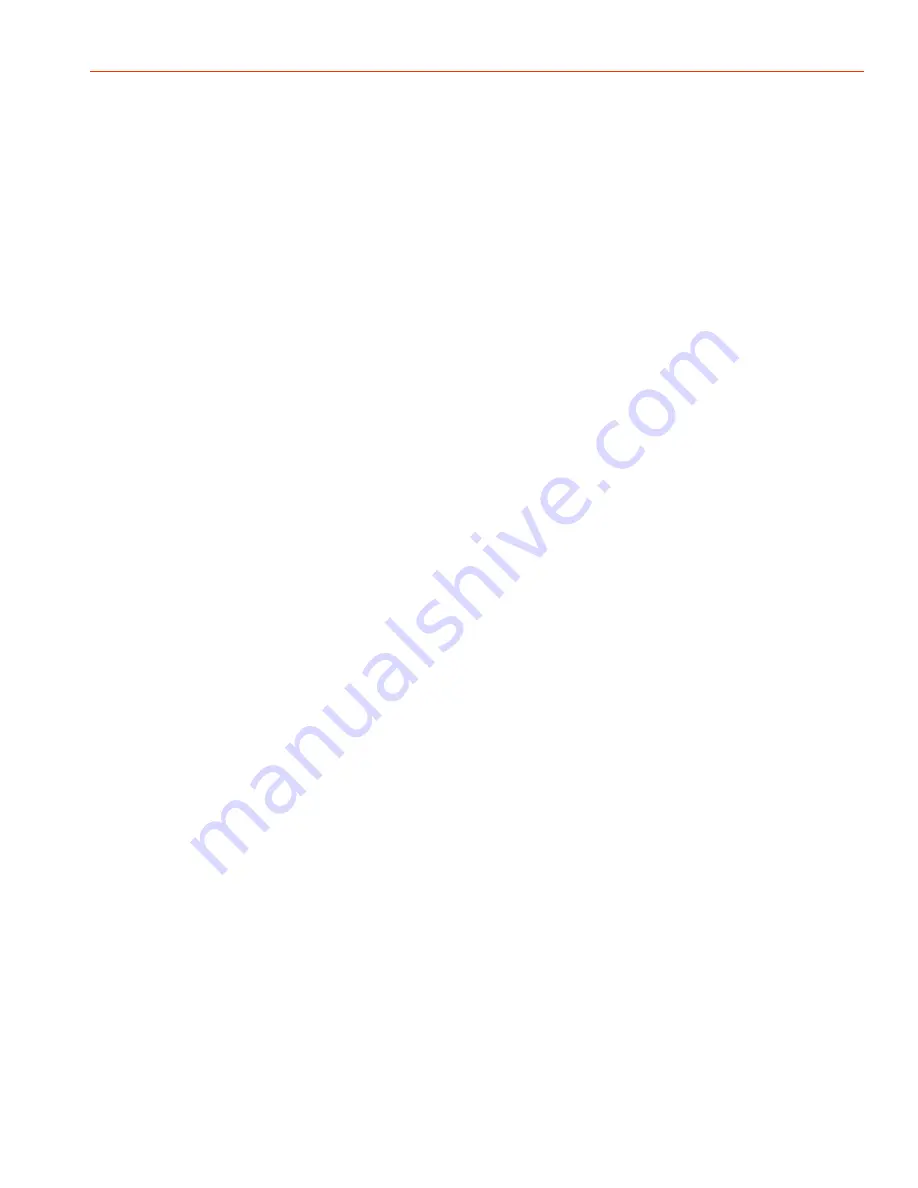
Page 7 of 38
WARNING
Failure to follow these instructions could result in serious bodily injury or death. Do not attempt to work on any Tuthill pump installation
before completing the steps below. Disconnect the drive so that it cannot be started while work is being performed. Review the Material
Safety Data Sheet (MSDS) applicable to the liquid being pumped to determine its characteristics and the precautions necessary to
ensure safe handling. Vent all pressure within the pump through the suction or discharge lines. All Tuthill pumps contain residual
hydraulic oil from the factory production test. Determine if this is compatible with the fluid you are pumping. If the fluid is incompatible,
then the pump must be fully flushed prior to use. If the pump is to be operated at elevated temperatures, the pump should be brought
up to operating temperatures gradually. Rapid or sudden introduction of liquids at elevated temperatures into the cold liquid chamber
of the pump could cause damage to pump externals, seals or other internal parts. Pumps can run dry provided provisions are made for
the mechanical seal if one is used. Failure to comply with this could cause severe damage to the mechanical seal parts. Pump needs to
be earthed separately to avoid a buildup of electro-static charge.
Installation
For optimum pump performance the suction line must be at least as large as the corresponding pump port. It should be as short as
possible in order to avoid excessive pressure drops and must be airtight. Locate the pump as close to the source of supply as conditions
permit, and if possible, below the level of the liquid in the reservoir. When necessary to locate the pump in a pit, provisions should be
made to safeguard against flooding. When handling high viscosity liquids, the speed of the pump must be reduced and the size of the
inlet lines increased to prevent cavitation. Refer to the NPSHr data for the pump.
Pumps should be filled with liquid at installation. The placement of a strainer on the suction side of the pump will restrict any solids
or abrasives from entering the pump, which could cause internal damage. Under no conditions should the pump be used to support
external piping loads (weight or expansion). Piping and other equipment should be independently supported. Piping strain can result
in misalignment, hot bearings, worn couplings, vibration, etc. It is important that the piping used be clean and free of chips and scales.
The discharge line must be designed with the maximum pressure rating of the pump in mind. Excessive pressure could cause damage
to your motor and/or pump. If a pressure relief valve has not been supplied with the pump, some other means of pressure protection
must be utilized. This could include in-line safety valves, pressure shutdown switches or other similar devices. Pumps are positive
displacement pumps and must be used in conjunction with a pressure relief mechanism.
Every pump installation should have a good foundation. Its structure should be sufficiently strong to hold the pump rigid and to absorb
any strain or shock that may be encountered. The installation should be leveled, checked for proper piping alignment, and then
fastened securely.
The alignment should be rechecked after the pump’s temperature has reached its operating temperature. Direct drive through
a traditional flexible coupling is recommended. However, do not expect the coupling to compensate for misalignment. Contact the
coupling manufacturer to determine the maximum amount of misalignment that the coupling can be subjected to. Never operate the
pumps without all the guards in place.
Direction of Flow
Tuthill Industrial Process Pumps may be operated in either direction. The direction of flow is dependent on the direction of rotation of
the pump drive shaft. When facing the drive shaft of the pump, a clockwise rotation provides a top suction port and a bottom discharge
port. This applies to Model 30A, 2A, 3A, 70A, 120A, 330 Pumps (Pages 11, 13, 15 & 17).
Model 600 Pumps are equipped with a vertical shaft arrangement (Page 25, 27, 29 & 31). On these models a clockwise drive shaft
rotation will provide a left hand suction port and a right hand discharge port. Flow would be from left to right when facing the drive
shaft.