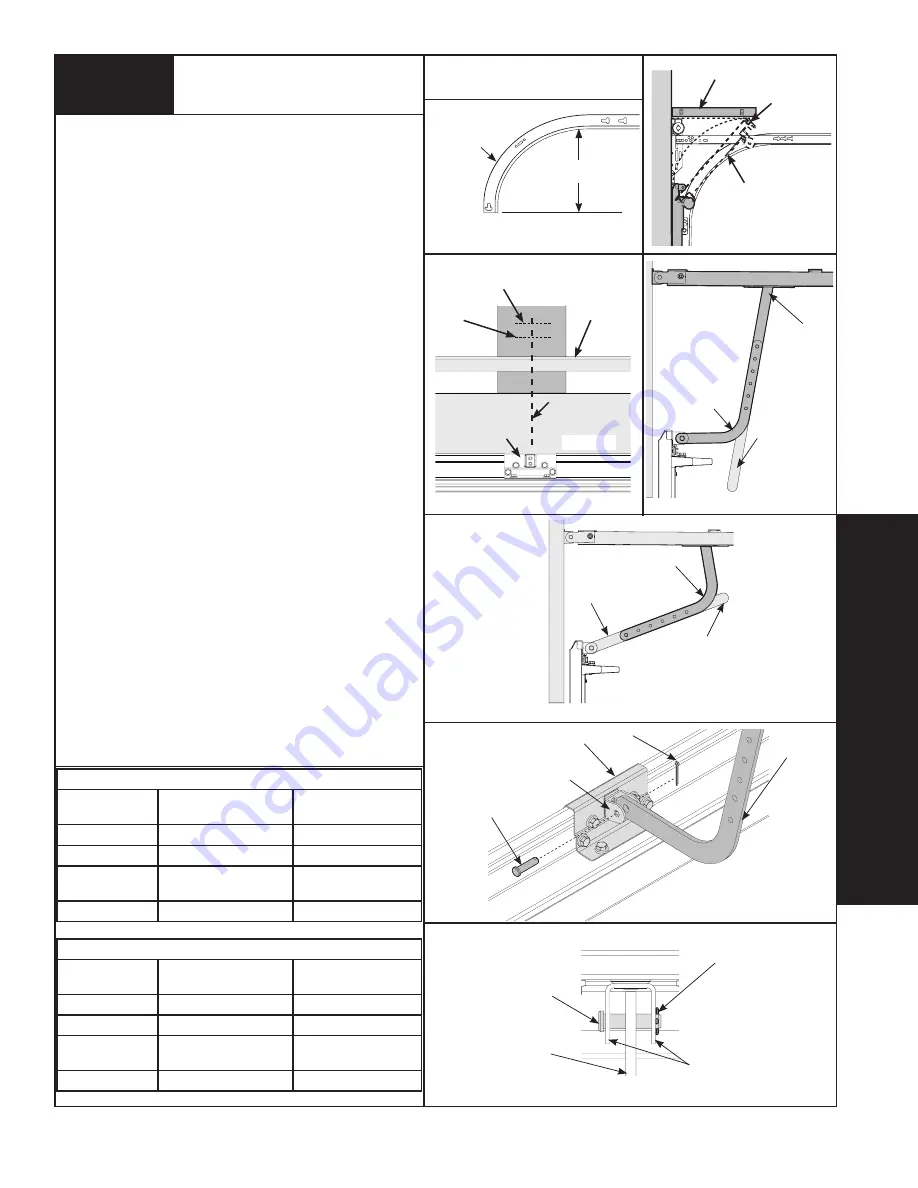
33
Please Do Not Return This Product To The Store.
Contact your local Wayne-Dalton dealer.
To find your Wayne-Dalton dealer; refer to your local yellow pages / business listings or go to Find a dealer area online at
www.wayne-dalton.com
OPTIONA
l
INST
All
ATION
Hairpin Cotter
operator BraCket
Door
arm
5/16” x 1-1/4”
Clevis pin
operator
BraCket taBs
Door arm
top view
Hairpin Cotter
(outsiDe of operator
BraCket taB)
operator BraCket
taBs
FIG. 2.6
DETERMINE ThE wAyNE-DAlTON
TRACk RADIUS bEINg USED:
Trolley Installation for
Standard lift
Measure the curved ends of the horizontal track
to
determine
if you have a 12” or 15” radius horizontal track,
as shown
in FIG. 2.1
. Determine center line of door. Mark vertical line
at this point, on the header wall. Raise the door slightly until
the top section reaches the highest point of travel (high arc)
.
using a level, mark this high arc point of travel on the header
wall
, intersecting the vertical center line, as shown in FIG.
2.2 through 2.3.
hold the wall bracket’s bottom edge to the
appropriate 1/2” - 1” (room permitting) above of the high
arc line and centered on the vertical line
, as shown in FIG.
2.3
. spot the wall brackets mounting holes on the header
wall and then refer to your
garage door operator manual for
pre-drilling and securing the
wall bracket to header.
using the
OPERaTOR hOOk-uP ChaRTs, refer to referenced illustrations
in FIG. 2.4 through FIG. 2.5 for correct arm hook-up from
trolley to operator bracket.
NOTE:
Refer to your operator manual for specific details on
how to assembly the curved and straight arm, as shown in
FIG. 2.4 through FIG. 2.5.
NOTE:
Depending on your setup, you may or may not have to
cut straight arm to accomplish trolley settings, as shown in
FIG. 2.4 through FIG. 2.5.
align hole in the appropriate arm with holes in operator
bracket tabs, as shown in FIG. 2.6. Insert 5/16” x 1-1/4”
clevis pin, making sure hole in clevis pin is outside of second
tab of operator bracket. Insert hairpin cotter into clevis pin
hole and spread hairpin cotter to ensure it will secure assem-
bly, as shown in FIG. 2.6 and FIG. 2.7.
�
hORIzONTal
TRaCk
12” OR 15”
FIG. 2.5
sTRaIGhT
aRM
CuRVED
aRM
CuT sTRaIGhT
aRM TO
aCCOMPlIsh
TROllEy
sETTING
FIG. 2.4
CuT sTRaIGhT
aRM TO
aCCOMPlIsh
TROllEy
sETTING
CuRVED
aRM
sTRaIGhT
aRM
OPERATOR hOOk-UP ChART STANDARD lIfT fOR 15” RADIUS
OPERaTOR MODEls
TyPE OF aRM BEING usED
REF. IllusTRaTIONs
aBOVE
Quantum/ClassiC
CurveD / straigHt
fIg. 2.5
linear
straigHt / CurveD
fIg. 2.4
liftmaster
(sears)
CurveD / straigHt
fIg. 2.5
genie
CurveD / straigHt
fIg. 2.5
OPERATOR hOOk-UP ChART STANDARD lIfT fOR 12” RADIUS
OPERaTOR MODEls
TyPE OF aRM BEING usED
REF. IllusTRaTIONs
aBOVE
Quantum/ClassiC
CurveD / straigHt
fIg. 2.5
linear
straigHt / CurveD
fIg. 2.4
liftmaster
(sears)
CurveD / straigHt
fIg. 2.5
genie
CurveD / straigHt
fIg. 2.5
FIG. 2.2
TOP
sECTION
hIGh aRC
lEVEl
FIG. 2.3
FROM
sTEP 11
hIGh aRC
lINE
TyPICal 1/2” - 1” aBOVE hIGh aRC
VERTICal
CENTER lINE
hEaDER
TORquEMasTER
®
COuNTERBalaNCE
FIG. 2.1
FIG. 2.7
5/16” x 1-1/4”
Clevis pin