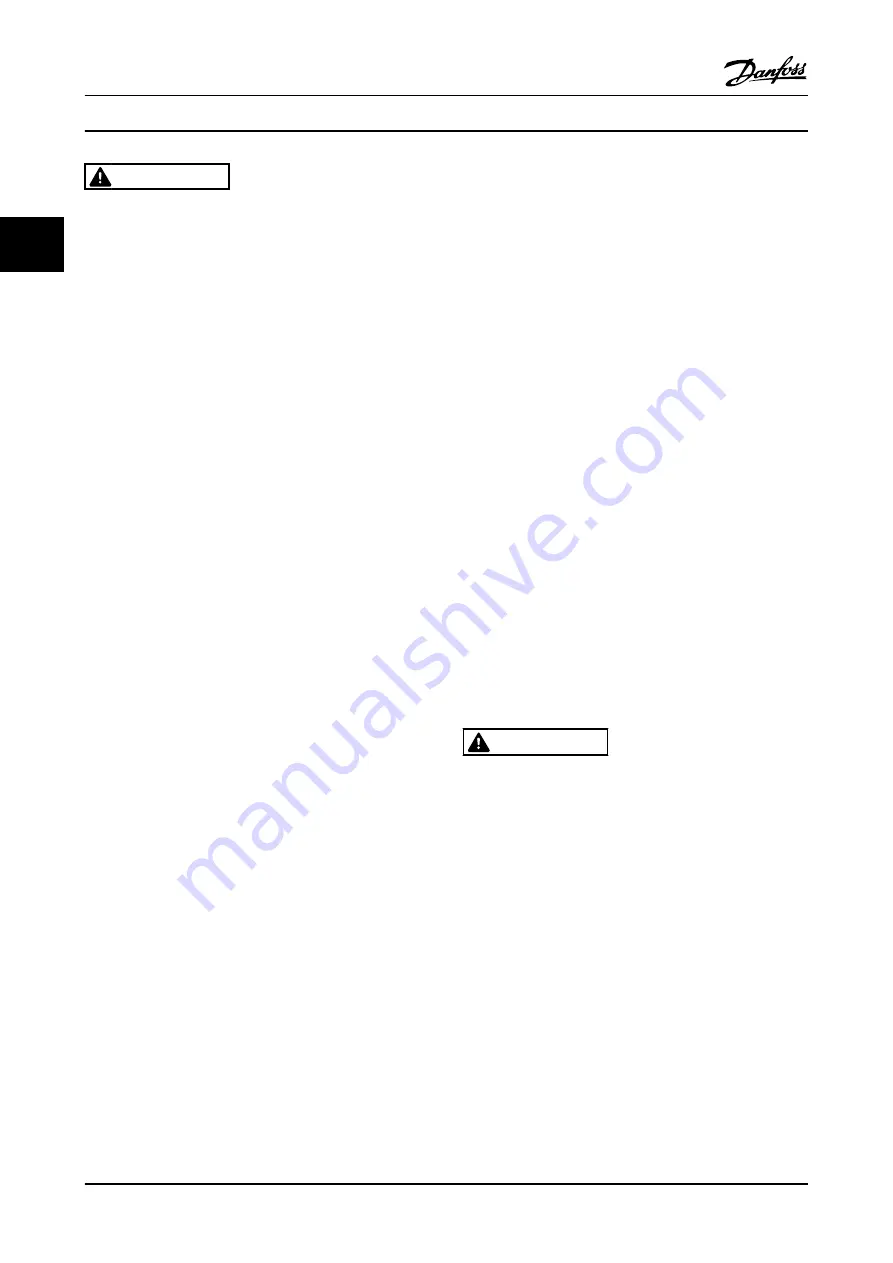
WARNING
Automatic Restart Behavior is permitted in one of the two
situations:
1.
Unintended restart prevention is implemented by
other parts of the safe stop installation.
2.
A presence in the hazard zone can be physically
excluded when safe stop is not activated. In
particular, paragraph 5.3.2.5 of ISO 12100-2 2003
must be observed
2.5.2 Safe Stop Commissioning Test
After installation and before first operation, perform a
commissioning test of an installation or application, using
Safe Stop.
