state codes
:
Discharge line must be connected to re-
lief valve outlet and run to a safe place of
disposal. Terminate the discharge line in
a manner that will prevent possibility of
severe burns or property damage should
the valve discharge.
Discharge line must be as short as pos-
sible and be the same size as the valve
discharge connection throughout its
entire length.
Discharge line must pitch downward
from the valve and terminate at least
6” above the floor drain where any dis-
charge will be clearly visible.
The discharge line shall terminate plain,
not threaded, with a material serviceable
for temperatures of 375°F or greater.
Do not pipe the discharge to any place
where freezing could occur.
No shutoff valve shall be installed be-
tween the relief valve and boiler, or in
the discharge line. Do not plug or place
any obstruction in the discharge line.
Test the operation of the valve after fill-
ing and pressurizing system by lifting
the lever. Make sure the valve discharges
freely. If the valve fails to operate cor-
rectly, replace it with a new relief valve.
Failure to comply with the above guide-
lines could result in failure of the relief
valve to operate, resulting in possibility
of severe personal injury, death or sub-
stantial property damage.
Expansion tank
and
show typical installation
of the expansion tank. Always locate the air separator and expansion
tank as shown in the suggested piping drawings, beginning with
.
Ensure that the expansion tank size will handle boiler and system water
volume and temperature. See tank manufacturer’s instructions and rat-
ings for details. Additional tanks may be added to the system if needed
to handle the expansion. These tanks may be installed by connecting
to tees in the system piping.
Undersized expansion tanks
cause system water to be
lost from the relief valve and makeup water to be added
through the fill valve. Eventual section failure can result.
Always locate the
cold water fill connection
at the ex-
pansion tank. Never locate this elsewhere in the system.
Diaphragm- or bladder-type tank:
Refer to
for suggested piping when using a dia-
phragm- or bladder-type expansion tank.
Diaphragm- or bladder-type expansion tank
— Con-
trol
fill pressure
with the tank air charge pressure. Al-
ways check pressure and charge tank
with tank removed
from system
to be sure reading is accurate. Boiler relief
valve is set for 30 PSIG. Operating pressure of system,
after temperature expansion above cold fill pressure,
should not exceed 24 PSIG to avoid weeping of relief
valve.
Install an
automatic air vent
on top of the air separator, per separator
manufacturer’s instructions.
Closed-type expansion tank:
shows suggested piping when using a closed-type
expansion tank, in which the air is directly in contact with tank water.
Connect piping (½” or ¾”) from the air separator top outlet to the tank
fitting. Slope any horizontal piping a minimum of 1 inch per 5 feet of
horizontal pipe.
Always use a
tank fitting
, such as the B&G
Tank-trol
or Taco
Taco-
Trol
(shown). The fitting reduces gravity flow of water in the piping to
the tank, avoids air bubbling through the tank water, and provides the
proper fill height in the tank.
Correct all leaks
in the system or tank piping. Leaks
allow air to escape from the system and will cause water-
logging of the tank. This will result in water loss through
the boiler relief valve due to over-pressurization.
NEVER
use an automatic air vent in a system equipped
with a closed-type expansion tank. The air removed from
the system will cause water-logging of the expansion tank.
Closed-type expansion tank
— Follow tank manu-
facturer’s instructions for
filling the tank
. Typical tank
sizing provides for approximately 12 PSIG when the tank
is filled to the normal level and system water is cold. Note
that boiler relief valve is set for 30 PSIG. Operating pres-
sure of system, after temperature expansion above cold
fill pressure, should not exceed 24 PSIG to avoid weeping
of relief valve.