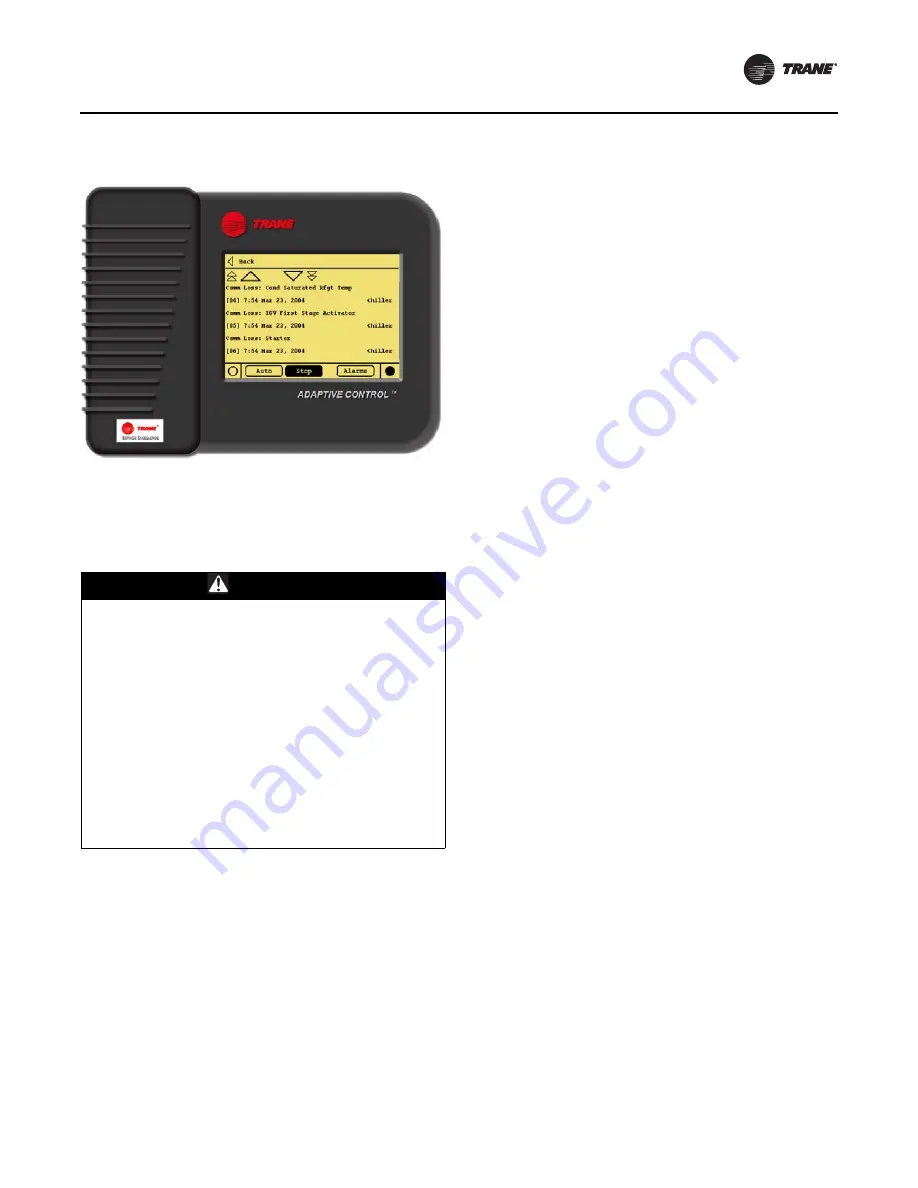
Troubleshooting
AFDK-SVU01C-EN
55
Troubleshooting
This section can assist in field troubleshooting LiquiFlo 2.0
drives, and can provide information, which others can use
to help you troubleshoot the drive.
1. Collect alarm/diagnostic and parameter information.
a. DO NOT cycle unit power or reset the controls.
Leave the AFD and UC800 or DynaView™ in their
present states.
b. Record the “AFD Last Diagnostic Code” using
Tracer™ TU or TechView™, as appropriate.
In Tracer TU, this value is available under the Unit
Status tab, in the Motor expanding box. In
TechView, this value is available in the Status view,
under the Motor tab.
c. Record all UC800 or DynaView active and historic
alarms/diagnostics. Make a full chiller service
report.
d. Document and check all applicable parameter
settings. This information can be verified from the
chiller nameplate, and by referring to this manual.
e. In the Binding view of the Tracer TU or TechView
service tool, verify there is a green face indicating
that the AFD Recomm Starter LLID is bound.
f. If an Operator Interface Module (OIM) is available,
record any drive diagnostics found.
2. Collect Chiller Information.
a. Note the following chiller information:
•
Operating mode and any sub-mode (i.e., 100%
or 75% load etc.)
•
Number of chiller starts, and hours of operation.
•
Time since last diagnostic shutdown (<1 minute,
<1 hour, >1 hour, etc.)
b. What was the chiller state at the time of the failure?
(Chiller starting? Running low load? Running full
load? etc.)
c. Record the chiller’s sales order and serial numbers,
and the drive’s serial and model numbers.
3. Troubleshooting
a. Measure and record the DC bus (via the Operator
Interface Module [OIM]).
b. Check ALL wiring (tightness, ribbon cables fully
seated, proper phasing, etc.)
c. Refer to the Rockwell manuals for further
troubleshooting information (manuals D2-3518-1
and D2-3496-2, or the most recent revisions).
d. If possible, use the Rockwell OIM and provide the
following drive parameter information:
•
LiquiFlo 2.0 (inverter) Parameters 49, 50, 209,
210, 224, 225, 226, 227, 228, 229, 230, 243, 244,
245, 246, 247, 248, 249, 250, 251, 252, 262, 263,
264, 265, 266, 267, 268, and 269.
4. Drive Over Temperature
a. Measure refrigerant pump discharge pressure and
compare to the condenser pressure. It should be
10–15 psid.
b. Measure drive coolant line delta-T.
c. Record parameters 120, 121, and 122 from the
active rectifier.
d. Operate the condenser at or below design
temperature. Elevated tower water temperatures
will raise drive temperatures.
e. The ambient temperature must remain below
specification (refer to
). Make sure the
fan grills are clean and operational.
f. Do not place manuals or prints below the power
module as this can block air flow.
Figure 27.
Unit control panel DynaView diagnostic
screen
WARNING
Hazardous Voltage w/Capacitors!
Disconnect all electric power, including remote
disconnects and discharge all motor start/run
capacitors before servicing. Follow proper lockout/
tagout procedures to ensure the power cannot be
inadvertently energized. For variable frequency drives
or other energy storing components provided by Trane
or others, refer to the appropriate manufacturer’s
literature for allowable waiting periods for discharge of
capacitors. Verify with an appropriate voltmeter that all
capacitors have discharged. Failure to disconnect
power and discharge capacitors before servicing could
result in death or serious injury.
For additional information regarding the safe discharge of
capacitors, see PROD-SVB06A-EN