Perform the test again after each modification of the
installation or application involving the Safe Stop.
NOTE!
A passed commissioning test is mandatory after first instal-
lation and after each change to the safety installation.
The commissioning test (select one of cases 1 or 2 as
applicable):
Case 1: Restart prevention for Safe Stop is required (that is
Safe Stop only where
5-19 Terminal 37 Safe Stop
is set to
default value [1], or combined Safe Stop and MCB 112
where
5-19 Terminal 37 Safe Stop
is set to
[6] PTC 1 & Relay
A
or
[9] PTC 1 & Relay W/A
):
1.1 Remove the 24 V DC voltage supply to
terminal 37 using the interrupt device while the
adjustable frequency drive drives the motor (that
is line power supply is not interrupted). The test
step is passed when
•
the motor reacts with a coast, and
•
the mechanical brake is activated (if
connected)
•
the alarm “Safe Stop [A68]” is displayed
in the LCP, if mounted
1.2 Send Reset signal (via bus, digital I/O, or
[Reset] key). The test step is passed if the motor
remains in the safe stop state, and the
mechanical brake (if connected) remains
activated.
1.3 Reapply 24 V DC to terminal 37. The test step
is passed if the motor remains in the coasted
state, and the mechanical brake (if connected)
remains activated.
1.4 Send Reset signal (via bus, digital I/O, or
[Reset] key). The test step is passed when the
motor becomes operational again.
The commissioning test is passed if all four test steps 1.1,
1.2, 1.3 and 1.4 are passed.
Case 2: Automatic Restart of Safe Stop is wanted and
allowed (that is, Safe Stop only where
5-19 Terminal 37
Safe Stop
is set to [3], or combined Safe Stop and MCB
112 where
5-19 Terminal 37 Safe Stop
is set to
[7] PTC 1 &
Relay W
or
[8] PTC 1 & Relay A/W
):
2.1 Remove the 24 V DC voltage supply to
terminal 37 by the interrupt device while the
adjustable frequency drive drives the motor (that
is line power supply is not interrupted). The test
step is passed when
•
the motor reacts with a coast, and
•
the mechanical brake is activated (if
connected)
•
the alarm “Safe Stop [A68]” is displayed
in the LCP, if mounted
2.2 Reapply 24 V DC to terminal 37.
The test step is passed if the motor becomes operational
again. The commissioning test is passed if both test steps
2.1 and 2.2 are passed.
NOTE!
See warning on the restart behavior in
WARNING
The Safe Stop function can be used for asynchronous,
synchronous and permanent magnet motors. Two faults
can occur in the power semiconductor of the adjustable
frequency drive. When using synchronous or permanent
magnet motors a residual rotation can result from the
faults. The rotation can be calculated to Angle = 360/
(Number of Poles). The application using synchronous or
permanent magnet motors must take this residual rotation
into consideration and ensure that it does not pose a
safety risk. This situation is not relevant for asynchronous
motors.
Installation
VLT
®
AutomationDrive Instruction
Manual
2-16
MG33AM22 - VLT
®
is a registered Danfoss trademark
2
2
Содержание FC 300
Страница 1: ...MAKING MODERN LIVING POSSIBLE Instruction Manual VLT AutomationDrive FC 300 0 25 75 kW ...
Страница 2: ......
Страница 8: ...Contents VLT AutomationDrive Instruction Manual MG33AM22 VLT is a registered Danfoss trademark ...
Страница 14: ...Introduction VLT AutomationDrive Instruction Manual 1 6 MG33AM22 VLT is a registered Danfoss trademark 1 1 ...
Страница 62: ...Status Messages VLT AutomationDrive Instruction Manual 7 4 MG33AM22 VLT is a registered Danfoss trademark 7 7 ...
Страница 109: ...Index VLT AutomationDrive Instruction Manual MG33AM22 VLT is a registered Danfoss trademark 12 5 ...
Страница 110: ...www danfoss com drives MG33AM22 130R0300 MG33AM22 Rev 2013 03 12 ...