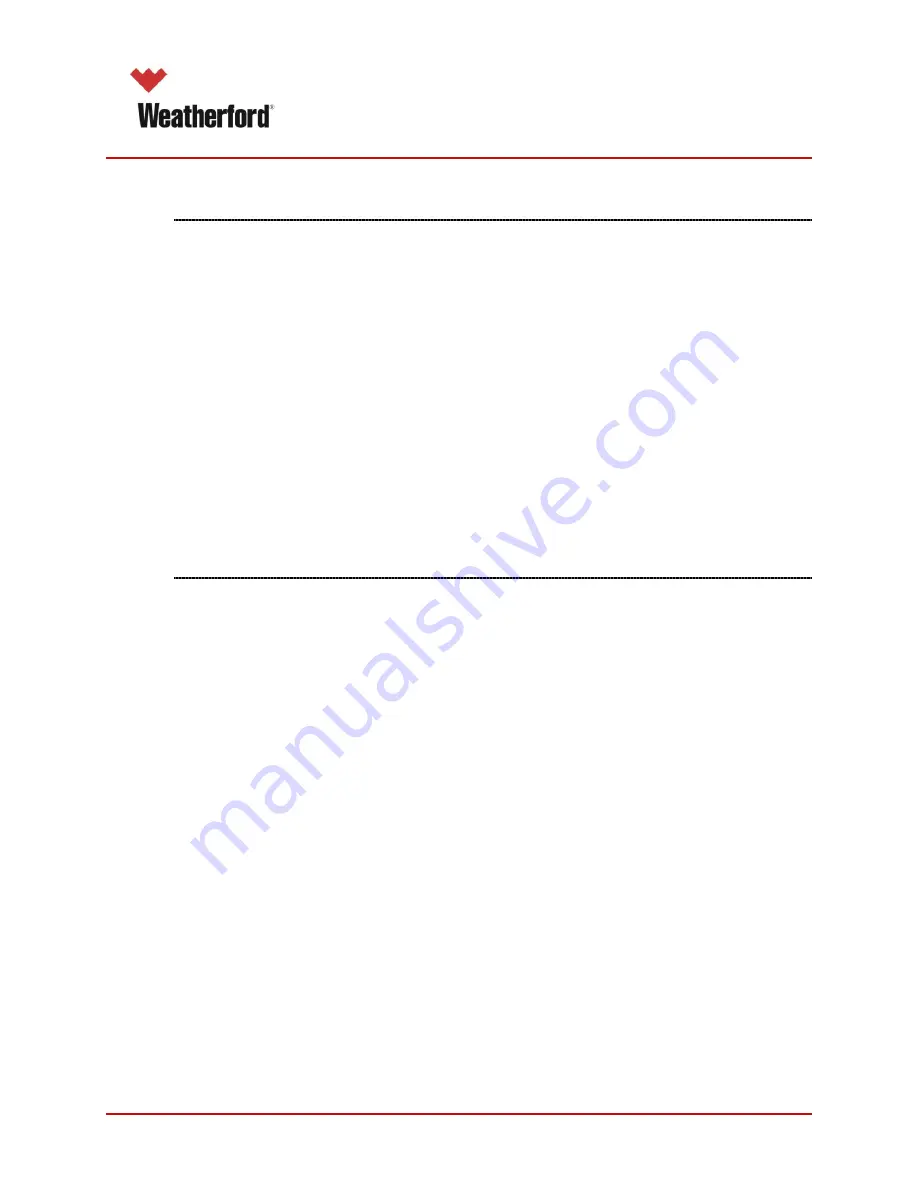
Pump and Fluid Systems
Chapter 5: Assembly/Disassembly
weatherford.com
33
MP-16 2-Piece 5000 psi January 2013
4.4.4
Semiannual Maintenance Checklist
□
Drain and flush the oil reservoir and clean power end oil sump and the settling area under
the crossheads. Then refill with fresh EP gear oil of the proper grade for the operation.
□
Clean or replace filter element in breather cap and suction screen.
□
Clean the magnet on the oil pump strainer area.
□
Ensure that all lubrication lines are in position, continuous and free of obstructions.
□
Clean the foundation and/or the hold down bolts, and ensure the pump is properly
oriented and secure to the skid.
□
Ensure that the bolting on suction and discharge flanges is secure.
□
Check the pinion sheave and bushing for wear and tear. Replace as needed.
□
Change the liner wash fluid. The fluid should also be flushed every time the pump is
moved and refilled before the drilling resumes.
4.4.5
Annual Maintenance Checklist
□
Check the crosshead guides for grooves, which indicate improper lubrication or foreign
matter in the lube oil. If found, check the lubrication system and the condition of the
crosshead extension rod seals, and replace if severely worn or scarred.
□
Check the clearance of the crossheads and the main gears, and record the data for
future reference.
□
Inspect the condition of the main gear and pinion gear teeth, as per the Pinion and Main
Gear section under 4.2.1: Initial Operations Maintenance.
□
Check the clearance of the bearings, and record the data for future reference. If bearing
clearance exceeds two times the installed clearance, repairs should be made. If
clearance has increased abnormally, a more thorough inspection should be made to
locate the source of the wear.
□
Check the tightness of the main frame mounting bolts and wristpin retainer bolts.
□
Check all bolting safety wires. If broken, identify cause and correct before replacing.
□
Check the tightness of the main bearing cap bolts and tighten as necessary. Units with
“super bolts” will have the required torque stamped on top of the nut.