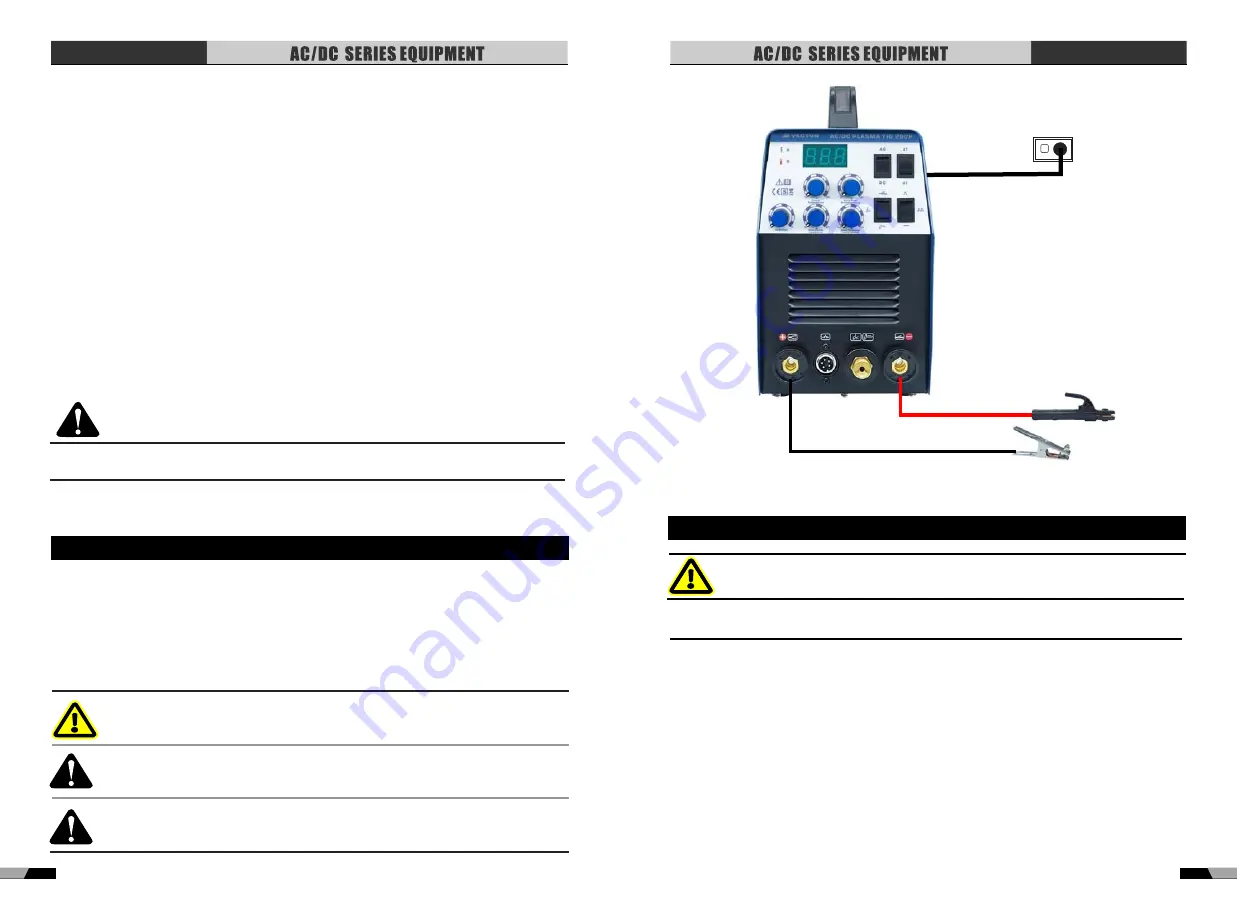
14. 5 Pin Control Socket
The 5 pin receptacle is used to connect a trigger switch or remote control to the welding
Power Source circuitry:
To make connections, align keyway, insert plug, and rotate threaded collar fully clockwise.
1 .
5
Gas/electricity integrated interface
Connect Gas/electricityone-piece TIG torch gun and plasma torch
.
and turned securely to achieve a sound electrical connection.
16. Negative Welding Terminal
Negative Welding Terminal. Welding current flows from the Power Source via heavy
duty bayonet type terminals. It is essential, however, that the male plug is inserted
17. Power switch
before using the machine. Pull the switch to the closure state of “AN” to operate the
machine, and pull the switch to “AUS” after use. Turn off the power input, and the machine
will stop operating.
18. Gas input port
The gas port is connected with the gas valve output port. After connection, check whether
there is gas leakage.
CAUTION
Loose welding terminal connections can cause overheating and result in the male plug
being fused in the terminal.
3.2 Setup for STICK (MMA) welding
WARNING
Before connecting the work clamp to the work and
inserting the electrode in the electrode holder make
sure the mains power supply is switched off.
CAUTION
CAUTION
Remove any packaging material prior to use. Do not
block the air vents at the front or rear of the Welding
Power Source.
Loose welding terminal connections can cause
overheating and result in the male plug being fused
in the bayonet terminal.
For Alkaline Electrode,connect the electrode holder to the positive welding termimal
Electrode,please connect the electrode holder to the negative welding termimal and
manufacturer. Welding current flows from the Power Source via heavy duty bayonet type
terminals. It is essential, however, that the male plug is inserted and turned securely to
achieve a sound electrical connection. Select STICK mode with the process selection
control.
a n d c o n n e c t t h e w o r k l e a d t o t h e n e g a t i v e w e l d i n g t e r m i n a l , w h i l e f o r t h e A c i d
connect the work lead to the positve welding terminal.If in doubt consult the electrode
power supply
Electrode Holder
Earth Clamp
3.3 Set-up for HF TIG (GTAW) welding
WARNING
Before any welding is to begin, be sure to wear all
appropriate and recommended safety equipment.
6. The tungsten must be ground to a blunt point (similar to a pencil) in order to achieve optimum
welding results. See illustration. It is critical to grind the tungsten electrode in the direction the
grinding wheel is turning. Grind at a 30 degree angle and never to a sharp point.
5. Connect the work lead clamp to your work piece.
4. Slowly open the Argon Cylinder Valve to the fully open position.
3. Connect the gas line/hose to the proper shielding gas source.
2. Connect the work lead cable to the positive output terminal, and the HF TIG Torch cable
to the negative output terminal.
The following set up is known as Straight Polarity or DC electrode positive. This is commonly
used for DC HF TIG welding on most materials such as steel and stainless steel.
NOTE
1. Switch the ON/OFF Switch (located on the rear panel) to OFF.
7. Install the tungsten with approximately 1.6mm to 3.2mm sticking out from the gas cup,
ensuring you have correct sized collet.
Operation
Operation
48
49