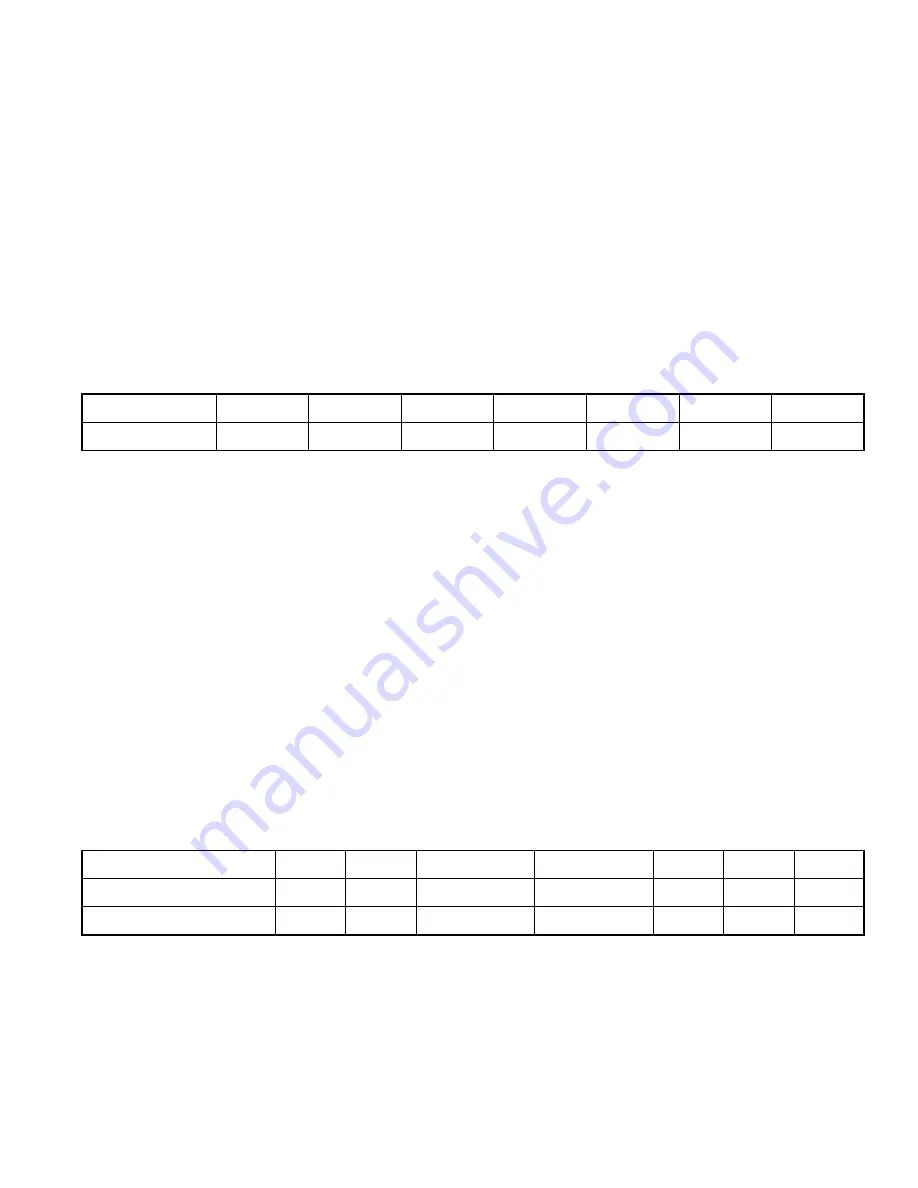
9
PURGES
COOLING PURGE — Cooling Purge is to cool the inside of the casing and the screws. During the operation of the pump, the
process gas introduced into the casing through the suction nozzle is compressed by the rotation of the screws and transferred to
the discharge side. Temperature of the process gas gets increased by the heat of compression and this heat energy should be
removed in order to prevent the pump from seizure. This Cooling Purge is required for SDV-800, SDV-1500, and SDV-2700. It is
optional for the smaller models, SDV-120, SDV-200, SDV-320 and SDV-430.
Normally this purge is done by atmospheric air. Where the process gas is not compatible with the atmospheric air, a different
cooling medium should be used, such as, Nitrogen, CDA (Clean Dry AIr) etc. For a standard pump, an air filter is provided near the
discharge side of the casing.
