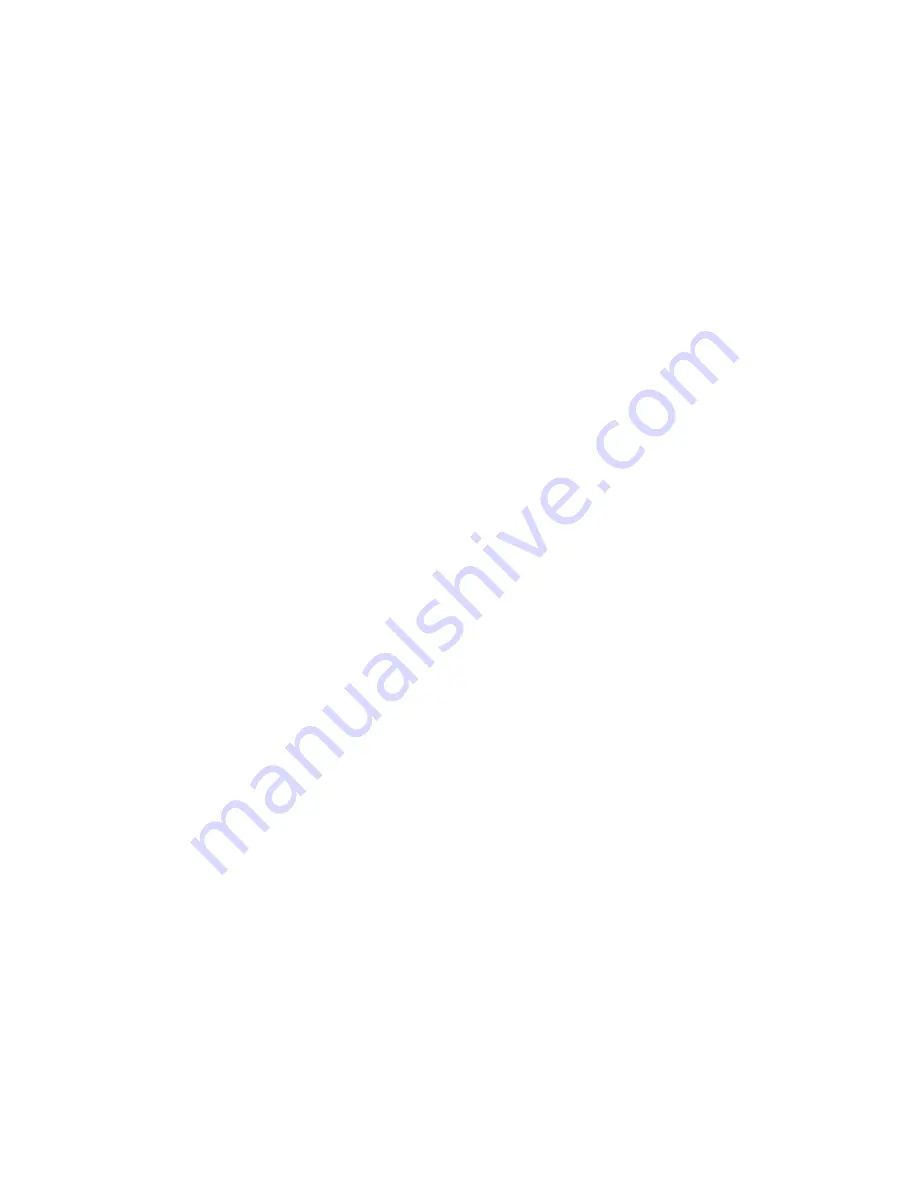
16
26. Remove set screws from Mechanical Seal Rotor (A) and pull out the Mechanical Seal Rotor (A)
27. Push out Screws
28. Remove bolts (M10) and separate the FEP from the pump casing
29. Press out Lip Seals, Lantern Rings and Mechanical Seal Stators (A)
30. Separate the Blind Plates from casing, covers and plates and inspect inside of the cooling jacket for any foreign material
buildup. Clean out foreign materials from cooling jacket, if there’s any.
