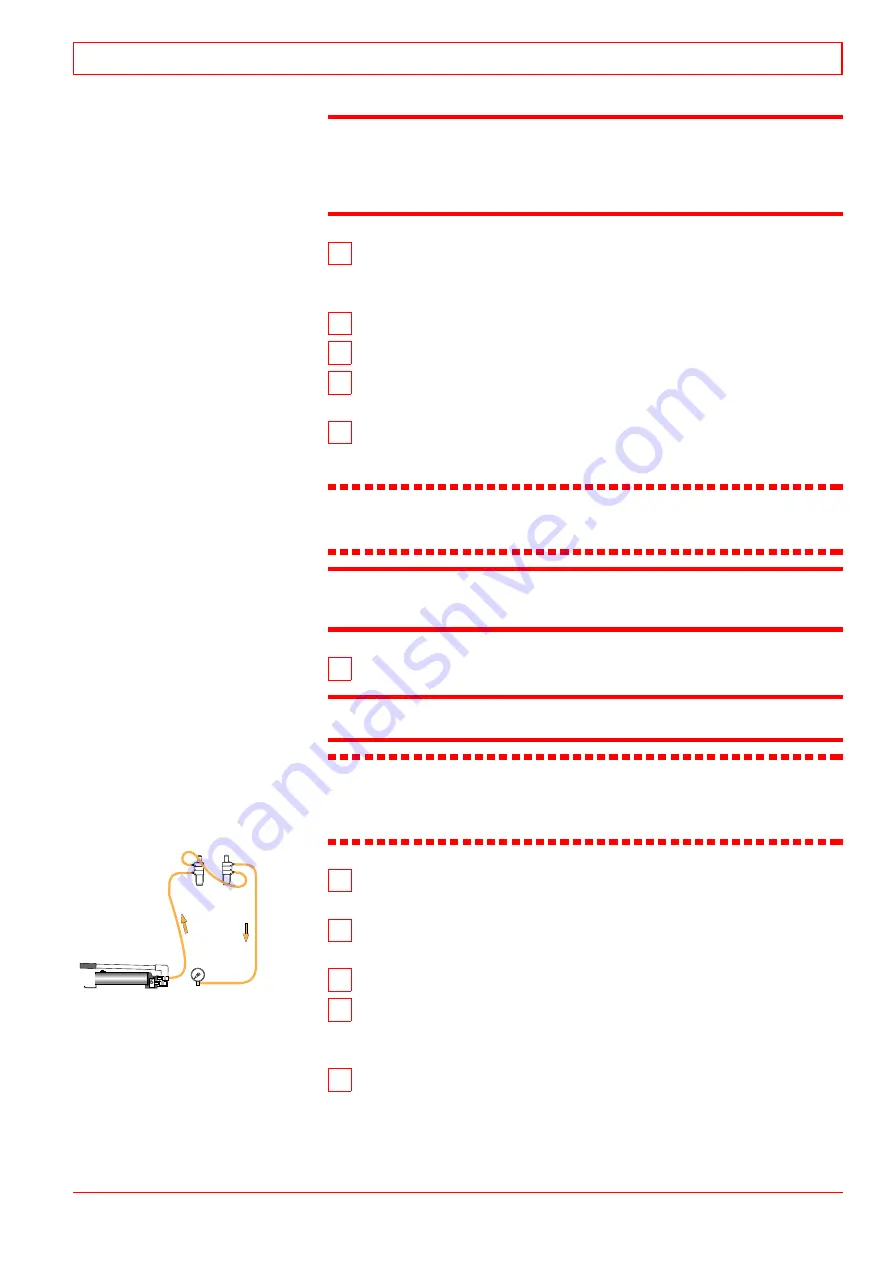
Caution!
The screws will be overloaded if the maximum hydraulic
pressure is exceeded.
It is recommended to change the screws if maximum hydrau-
lic pressure is exceeded for some reason.
