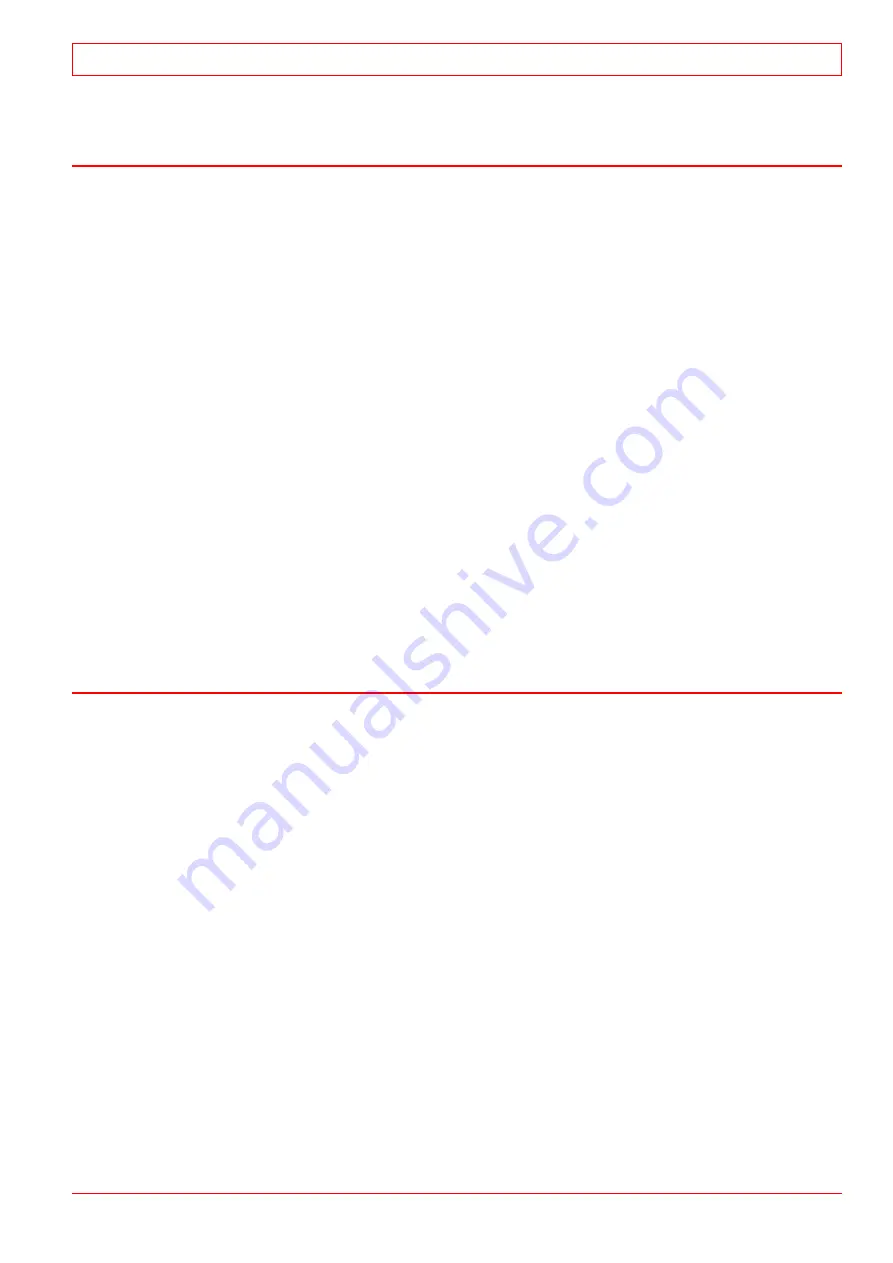
01.3
Reference conditions
Reference conditions according to ISO 3046/I (1995):
Air pressure . . . . . . . . . . . . . . . . . . . . . . . . . . 100 kPa (1.0 bar)
Ambient temperature . . . . . . . . . . . . . . . . . . . . . . 298 K (25°C)
Relative air humidity . . . . . . . . . . . . . . . . . . . . . . . . . . . . . 30 %
Cooling water temperature of charge air cooler . 298 K (25°C)
In case the engine power can be utilized under more difficult
conditions than those mentioned above, it will be stated in the
sales documents. Otherwise, the engine manufacturer can give
advice about the correct output reduction. As a guideline addi-
tional reduction may be calculated as follows:
Reduction factor = (a + b + c) %
a
= 0.5 % for every °C the ambient temperature exceeds the stated
value in the sales documents.
