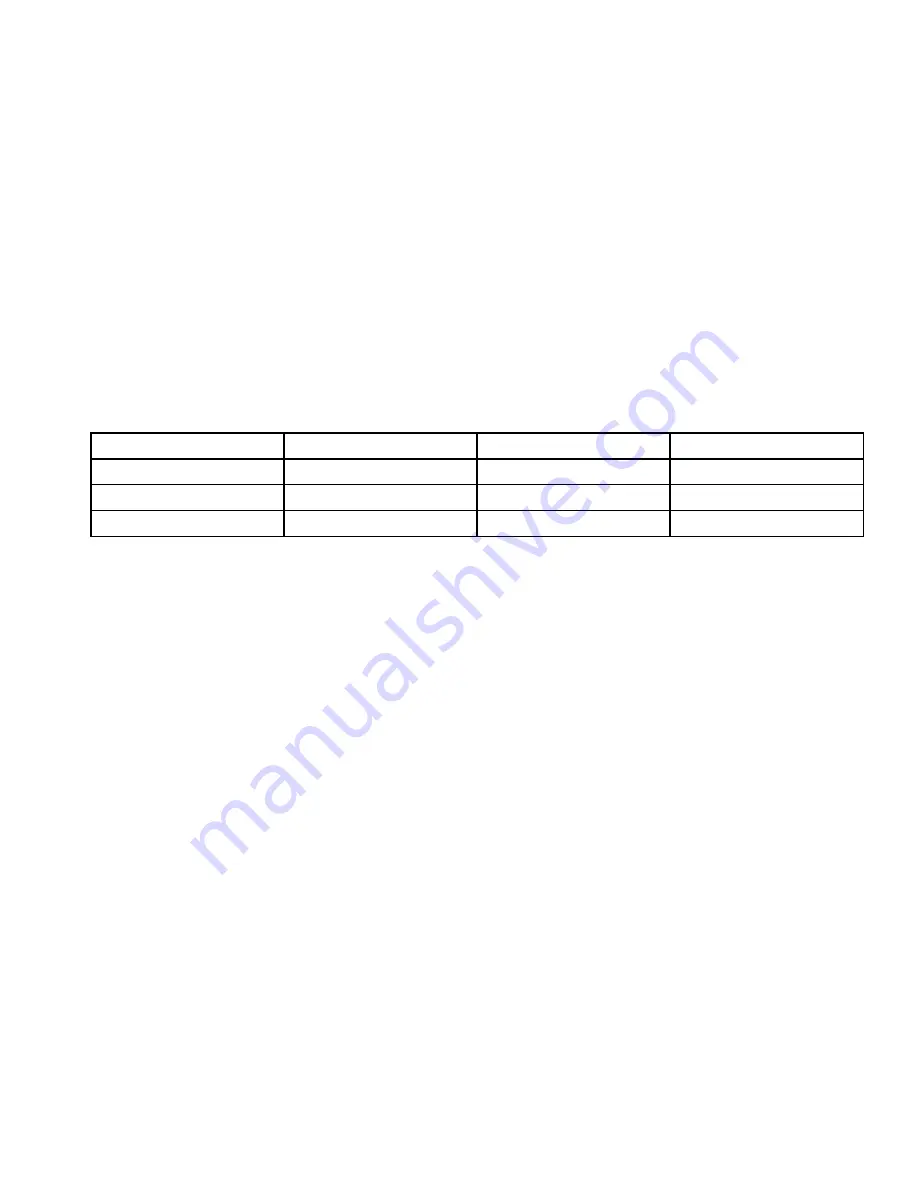
Page 33 of 38
8.
If the impellers are properly set on the shaft to dimensions from step 1, then the initial setting clearance will always be too large.
Thus, to move the impeller to the proper setting, add shims between bottom of bearing bore and the bearing outer race.The
following shims are available:
• Red .002”
• Blue .005”
• Pink .015”
9.
Grease faceplate bearings thru fittings on bearing caps.
10.
For the remaining reassembly procedure, refer to steps 1 - 16 in Minor Reassembly Instructions.
Packings
Installing Packings in Pumps
1.
Remove all old packing using a packing hook. Clean stuffing box and shaft thoroughly and examine shaft for wear or scoring. Check
bearings for wear as this can cause an eccentric shaft rotation resulting in excessive leakage. Packings will not act as a bearing. If
shaft surface is worn, replace shaft or have seal surface area resurfaced.
2.
Be certain the proper size packing is used. The following packing sizes will apply
Pump Model
Packing Size
Shaft Diameter
No. of Rings
70A & 120A
7/16” Square
1-7/8”
6
330
1/2” Square
2-1/4”
6
600
1/2” Square
2-1/2”
6
3.
Always cut packings into separate rings. Never coil around shaft. (standard factory packings are pre-cut and pre-formed) If bulk
packing is used cut each ring on a mandrel the same size as the pump shaft. Try rings in stuffing box to be certain that each ring fills
the seal chamber and that there is no gap between packing joints.
4.
Install one ring at a time, seating each ring independently. Use clean oil to lubricate shaft and inside of stuffing box. Joints should be
staggered and kept at least 90° apart. Each individual ring should be firmly seated with a tamping tool. Never depend entirely on
the gland to seat a set of packings. This practice will jam the last rings installed but leave the front rings loose. The result is excessive
and rapid wear.
5.
After last ring is installed, tighten gland nuts finger tight. Then start pump and take up nuts until leakage is decreased. Stopping
leakage at this point will cause packing to burn. If temperature rises in seal area, back off on packing nuts as this indicates excessive
gland pressure.
6.
Allow packing to leak freely for at least one hour when starting up a newly packed pump. Take up gland nuts gradually, 1/16 turn
every 5-10 minutes, until leakage stabilizes at about 3-5 drops per minute. If temperature in seal area increases, back off and start
over.
Note:
Replace packing when leakage cannot be controlled by further take-up of gland. Test results indicate that 70% of the wear
occurs on the first two rings of packing nearest the gland. Rings next to the gland work the hardest. The rings in the bottom of the
stuffing box serve to throttle some fluid pressure. On abrasive service the bottom ring takes most of the beating. Therefore, this ring
should be a firm ring.
How to Pack for Abrasive Liquids
As used here “Abrasives” is a broad term intended to cover the problem of packing against slurries, congealing liquids and the likes. They
cause the greatest damage to equipment, and present difficulties for packing. In general, this involves flush, purges and temperature
control. Hard facing on the shaft seal surfaces, such as stellite or ceramic, are also recommended. When pumping slurries and abrasives
an external source of clear or otherwise suitable liquid must be force fed at a pressure higher than that existing in the stuffing box. This
differential pressure is in the area of 10-25 psi.