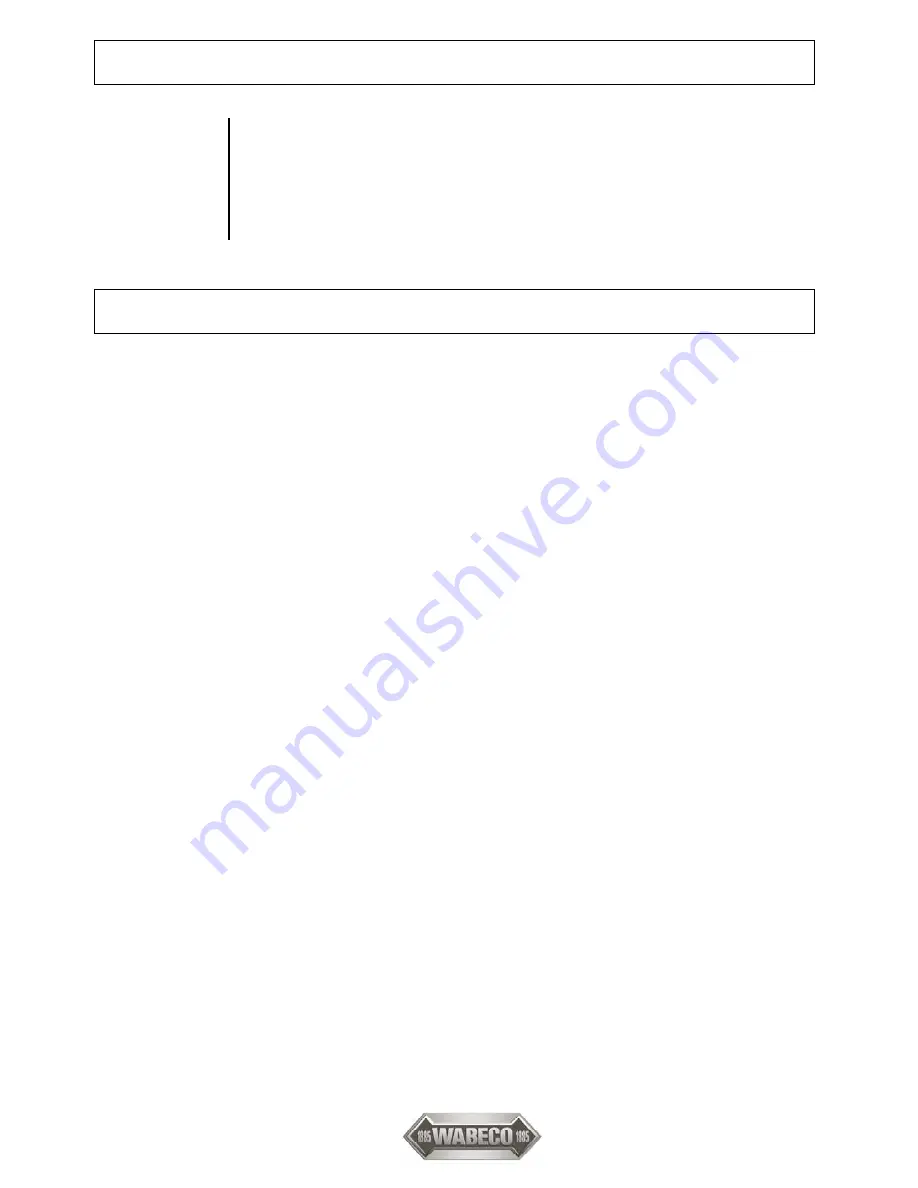
8
4.
Overload protection
i
Wait approx. 1 second after switching off the machine manually or after an
automatic switchdown following an overload before switching it on again. This will
ensure that the motor is protected effectively in all work situations. Otherwise the
machine may not run up again because the electronics relay could did not have
enough time to react.
5. Safety
Instructions
1. The feed line for the motor must be connected to a sealed contact socket or junction box.
(Have the socket or junction box checked by an electrician beforehand; protection against
children being able to put into operation).
2. The socket or junction box must be close enough to the equipment, so that the live cable is
subjected to no tensile strain whatsoever.
3. When maintenance or cleaning work is done, the machine must be shutdown and the mains
plug pulled out.
4.
Do not slow down workpieces or chucks by hand or any other objects.
5.
Wear safety goggles when working with the machine.
6. Do not remove the chips with the hand. Use corresponding aids (hand brush, hook, paint
brush).
7.
Always keep the protective hood of the drive closed.
8.
The turning tools must be tightly clamped at the correct height and as short as possible.
9.
The turning tools must never be replaced when the machine is running.
10.
Never leave the clamping chuck key in (even when not in operation).
11. Always pay attention to the clamping width of the lathe chuck. (lathe chucks
∅
max. 40mm,
drill chucks max. 100mm
∅
).
12.
Never take measurements on work pieces during the lathing process
(risk of accidents
and damage to the measuring gauges)
13. Do not wear loose clothing (ties, shirt sleeves, jewellery etc.).
14. When working between centres, always centre well in order to prevent the workpiece from
being slung away. In addition, make sure that the locking screw of the tailstock is tightened.
15. When using the automatic feed always take care that the cross support does not get in contact
with the chuck or the tailstock.
16. Never leave the machine alone when in operation.
17.
When machining wood, use the lathe centre instead of the lathe chuck to support the
work piece.
18. The machine must be secured so that it cannot be switched on by children. Make sure that
other people do not operate the machine.
19. Always keep the machine dry.
20. Frequently check the machine for damage. Any damaged parts must be replaced by original
parts and are to be fitted by an expert or by us.
Содержание D2400
Страница 5: ...5 1 Machine dimensions 1 1 D2000 1 2 D2400...
Страница 6: ...6 1 Machine dimensions 1 3 D3000...
Страница 28: ...28 13 Drawings and list of parts 13 3 Lead screw drive for D2400 and D3000...
Страница 32: ...32 13 Drawings and list of parts 13 5 Drive with gear transmission for D2000...
Страница 34: ...34 13 Drawings and list of parts 13 6 Cross support...