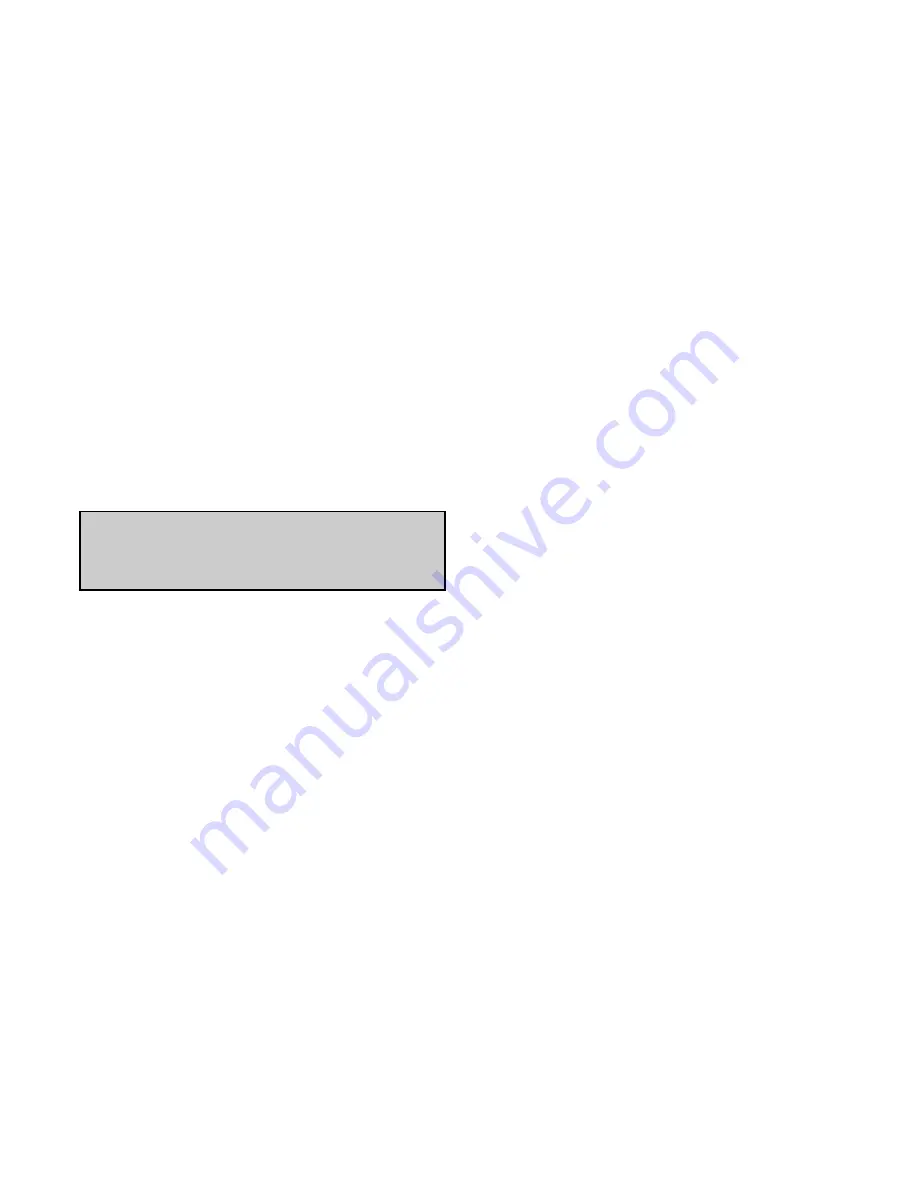
14
requires an immediate change of the exhaust filter.
In order to replace the filter, remove the four
socket head cap screws (Ref. 155, 146) retaining the
exhaust port housing. Pull the housing off the
exhaust box and set it aside. Use a slotted head
screw driver to loosen the exhaust filter retaining
spring, then rotate and remove the spring. Pull the
filter cartridge (Ref. 120) out of the exhaust box.
To field test an exhaust filter element, remove it
from the pump, allow it to cool, clean the sealing
end (or O-ring end), and use compressed air to blow
through the element. Apply approximately 3 to 6
psi, which is the maximum allowable operating
pressure across the filter.
Note: Use a shop rag to
seal off the connection between the air hose and the
filter.
If you can blow through it, the element is
good. If not, discard it and install a new one. The
filter cannot be cleaned successfully. Visually
inspect the filter element for cracks.
Reinstall the filter elements. Make sure the open
end of the element is properly seated down in its
recess in the exhaust box (see Figure 3) with the O-
ring (Ref. 121) correctly positioned. Retain the filter
with the spring clip, tighten the tension screw until
the filter is secure. Place the exhaust port gasket and
housing in position on the exhaust box and retain
with the cap screws.
3.4 Vacuum Inlet Filter
If the pump is equipped with a special vacuum
inlet filter in applications where powder, dust or grit
is present, the filter cartridge should be cleaned on a
weekly basis, or as required, depending on the
amount of foreign particles to which the pump is
exposed.
3.5 Maintenance Chart
Daily:
Visually check oil level (see 3.1.1 and
3.1.2).
Weekly:
Check oil for contamination (see
3.1.3). Inspect inlet filter (see Section 3.4).
Every three (3) or four (4) months, 500 to 750
hours of operation, or as necessary:
See 3.1.3 and
1.5. Drain and discard oil from the hot pump.
Replace the automotive-type oil filter and refill with
fresh oil through the fill plug (see 3.1.2 through
3.1.3 and 3.2).
Every nine (9) to twelve (12) months, or as
necessary:
Replace exhaust filter elements (see
3.3).
3.6 Overhaul Kit/Filter
An overhaul kit containing a set of gaskets and
O-rings, vanes, bearings and bearing sleeves, shaft
seals and taper pins, is available from the factory.
Also, a filter kit containing oil drain plug, gas-
kets, automotive type oil filter (where applicable),
exhaust filter, and exhaust filter, is available from
the factory.
When ordering, please specify pump size and
model (a 3-digit suffix after size), and serial number.
4.0 TROUBLESHOOTING
4.1 Trouble
Pump does not reach “blank-off” pressure which
is the lowest absolute pressure (best vacuum) when
running with the inlet closed via a blank flange or a
valve; or the pump takes too long to evacuate the
system. “Blank-off” pressure can be measured by
using a good quality capsule gauge.
4.1.1 Possible Cause
Contaminated oil is by far the most common
cause of not reaching the ultimate pressure.
Remedy:
Shut off pump, after operating temperature has
been reached, drain the warm oil from pump and
exchange automotive-type oil filter (where applica-
ble), if necessary. Flush and fill pump with new oil
and take new “blank-off” measurement after operat-
WARNING: Do not inhale through the filter
or allow your mouth to come in direct contact
with the filter.
Содержание Ultravac 500
Страница 2: ......
Страница 69: ...9 ...
Страница 70: ...10 ...
Страница 72: ...12 13 ...
Страница 80: ...21 Maximum oil temperature with 80 F ambient temperature and no supplemental oil cooling ...
Страница 81: ...22 ...