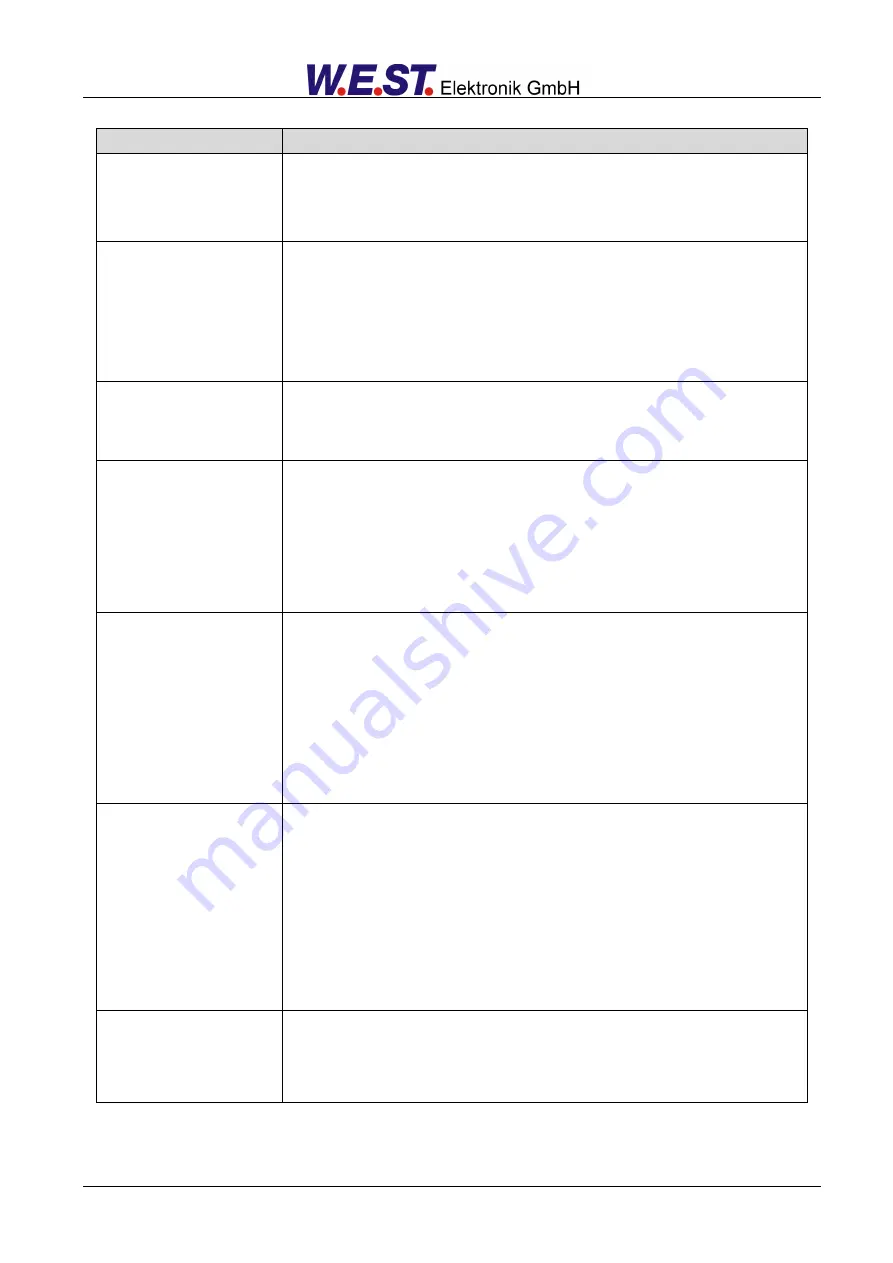
Page 37 of 53
POS-123-P-PFN
FAULT
CAUSE / SOLUTION
ENABLE is active, the
module does not re-
spond, and the READY
LED is off.
There is presumably no power supply or one of the ENABLE signals is not present. If
there is no power supply, there is also no communication via our operating program.
If a connection to WPC-300 has been made, then a power supply is also available.
The same is applied to the Profinet connection. In this case in monitor window the
ENABLE input can be checked.
ENABLE is active, the
READY LED is flashing.
The flashing READY LED signals that a fault has been detected by the module. The
fault could be:
•
A broken cable or bad signal at the sensor input if
4… 20 mA signal are used.
•
A broken cable or incorrect cabling to the solenoids.
•
Internal data error: press the command/SAVE button to delete the data error. The
system reloads the DEFAULT data.
•
The field bus communication is faulty.
ENABLE is active; the
READY LED is on, the
system moves to an end
position.
The control circuit polarity is incorrect. The polarity can be changed with the
SIGNAL:U command or maybe by reversing the sensor signal (SIGNAL:X).
ENABLE is active, the
READY LED is on, the
STATUS LED is not on,
the system moves to the
target position but
doesn’t reach it
(positioning error).
Serious positioning errors can result from incorrect parameterisation or incorrect
system design.
•
Are working range and nominal sensor range correct?
•
Is the gain high enough (to start the system the deceleration distances should be
set to approx. 20… 25 % of the cylinder position and decreased if necessary
)
?
•
Is there an overlapping of the valve to be compensated? Values should be
mentioned in the datasheet of the valve.
ENABLE is active, the
READY LED is on, and
the system oscillates on
the target.
The system is working and also actuating the valve.
Various potential problems could be:
•
The parameterisation is not yet adjusted to the system (gain too high).
•
There is severe interference on the power supply.
•
Very long sensor cables (> 40 m) and sensor signal interference.
•
The MIN setting to compensate the valve overlap is too high.
As a basic principle, the parameterisation of the sensor data and the controller
settings must be carried out first (before switching on). An incorrect demand is
equivalent to incorrect system design which then leads to incorrect operation. be
reduced.
Speed too low
The drive may be able to move to position but the speed is too low.
•
Check the controller signal to the valve whether C reaches 100%. If not
parameterisation (e.g. gain) should be adapted.
•
Check If the control signal U reaches 100%. If not maybe there is a speed
limitation.
•
Check the solenoid current. If the needed value is not reached, the valve
adaption may has to be adapted (CURRENT/MAX)
•
In case of all values are correct, measure the solenoid current. If the setpoint is
not reached, the wiring including the valve plugs should be checked.
•
In the case of all is correct, the cause is a hydraulic problem, for example a
wrong dimension of a used component.
Speed too high
The drive moves in and out too fast leading to uncontrolled behavior. Reducing the
speed demand has very little or no effect.
-
The hydraulic system is over-sized. The entire parameterisation of the
movement cycle cannot be reproduced (overlap and deceleration distance
settings)
Содержание POS-123-P-PFN
Страница 11: ...Page 11 of 53 POS 123 P PFN 31 03 2021...
Страница 53: ...Page 53 of 53 POS 123 P PFN 31 03 2021 9 Notes...