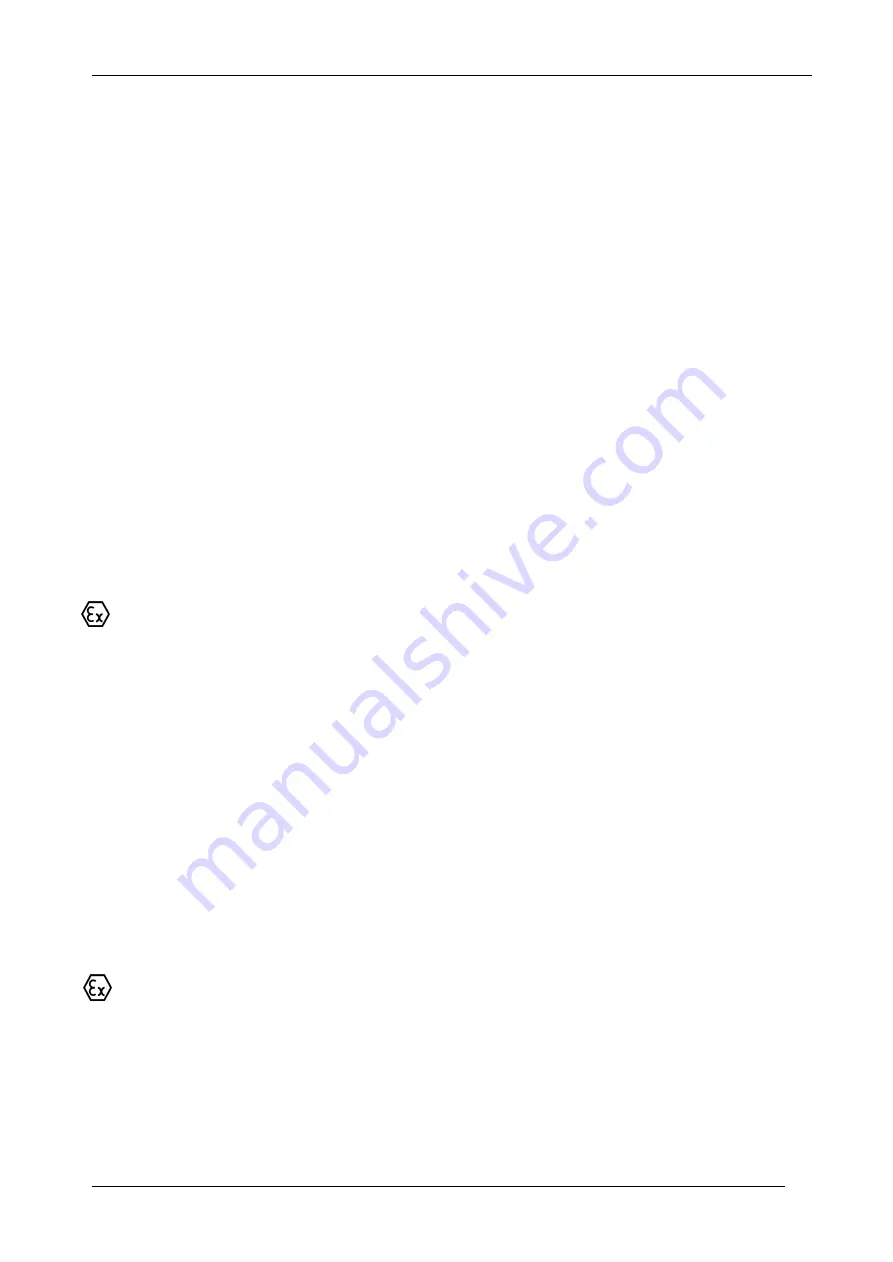
20
To avoid that maximum allowed surface temperature is exceeded, thermal
protectors of main and auxiliary motors must be connected to suitable
protection devices and, if protectors are Pt100 or thermocouples, trip
temperatures must be regulated to the values indicated by WEGeuro.
7. MAINTENANCE
7.1
The motors which are not fitted with grease nipples are equipped with bearings
with lubrication for life that is 20.000 working hours under normal conditions.
The type, quantities of grease and the respective lubrication intervals for normal
working conditions are shown on the nameplate. The addition of grease should
be carried out with the motor running and in compliance with safety procedures.
For heavy working conditions, such as high levels of humidity and pollution,
excessive loads on the bearings, excessive levels of vibration, the grease
lubrication intervals should be reduced.
7.2
Every two years the motors should be opened and the bearings should be
checked, and replaced, if necessary.
For heavy working conditions this interval should be shortened.
7.3
The air inlets and the cooling surfaces shall be cleaned periodically. The
intervals depend on the degree of pollution/accumulation of dust in the air.
7.4
The maintenance of flameproof motors is particularly important, as:
•
Any changing to the bearings could:
- cause a sudden temperature rise, thus presenting a risk of explosion
- increase the clearance between the shaft and the bearing plate, due
to friction of the shaft on the closing plate; an internal ignition may
spread to the outside and can cause an explosion
•
Concerning external ventilation, a fault in the cooling system raises the
surface temperature, which could reach values higher than those
established for the temperature class.
•
The temperature class should be checked on the certification plate; this
indicates the maximum temperature as follows:
T3 / 200ºC ; T4 / 135ºC ; T5 / 100ºC ; T6 / 85ºC
8. ASSEMBLING AND DISASSEMBLING
This type of motors requires a special care. Particularly when assembling and
disassembling parts are carried out, the condition of the joints should be
checked. The dimensions of the joints, i.e. length and clearance, have been
100% controlled during production of the motors. The joints must not be
changed and you need to:
- Ensure that the joints are not damaged and do not have cuts or dents.
If this happens the parts should be replaced.