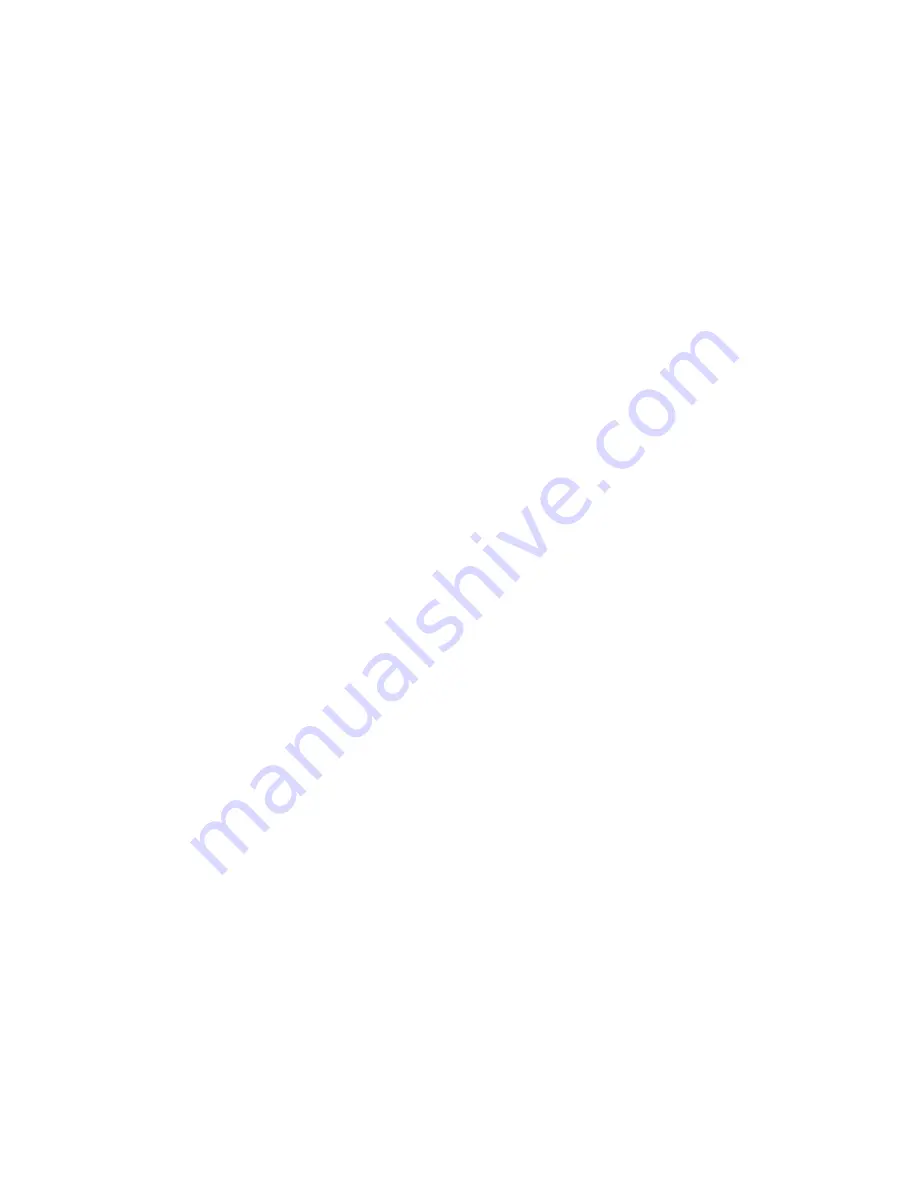
15
DISASSEMBLY: PRECAUTIONS AND PROCEDURE
Notes for the steps for the models after October 2005: This revision includes steps for the SDV pump models manufactured
after October 2005. The additional steps are noted by superscripted “new” on the right hand side of the step numbers, for
example, (54) “NEW”. These additional steps are applicable for the pumps with serial numbers as listed as below. For the pumps
manufactured before Oct. 2005, please skip these additional steps.
• SDV-120: S/N 406 and after
• SDV-430: S/N 352 and after
• SDV-200: S/N 263 and after
• SDV-800: S/N 241 and after
• SDV-320: S/N 404 and after
PRECAUTIONS
1. Disassembly of the screw/shaft assembly is strongly discouraged. If the screw/shaft assembly must be disassembled, please
contact factory and seek advice prior to disassembly of the screw/shaft assembly.
2. Measure and record the screw clearance through the process inlet nozzle at the point “E” shown on the “Figure 5 Screw
Clearance Measuring Point”. Check the measured clearance value against the screw clearance requirements listed on the
“Table 7 Screw Clearance Table”.
3. Place match marks on all connections and fittings.
4. Be careful not to damage the gaskets at the process and utility piping connections during the piping disassembly.
5. Take measurements and record of all gasket thicknesses after the disassembly of the process and utility piping connections.
6. Check all parts for any abnormal wear or damage during the disassembly. Damages on any part that joints to another parts
would greatly influence pump performance. Any damages on such parts must be repaired or replaced.
7. Keep all the disassembled parts in a clean and dust free place, especially for the mechanical seals, lip seals and bearing.
ABBREVIATIONS
DS:
Drive Side
NDS:
Non Drive Side
DE:
Drive End
NDE: Non Drive End
FEC:
Front End Cover
FEP:
Front End Plate
REP:
Rear End Plate
DISASSEMBLY PROCEDURE
FEC DISASSEMBLY
1. Disconnect all process and utility piping and electrical/controls connections
2. Remove motor, coupling & key
3. Drain oil and cooling liquid from the pump
4. Relocate the pump to a safe workbench suitable for disassembly/reassembly work. Workbench should have a hole on a flat
space for vertical orientation of the pump with the shaft underneath of the workbench surface.
5. Remove Seal Adaptor Housing Cover, Mechanical Seal Stator (B)
6. Remove Mechanical Seal Rotor (B)
7. Remove bolts from FEC and separate the FEC from FEP
8. Push out Ball Bearing
NDE (NON-DRIVE END) DISASSEMBLY
9. Set the pump assembly (less FEC) vertically on the work bench with REP on top
10. Remove set screws (M8) from Grease Cover and remove Grease Cover
11. Remove Locknuts and Lockwashers and remove bolts from REP
12. Remove NDE Plate: install set screws in the holes in REP and separate the REP from pump casing by tightening the set
screws
13. Push out Bearing, Spacer, Lip Seals, Lantern Rings NOTE: There are two (2) Lip Seals on each shaft on SDV-120 and
three (3) Lip Seals on each shaft for all other models.
14. Remove Slip Sleeves from each shaft DE Disassembly
15. Lift up the pump casing and reposition the pump on the work bench with FEP on top
16. Loosen the bolts in Powerlocks (Fetter Ring) and separate Powerlocks from the DS Timing Gear and pull out the DS Timing
Gear
17. Remove Locknut and Lockwasher
18. Remove NDS Timing Gear
19. Remove keys from shaft
20. Remove bolt (M8) from Bearing Stoppers and remove Bearing Stoppers
21. Remove Locknuts and Lockwashers
22. Mark (label) the DS and NDS Bearing Holders with a permanent maker
23. Separate the Bearing Holders from FEP
24. Separate the Bearings from Bearing Holders
25. Remove and label DS and NDS shims and/spacers, if there’s any. Label them accordingly for identifications.
Содержание KINNEY SDV SDV-120
Страница 28: ...28 NEW SDV 320 EXPLODED VIEW DRAWING NOTES ...