NOTES:
•
Cooling Purge is not required for SDV-120, SDV-200 & SDV-320 for typical processes.
•
Flow rates shown below should be applied when the end-user decides to supply Cooling Purge to the pump.
•
Purge Pressure: Atmospheric pressure for process inlet pressure (operating pressure) 150 torr or below 0.5 kg/cm2g
(7.11 psig) minimum for process inlet pressure (operating pressure) 150 torr or higher.
•
Flow Rates: slpm (sgpm) Cooling purge flow rate can vary depending on the process inlet pressure (operating
pressure)
SDV-120
SDV-200
SDV-320
SDV-430
SDV-800
SDV-1500
SDV-2700
Cooling Purge
30 (7.9)
36 (9.5)
40 (10.6)
40 (10.6)
50 (13.2)
160 (42.3)
170 (43.9)
SEAL PURGE — Depending on the application, SDV pump may require Seal Purges. If Seal Purge is specified on your system, it
is intended to provide a pressurized barrier within the Front End Plate (FEP) and/or Rear End Plate (REP) with gas which should be
compatible with the process gas and the lubrication oil/grease or inert gas such as Nitrogen or Argon, so that the contamination of
the lubrication oil and/or the grease within the Front End Cover (FEC) and/or the Rear End Plate (REP) is prevented.
Drive End (DE) Seal Purge should be connected to two purge connection nozzles on the Front End Cover. Non Drive End (NDE)
Seal Purge should be connected to two purge connection nozzles on the Rear End Plate (REP). (For SDV-120, there’s only one Non
Drive End (NDE) Seal Purge connection nozzle.) Both Drive End (DE) and Non Drive End (NDE) Seal Purges can be manifolded
from a single source of purge gas supply.
Seal Purge pressure should be below 0.5 kg/cm2g (7.11 psig). Leak rate of the mechanical seals is below 3 cc/hr (5.3 x 10-6 CFM)
and they can sustain pressure up to 3 kg/cm2g (42.7 psig).
Please note that TVBS does not recommend NDE (Non Drive End) Seal Purge unless it is absolutely required. Providing NDE (Non
Drive End) Seal Purge slightly increases the inlet pressure due to the additional mass flow into the pump. Please consult factory for
further assistance if you require seal purges.
NOTES:
•
Start/Stop (Cleaning) Purges should last for 20 to 30 minutes with the process isolation valve closed, prior to the start
of the process operation and immediately after the completion of the process operation.
•
Seal Purge Pressure: 0.5 kg/cm2g (7.11 psig) Maximum
•
Flow Rates: slpm (sgpm)
SDV-120
SDV-200
SDV-320
SDV-430
SDV-800
SDV-1500
SDV-2700
DE (Drive End) Seal Purge
3.3 (0.9)
3.3 (0.9)
5.8 - 6.7 (1.5 - 1.8)
5.8 - 6.7 (1.5 - 1.8)
8.3 (2.2)
11.7 (3.1)
11.7 (3.1)
NDE (Non Drive End) Seal Purge
0.5 (0.13)
0.8 (0.21)
1.6 (0.42)
2.0 (0.53)
3.7 (0.98)
7.5 (1.98)
13 (3.43)
START/STOP (CLEANING) PURGES — Start/Stop (Cleaning) Purge is to remove residual process gas or any incompatible
substances such as moisture, atmospheric air etc. from the inside of the pump prior to or after the pump operations. Start/Stop
(Cleaning) Purge should be done with gas which is compatible with the process gas or inert gas such as Nitrogen or Argon. This
Start/Stop (Cleaning) Purge is especially important when pumping corrosive gases, toxic gases or polymeric process materials
such as film resin etc.
Start (Cleaning) Purge: With the inlet process isolation valve of the pump closed, operate the pump with purge gas to the pump
for 20 to 30 minutes to remove any undesired residual gases from the pump’s internal. The inlet process isolation valve should be
open to start process pumping operation upon completion of the Start (Cleaning) Purge.
Содержание KINNEY SDV SDV-120
Страница 28: ...28 NEW SDV 320 EXPLODED VIEW DRAWING NOTES ...