31. Clean all parts with high-grade solvent and replace any worn or damaged parts with factory-approved parts.
REASSEMBLY: PRECAUTIONS AND PROCEDURE
Notes for the steps for the models after October 2005: This revision includes steps for the SDV pump models manufactured
after October 2005. The additional steps are noted by superscripted “new” on the right hand side of the step numbers, for
example, (54) “NEW”. These additional steps are applicable for the pumps with serial numbers as listed as below. For the pumps
manufactured before Oct. 2005, please skip these additional steps.
• SDV-120: S/N 406 and after
• SDV-430: S/N 352 and after
• SDV-200: S/N 263 and after
• SDV-800: S/N 241 and after
• SDV-320: S/N 404 and after
PRECAUTIONS
1. Apply lubricants after cleaned with light oil. Bearings should be handled with clean hands and tools.
2. Cleaning of parts should be done with soft, clean fabrics or tissue and oil should be applied. For such parts joining each
other and with high potential of oxidations, such as, keys, shaft threads etc; apply Molybdenum Disulfide on the joint areas for
easier disassembly.
3. Inner diameter surfaces of gears should be thoroughly cleaned prior to the installation.
4. If there’s any damaged packing, shim and/or spacer, it must be replaced with new ones of the same thickness.
REASSEMBLY PROCEDURE
SETUP OF SCREWS AND REP
1. Set NDE REP on two blocks or pipe stand with casing side facing upward
2. Insert both Drive and Driven Screws upright into the Rear End Plate (Drive Screw to right side). Keyway alignment is not
required at this step.
ASSEMBLY OF FEP PARTS AND SCREWS/SHAFTS
3. Press Lip Seals into FEP (Facing In position)
4. Insert Lantern Rings with O-rings (O-ring side UP). Ensure the O-rings are in place within the O-ring glands.
5. Check the Mechanical Seal Stator (A) O-rings materials of construction. Where the application requires special O-rings,
such as, Kalrez O-rings, ensure the O-rings on Mechanical Stator (A) are meet the requirements. If required, replace the
Mechanical Seal Stator (A) O-rings with correct O-rings.
6. Apply sealant to the outer surface of the Mechanical Seal Stator (A). Note: Ensure the material compatibility of the sealant
with the process vapor and/or gases. RTV-6702 is generally accepted for Oxygen services where the exposed area of RTV-
6702 to the process vapor and/or gases is relatively small. However, the end user must ensure the material compatibility.
7. Lubricate the carbon faces of the Mechanical Seal Stators (A) with a few drops of clean oil.
8. Press in Mechanical Seal Stators (A) into the FEP
9. Install DS and NDS Bearing Holders to the FEP and secure them with screws. This is a temporary installation and Bearing
Holders need to be removed after the setting of the FEP. (See step 10)
10. Place FEP onto Screws (process discharge nozzle to Left)
11. Remove DS and NDS Bearing Holders from the FEP.
12. Slide Mechanical Seal Rotors (A) onto the Screw Shafts.
13. Measure and record the depth from FEP face to the top of the Mechanical Seal Rotor (A)
14. Adjust Mechanical Seal Stator (A) clearance to 0.040 ~ 0.048 inches (1.0 ~ 1.2 mm) deep and tighten setscrews. Re-
measure the depth from FEP face to the top of the Mechanical Seal Rotor (A) as in step 13. Difference should be 0.040 ~
.048 inches (1.0 ~ 1.2 mm).
15. Replace DS and NDS shims and/or spacers, if there are any. (See step 5 of disassembly procedure.)
16. Insert Bearing Holders into the FEP
17. Insert Ball Bearings into the Bearing Holders
18. Secure Ball Bearings on the shafts with Lockwashers and Locknuts and bend one edge of Lockwashers to fix the locations.
Prior to securing Locknuts, insert a bronze plate or soft metal shim between Screws to keep the Screws from rotating.
19. Secure Bearing Holders with the setscrews.
20. Replace Bearing Stoppers and secure them with bolts (M8)
21. Measure the clearance between Screws and FEP. The clearance between Screws and FEP should be per the Table 7 Screw
Clearance Table.
Содержание KINNEY SDV SDV-120
Страница 28: ...28 NEW SDV 320 EXPLODED VIEW DRAWING NOTES ...