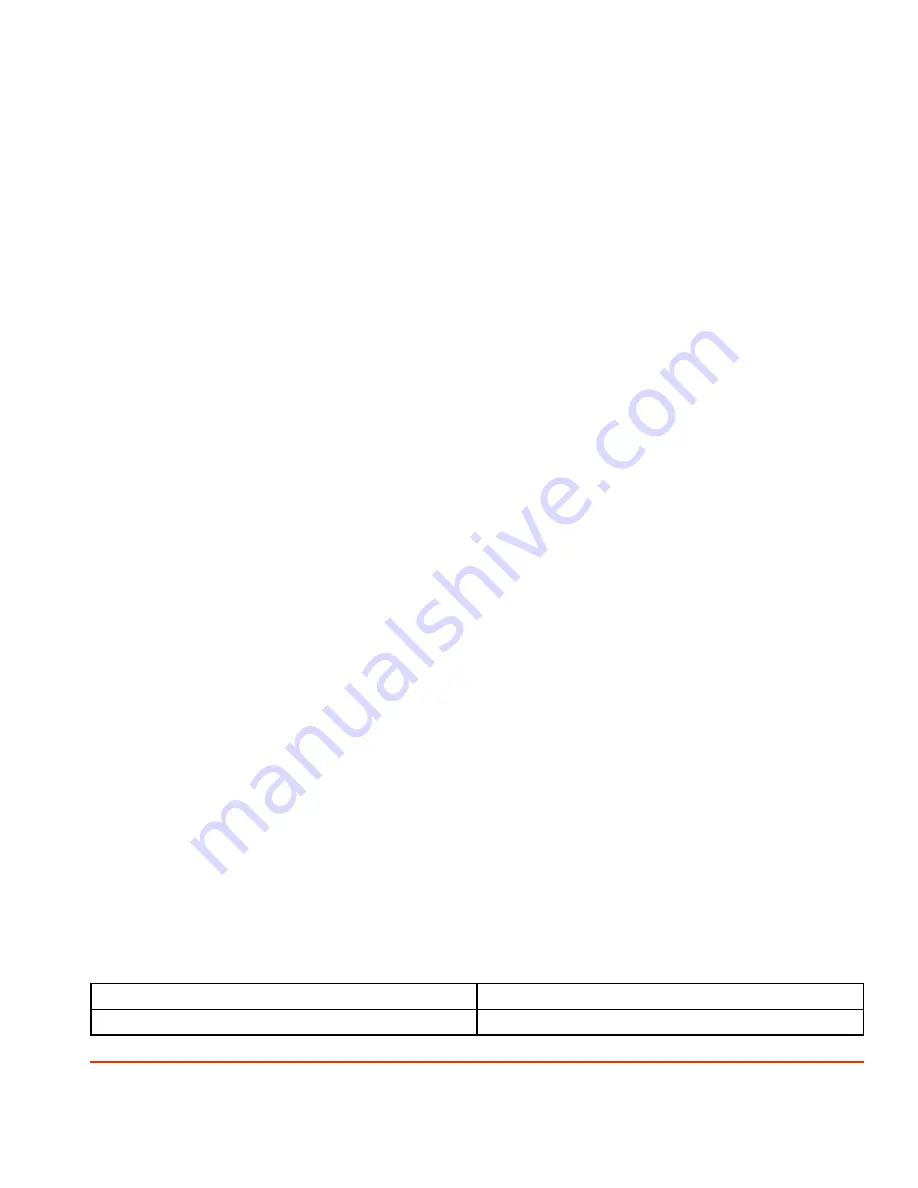
Page 31 of 38
the mechanical seal body axially on the shaft using the previous mark that was made during disassembly. After setting the end
clearances, tighten the seal set screws to the shaft. Install the mechanical seal gland back into the impeller housing stuffing box and
tighten the gland nuts (32). Re-install the pipe plugs (24). Also, reference Page 41 for additional mechanical seal information.
11.
Install drainpipe plug. Remove oil level plug. Fill gear case with lube oil (see lube chart on page 9) until oil comes out oil level hole.
Then install and tighten fill plug and oil level plug.
12.
Spin the assembled pump several times to be certain that there is no interference from incorrect timing. If no interference is
apparent, the pump is ready to be put back in service.
Major Disassembly Instructions
The first seven steps are the same as in the minor disassembly procedure. The major disassembly involves the disassembly of the
faceplate group.
8.
Place faceplate group in a vise. CAUTION: Use soft vise jaws to prevent damage to gasket seal surface.
9.
If Packing is used (reference assembly on page 26). Remove packing gland nuts (30) and slide packing gland (42) out of the way.
Then remove packing (36) from both seal chambers on faceplate. If pump is equipped with mechanical seals, refer to the seal
instructions that were shipped with the pump. Also, reference Page 39 for additional packing information. If Tuffseals are used
(reference assembly on page 28). Loosen Tuffseal set screws that lock the cartridge seal’s collar onto the shaft. Also, reference
Page 40 for additional Tuffseal information. If mechanical seals are used (reference assembly on page 30). Remove pipe plugs (34)
from impeller housing stuffing boxes. This allows access to the mechanical seal set screws holding the seal to the shaft. Mark the
shaft where the mechanical seal is so that the correct seal working length can be referenced upon re-assembly. Then loosen the
mechanical seal set screws. Loosen the mechanical seal gland nuts (30) and allow the mechanical seal gland to be loose on the
housing. Thus, when the shafts are pulled out of this area the gland will not fall off. Allow it to hang loosely on the studs. Also,
reference Page 41 for additional mechanical seal information.
10.
Remove six hex head bolts (25). Remove bearing covers (26). Press tines of lock washers (2) out of grooves on lock nut (1).
Remove lock nut.
11.
Remove bearing carrier (29) and bearing (27). CAUTION: Note the shims that are placed between bearing carrier (29) and
faceplate (33). If shafts and impellers are not replaced, these shims must be returned to the same position from which they were
removed. Now slide impeller and shaft assembly out through the fluid chamber side of faceplate.
12.
Remove the two double row faceplate ball bearings (27) from the bearing carriers (29). Then remove lip seals (10) and check
condition. Replace if required.
13.
If the shaft or impeller needs to be replaced, remove two set screws (5) from each impeller hub. Then press shafts through
impellers by placing impeller and shaft assembly in press with threaded stub shaft up. Remove impeller keys (4).
Reassembly
1.
Install impellers onto shafts [For non-galling impellers (ductile iron)]. Apply lubricant to shaft end on which impeller fits (White
lead is recommended). Slip impeller on shaft from the threaded stub shaft end. Install steel woodruff impeller key. Align keyway in
impeller with woodruff impeller key. Press impeller into proper position, and install setscrews as tight as possible. The dimensions
shown below are given from the shoulder on the shaft to the nearest flat face on the hub of the impeller. Install impellers onto
shafts [For galling impellers (stainless steel)] Impellers must be shrunk on the shafts, due to galling properties of the material. Heat
impellers to 500-550°F for 1 ½ -2 hours. Quickly assemble shaft and impeller with keys in place into proper position according to
the dimensions from above. Allow cooling.
Pump Size
Impeller Location (inches)
600
8.018 – 8.033
WARNING
Wear heat-resistant gloves when handling hot components.