6 Release the pressure slowly
and disconnect the hoses,
unscrew the tightening nuts and remove hydraulic tool as one
package.
7 Remove the nuts.
8 Rotate the crank pin
of the cylinder concerned in to TDC.
9 Mount the limiter
800018 in the lower part of cylinder
liner and tighten the screw, see Fig 11-5.
10 Separate upper part
and big end (5) by turning the
crankshaft towards BDC.
Support the upper part of the connecting rod to avoid dam-
aging the cylinder liner.
Note!
To avoid damaging the guiding pins the separation of the
upper part (1) and the big end (5) should be done aligned.
11 Remove the shim (2),
see Fig 11-2.
Note!
Do not mix the shims (2) with other connecting rod shims.
Always when mounting flute or/and the limiter is/are mounted
in the crankcase observe extremely cautiousness when using
the turning device.
12 Rotate the crankshaft
towards the operating side to the
position 55° from TDC by using the turning device.
13 Mount the mounting support 800102
on the upper stud
of the crank case cover, see Fig 11-5. Tighten the nut.
14 Lift the hydraulic tools
800020 in to the position.
15 Connect the hoses
of the hydraulic pump 800053 and
proceed to open the upper connection as described in adjacent
figure.
16 Strain the screws by raising the pressure
to the value
stated in the section 07.3 and proceed with opening the nuts.
Hydraulic oil
DISMANTLING
1. Lift the distance sleeve.
2. Lift the hydraulic cylinder and
screws in a one package in pos.
3. Connect hoses, open valve.
4. Tighten the tool assembly,
until the piston and cylinder is
on the same level, open the
nuts by 180˚.
5. Close the valve, pump to
required pressure.
Open the nuts about half a turn.
6. Open the valve slowly and
remove the tool.
32-200020
Crank Mechanism: Crankshaft, Connecting Rod, Piston
11
WÄRTSILÄ 32
11 - 7
Содержание VASA 6L32
Страница 4: ......
Страница 18: ...Appendix B Welding Precautions 200640 00 6...
Страница 26: ...01 Main Data Operating Data and General Design 32 200634 01 01 8 W RTSIL 32...
Страница 60: ...Appendix A Environmental Hazards 200507 02A 10...
Страница 68: ...Page 7 7 Document No 4V92A0645 Rev j...
Страница 84: ...03 Start Stop and Operation 32 200402 04 03 12 W RTSIL 32...
Страница 98: ...04 Maintenance Schedule 32 200623 01 04 14 W RTSIL 32...
Страница 154: ...07 Tightening Torques and Use of Hydraulic Tools 32 200643 01 07 30 W RTSIL 32...
Страница 162: ...08 Operating Troubles Emergency Operation 32 200402 01 08 8 W RTSIL 32...
Страница 164: ...Specific Installation Data 2005 01 09 2...
Страница 178: ...10 Engine Block with Bearings Oil Sump and Cylinder Liner 32 200150 10 14 W RTSIL 32 34SG...
Страница 216: ...Appendix A Testing of cylinder tightness 32 200142 A 4 W rtsil 20 32 34...
Страница 226: ...13 Camshaft Driving Gear 32 200546 02 13 10 W RTSIL 32...
Страница 253: ...U tube manometer Fig 15 12 401508200050 32 200549 10 Turbocharging and Air Cooling 15 W RTSIL 32 15 19...
Страница 254: ...15 Turbocharging and Air Cooling 32 200549 10 15 20 W RTSIL 32...
Страница 274: ...16 Injection System 32 200627 01 16 20 W RTSIL 32...
Страница 280: ...Fuel System 32 200508 07 17 6 W RTSIL 32...
Страница 314: ...19 Cooling Water System 32 200050 19 14 W RTSIL 32...
Страница 394: ...23 Instrumentation and Automation 32 200115 II 23 60 W RTSIL 32...