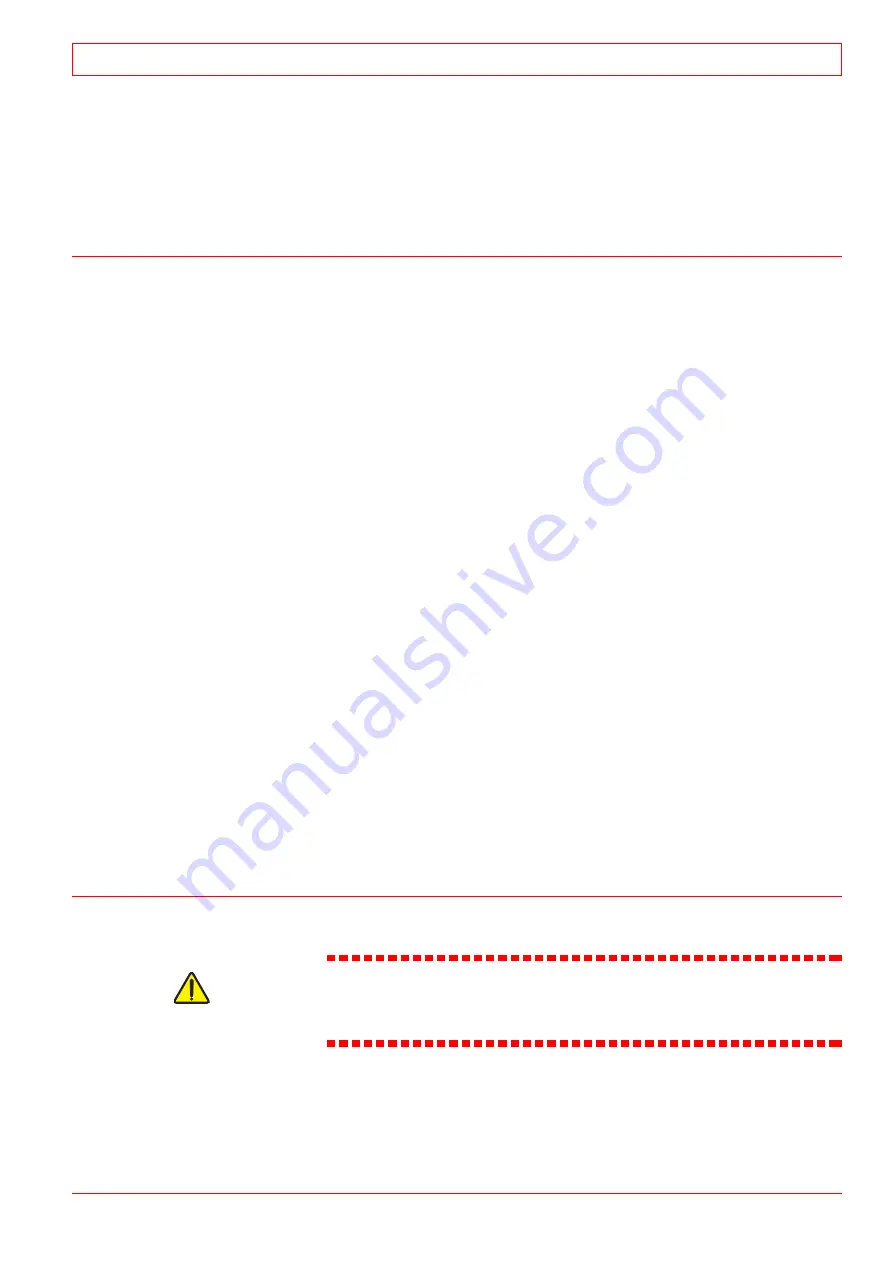
22. Control Mechanism
22.1
Description
During normal operation the engine speed is controlled by a
governor (1) which regulates the injected fuel quantity to corre-
spond with the load and engine speed.
The regulation movement is transferred to the control shaft (10)
through a adjustable link rod (2).
The movement from the control shaft, to the injection pump fuel
racks (15), is transferred through the regulating lever (6) and the
spring (7). The torsion spring (5) enables the control shaft and,
consequently, the other fuel racks to be moved to a stop position,
even if one of the fuel racks has jammed. In the same way the
torsion spring (7) enables the regulating shaft to be moved
towards fuel-on position, even if an injection pump has jammed
in a no-fuel position. This feature can be of importance in an
emergency situation.
The engine can be stopped by means of the stop lever (16). When
the stop lever is moved to stop position, the lever (17) actuates
the lever (9) forcing the regulating shaft to stop position.
The engine is provided with an electro-pneumatic device with
tripping speed about 15 % above the nominal speed. The electro-
pneumatic device moves every fuel rack to a no-fuel position by
means of a pneumatic cylinder on every injection pump. The
cylinder actuates direct on the fuel rack. The electro-pneumatic
device can also be tripped manually, see section 22.5.
When starting, the governor will automatically limit the move-
ment of the regulating shaft to a suitable value.
The speed governor is provided with a stop solenoid which is
connected to the engine automation system.
22.2
Maintenance
Caution!
Special attention should be paid to the function of the system
as a defect in the system may result in a disastrous overspeed-
ing of the engine or in the engine not being able to take load.
32-200636-01
Control Mechanism
22
WÄRTSILÄ 32
22 - 1
Содержание VASA 6L32
Страница 4: ......
Страница 18: ...Appendix B Welding Precautions 200640 00 6...
Страница 26: ...01 Main Data Operating Data and General Design 32 200634 01 01 8 W RTSIL 32...
Страница 60: ...Appendix A Environmental Hazards 200507 02A 10...
Страница 68: ...Page 7 7 Document No 4V92A0645 Rev j...
Страница 84: ...03 Start Stop and Operation 32 200402 04 03 12 W RTSIL 32...
Страница 98: ...04 Maintenance Schedule 32 200623 01 04 14 W RTSIL 32...
Страница 154: ...07 Tightening Torques and Use of Hydraulic Tools 32 200643 01 07 30 W RTSIL 32...
Страница 162: ...08 Operating Troubles Emergency Operation 32 200402 01 08 8 W RTSIL 32...
Страница 164: ...Specific Installation Data 2005 01 09 2...
Страница 178: ...10 Engine Block with Bearings Oil Sump and Cylinder Liner 32 200150 10 14 W RTSIL 32 34SG...
Страница 216: ...Appendix A Testing of cylinder tightness 32 200142 A 4 W rtsil 20 32 34...
Страница 226: ...13 Camshaft Driving Gear 32 200546 02 13 10 W RTSIL 32...
Страница 253: ...U tube manometer Fig 15 12 401508200050 32 200549 10 Turbocharging and Air Cooling 15 W RTSIL 32 15 19...
Страница 254: ...15 Turbocharging and Air Cooling 32 200549 10 15 20 W RTSIL 32...
Страница 274: ...16 Injection System 32 200627 01 16 20 W RTSIL 32...
Страница 280: ...Fuel System 32 200508 07 17 6 W RTSIL 32...
Страница 314: ...19 Cooling Water System 32 200050 19 14 W RTSIL 32...
Страница 394: ...23 Instrumentation and Automation 32 200115 II 23 60 W RTSIL 32...