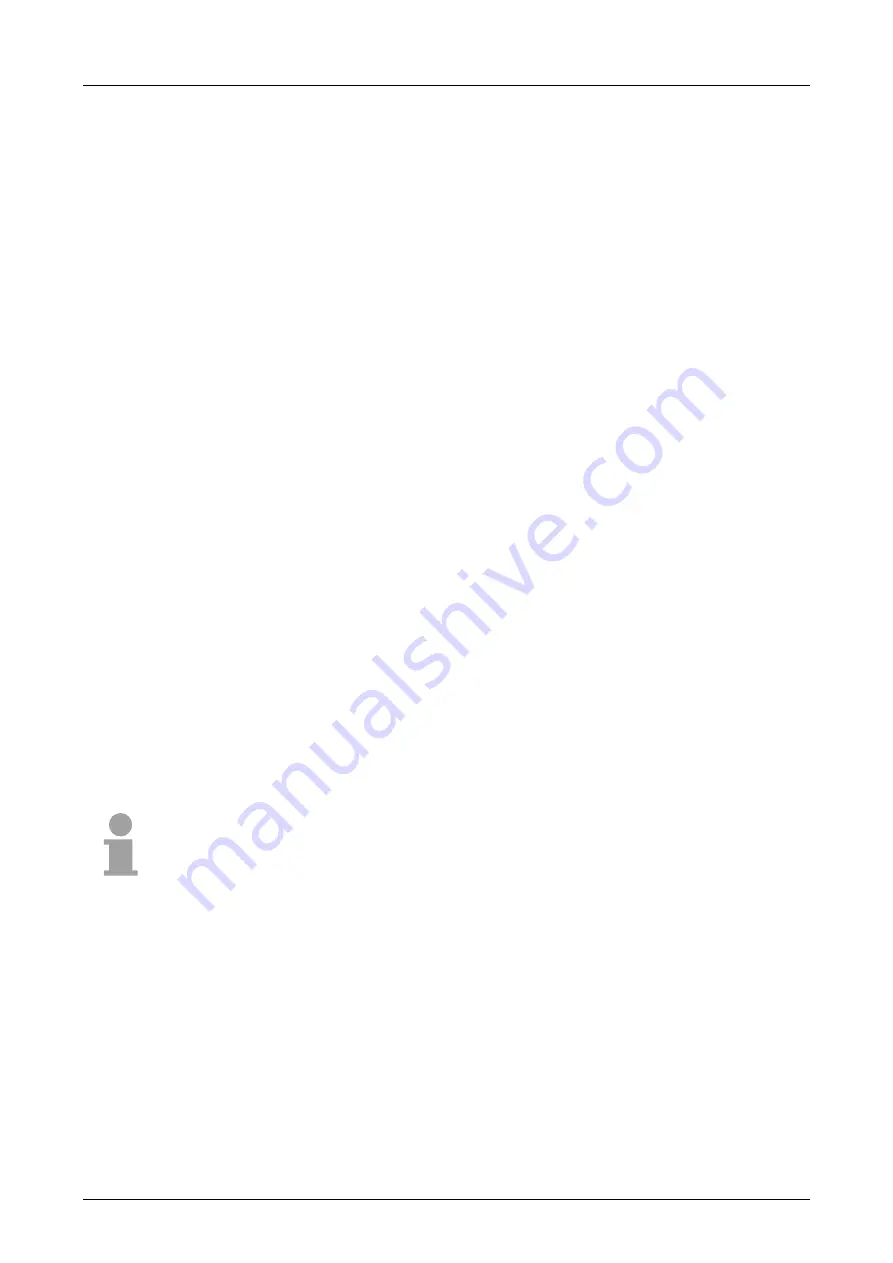
Manual VIPA System 200V
Chapter 4 CP 240 - serial
HB97E - CP - Rev. 11/30
4-27
The CP 240 Modbus supports several operating modes that are described
in the following:
In
Modbus Master
operation you control the communication via your PLC
user application. For this the SEND and RECEIVE handling blocks are
required. By using a blockage you here have the option to transfer up to
250Byte user data.
In
Modbus Slave Short
operation the CP 240 occupies each 16Byte for in-
and output data at arbitrary area in the CPU. Via the address parameter
you may define this area during the hardware configuration. A PLC
program for the data provision is at the slave side not required. This
operation mode is especially convenient for the fast transfer of small data
amounts via Modbus.
For data that exceeds the length of 16Byte you should use the operation
mode Modbus Slave Long. Here the master transfers at data reception via
RECEIVE the area to the CPU where a change has happened. The date
transfer happens following this principle:
The reception area of max. 1024Byte is separated into 128 8Byte blocks.
At data change by the master only those blocks are transferred to the CPU
where changes occurred. During one block cycle of the RECEIVE block up
to 16 coherent 8Byte block may be handled on at the back plane bus. If the
8Byte blocks are not coherent, every changes 8Byte block requires one
block cycle. The receive DB of the RECEIVE block must always be set as a
multiple of 8.
By means of a SEND call a wanted data area is transferred to the CP that
may be read by the master. Writing master accesses must not lie outside
of the reception area!
Please regard that Modbus Slave Long is supported starting with the block
library FX000002_V120 or higher.
Note!
The CP 240 only reports a respond telegram to the master after all data
has been received.
After switching on the voltage supply the LEDs ER, TxD and RxD are
flashing at the Modbus module. Thus the module signalizes that it hasn’t
received valid parameters from the CPU yet. As soon as you switch the
CPU to RUN, the Modbus parameters are transferred to the module. With
valid parameters the LEDs ER, TxD and RxD extinguish. Now the Modbus
module is ready for communication.
At deployment in master mode you may now execute according write/read
commands in your user application.
If the ER-LED is not extinguishing, an internal error has happened. At a
transient error you may set this back by means of a STOP-RUN switch of
the CPU.
Modbus at the
CP 240 from VIPA
Modbus Master
Modbus Slave Short
Modbus Slave Long
Commissioning
Содержание CP 240 RS232
Страница 1: ...Manual VIPA System 200V CP Order No VIPA HB97E_CP Rev 11 30...
Страница 2: ...L...
Страница 14: ...Chapter 1 Basics Manual VIPA System 200V 1 6 HB97E CP Rev 11 30...
Страница 126: ...Chapter 5 CP 240 EnOcean Manual VIPA System 200V 5 32 HB97E CP Rev 11 30...
Страница 144: ...Chapter 6 CP 240 M Bus Manual VIPA System 200V 6 18 HB97E CP Rev 11 30...
Страница 148: ...Index Manual VIPA System 200V A 4 HB97E CP Rev 11 30 M Stich...