b
= 1 % for every 100 m level difference above stated value in the
sales documents.
c
= 0.4 % for every °C the cooling water of the charge air cooler
exceeds the stated value in the sales documents.
01.4
General engine design
The engine is a turbocharged aftercooled 4-stroke diesel engine
with direct fuel injection.
The engine block
is cast in one piece. The crankshaft is mounted
underslung the engine. The main bearing cap is supported by two
hydraulically tensioned main bearing screws and two horizontal
side screws.
The charge air receiver as well as the cooling water header are
cast into the engine block. The crankcase covers, made of light
metal, seal against the engine block by means of rubber sealing’s.
The lubricating oil sump is welded.
The cylinder liners
are cooled only in the upper part. The
cooling effect is optimized to give the correct temperature of the
inner surface.
To eliminate the risk of bore polishing, the liner is provided with
an anti polishing ring.
The main bearings
are fully interchangeable trimetal or bi-
metal half shell bearings which can be removed by removing the
main bearing cap.
The crankshaft
is forged in one piece and is balanced by coun-
terweights as required.
The connecting rods
are of a three-piece design, so called
“Marine type connecting rod”.
32-200634-01
Main Data, Operating Data and General Design
01
WÄRTSILÄ 32
01 - 3
Содержание VASA 6L32
Страница 4: ......
Страница 18: ...Appendix B Welding Precautions 200640 00 6...
Страница 26: ...01 Main Data Operating Data and General Design 32 200634 01 01 8 W RTSIL 32...
Страница 60: ...Appendix A Environmental Hazards 200507 02A 10...
Страница 68: ...Page 7 7 Document No 4V92A0645 Rev j...
Страница 84: ...03 Start Stop and Operation 32 200402 04 03 12 W RTSIL 32...
Страница 98: ...04 Maintenance Schedule 32 200623 01 04 14 W RTSIL 32...
Страница 154: ...07 Tightening Torques and Use of Hydraulic Tools 32 200643 01 07 30 W RTSIL 32...
Страница 162: ...08 Operating Troubles Emergency Operation 32 200402 01 08 8 W RTSIL 32...
Страница 164: ...Specific Installation Data 2005 01 09 2...
Страница 178: ...10 Engine Block with Bearings Oil Sump and Cylinder Liner 32 200150 10 14 W RTSIL 32 34SG...
Страница 216: ...Appendix A Testing of cylinder tightness 32 200142 A 4 W rtsil 20 32 34...
Страница 226: ...13 Camshaft Driving Gear 32 200546 02 13 10 W RTSIL 32...
Страница 253: ...U tube manometer Fig 15 12 401508200050 32 200549 10 Turbocharging and Air Cooling 15 W RTSIL 32 15 19...
Страница 254: ...15 Turbocharging and Air Cooling 32 200549 10 15 20 W RTSIL 32...
Страница 274: ...16 Injection System 32 200627 01 16 20 W RTSIL 32...
Страница 280: ...Fuel System 32 200508 07 17 6 W RTSIL 32...
Страница 314: ...19 Cooling Water System 32 200050 19 14 W RTSIL 32...
Страница 394: ...23 Instrumentation and Automation 32 200115 II 23 60 W RTSIL 32...