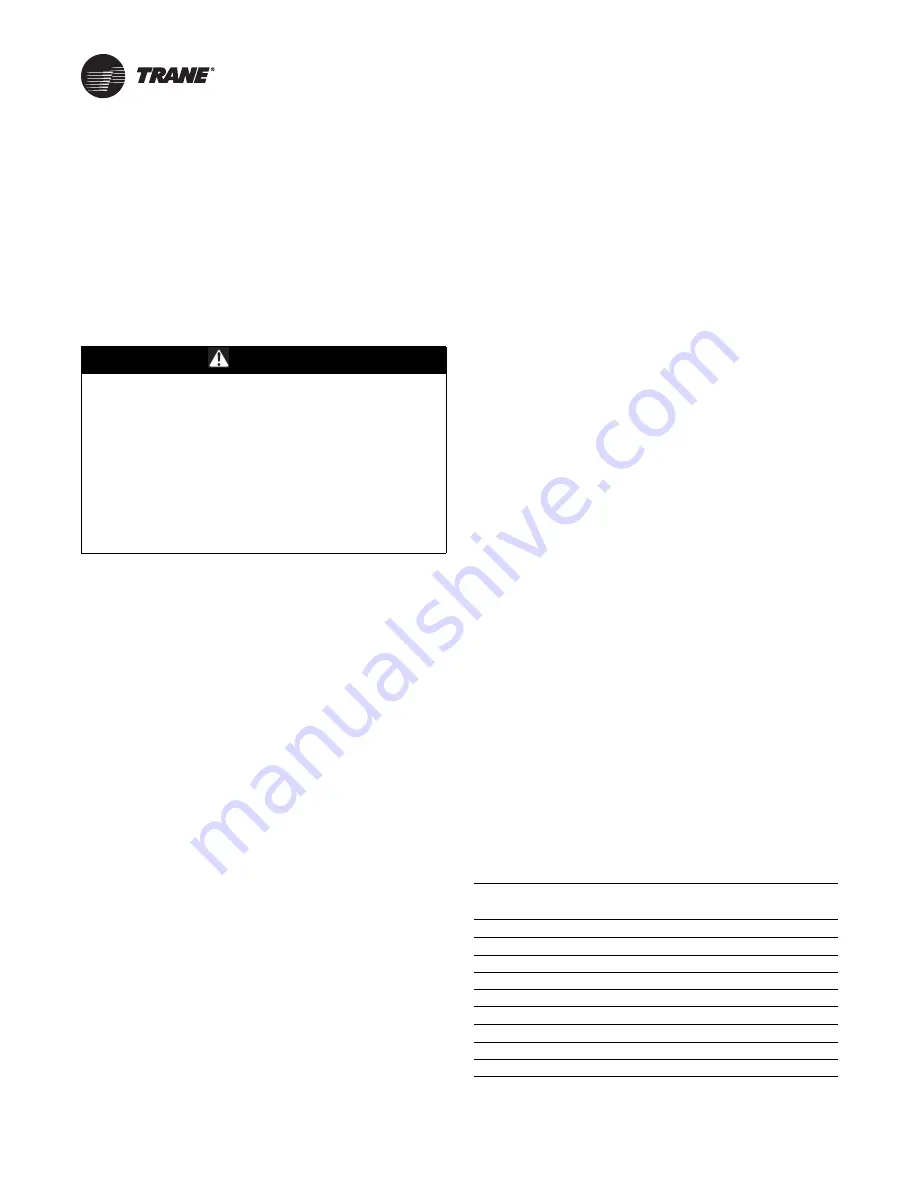
24
AFDK-SVU01C-EN
Mounting
Unit-Mounted (Refrigerant-
Cooled)
1. If present, disconnect existing power wiring and
ground connection.
2. Remove existing drive following the instructions given
in AFDE-SVU02*-EN (
Installation, Operation, and
Maintenance: Liquid Cooled Adaptive Frequency™
Drive with Tracer AdaptiView™ Control
).
WARNING
Refrigerant under Positive Pressure!
System contains oil and refrigerant and may be under
positive pressure. Recover refrigerant to relieve
pressure before opening the system. See unit
nameplate for refrigerant type. Do not use non-
approved refrigerants, refrigerant substitutes, or
refrigerant additives. Failure to recover refrigerant to
relieve pressure or the use of non-approved
refrigerants, refrigerant substitutes, or refrigerant
additives could result in an explosion which could
result in death or serious injury or equipment damage.
3. Carefully lift the drive into place. Do not bump or jolt
the drive while lifting. Refer to
.
4. Replace the mounting hardware used to secure the
drive enclosure to the lower mounting brackets. The
bolts should be torqued to 21 ft·lb (28.5 N·m).
5. Replace the mounting hardware used to secure the
drive enclosure to the motor terminal transition piece
or terminal board. The bolts should be torqued to
90 ft·lb (122 N·m).
6. Verify the flange fittings on the cabinet and the
CenTraVac chiller’s tubing are free of dirt, burrs, and
excessive nicks.
7. On both the inlet and outlet connections place a new
flange gasket over the studs on the back side of the
drive.
Notes:
•
Coat all gaskets very lightly with Loctite
®
515
sealant.
•
Frame 3 drives (405, 600 A) only:
On the refrigerant
inlet connection to the drive, place the inlet orifice
plate over the first gasket, then place another new
gasket over the orifice plate.
8. Align the chiller tubing and flanges over the studs on
the drive so that the flanges are straight and parallel.
Place the proper washers and nuts over the studs and
snug them up by hand. Be careful to maintain the
parallel alignment of the flanges.
9. Use a socket and torque wrench to further tighten the
flange bolts to their proper torques. Tighten the flange
bolts in small equal steps to ensure an equal draw-
down of the flange onto the gasket.
Flange Bolt Torques:
1/2-in. bolts = 90 ft·lb (122.1 N·m)
5/16-in. bolts = 22 ft·lb (29.9 N·m)
10. Inspect the connection for leaks.
11. Replace the panels and screws on the backside of the
drive that cover the refrigerant connections.
12. Reconnect the Flexibar conductors at the motor
terminals. The Flexibar connections to the motor
terminals should be torqued to 27 ft·lb (36.6 N·m).
Refer to
“Installing Unit-Mounted Output
13. Reconnect power, ground, and control wiring
connections. Refer to
Remote-Mounted (Water-Cooled)
1. Remove existing power connections and starter.
2. Prepare the location to install the drive.
Important:
•
The length of wire between the AFDK terminals and the
motor terminals must be no greater than 250 feet. The
maximum piping distance between the AFDK, heat-
exchanger assembly, and cooling source are described
in
. Ensure that the location selected
will not require wiring or piping distances greater than
these defined maximums.
•
Verify the location meets the requirements described
in
“Environmental Conditions,” p. 8
.
•
Clearances reserved for service and air-flow must be
maintained.
3. Frame 3 drives (405, 600 A) are provided with three
floor mounting rails. Frame 4 drives (900, 1200 A) are
provided with five floor mounting rails. These rails
must be installed and secured to the floor by the
following customer supplied hardware:
Quantity
Frame 3
Frame 4
Hardware to Install Floor Mounting Rails
1/2-13 X 1.500 Bolt
6
10
1/2 Flat Washer
10
20
1/2 Lock Washer
6
10
1/2-13 Nut
4
10
Hardware to Secure Enclosure to the Floor
1/2 x 3” Lag Screw
6
10
1/2” Fender Washer
6
10
1/2” Anchor
6
10