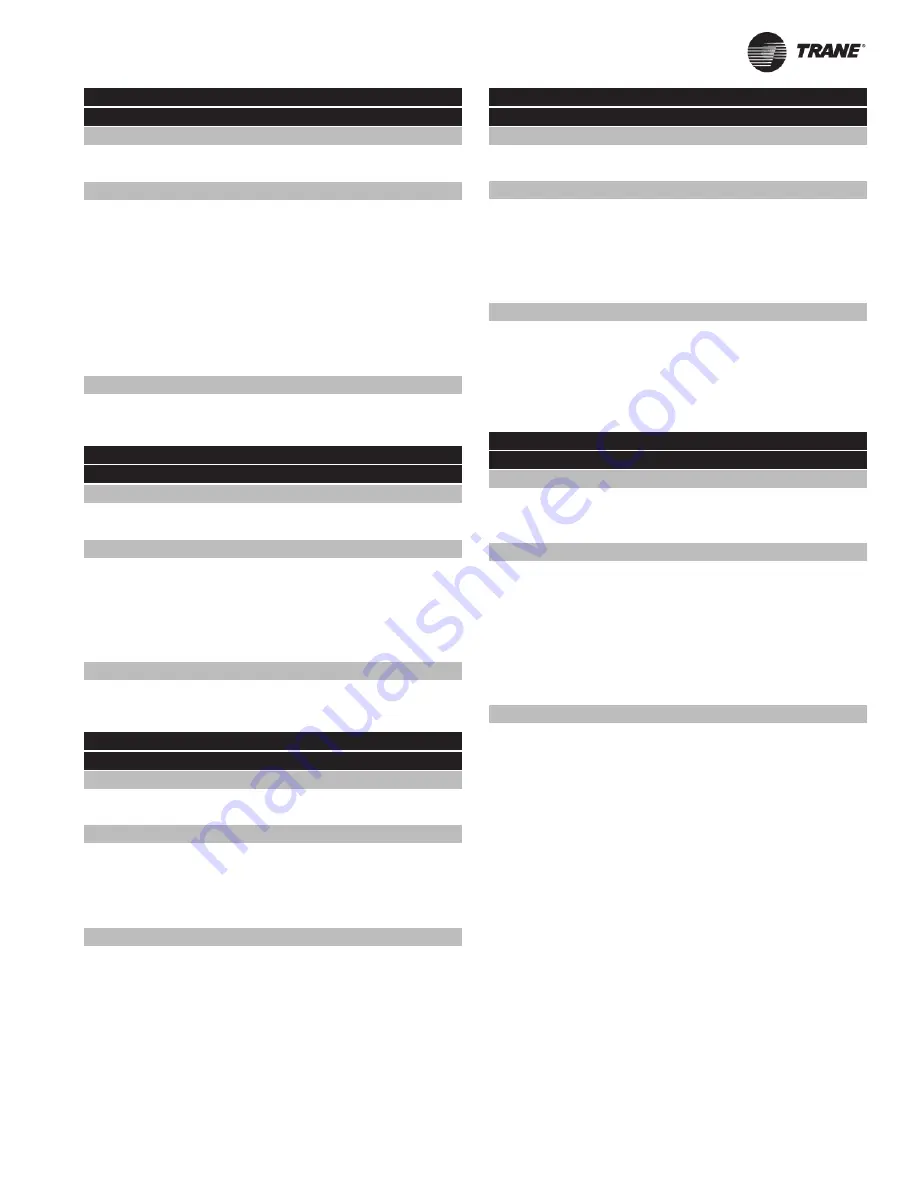
73
418
Setpoint 1
(SETPOINT 1)
Value:
Feedback Minimum to Feedback Maximum
★
0.000
Function:
Setpoint 1
is used to provide the setpoint reference for PID control with
one feedback signal. It is also used for the setpoint for zone one in
two-setpoint PID control. External and preset references may be added
to its value.
In open loop,
Setpoint 1
should be set to 0 to prevent parameter 417,
Feedback Function,
from affecting the reference.
See description of parameter 417,
Feedback Function
.
Description of choice:
Set the desired value within the programmed minimum and maximum.
The process unit is selected in parameter 415,
Process Units
.
419
Setpoint 2
(SETPOINT 2)
Value:
Feedback minimum to Feedback maximum
★
0.000
Function:
Setpoint 2 is used to provide the setpoint reference for zone two in
two-zone PID. In open loop,
Setpoint 2
should be set to 0, to prevent
parameter 417,
Feedback Function,
from affecting the reference.
See description of parameter 417.
Description of choice:
Set the required value. The process unit is selected in parameter 415,
Process Units
.
420
PID Normal/Inverse Control
(PID NOR/INV. CTRL)
Value:
★
Normal (NORMAL)
[0]
Inverse (INVERSE)
[1]
Function:
This determines how the drives PID controller responds to an error
between the setpoint and feedback.
Used in
Closed Loop
, (parameter 100).
Description of choice:
Select
normal
when the drive is to reduce the output frequency as the
feedback signal increases.
Select
inverse
when the drive is to increase the output frequency as the
feedback signal increases.
421
PID Anti-windup
(PID ANTI WINDUP)
Value:
Off (DISABLE)
[0]
★
On (ENABLE)
[1]
Function:
It is possible to choose whether the PID controller integrator is to
continue to sum the error signal when it is not possible to increase or
decrease the output frequency to correct the error.
Used in
Closed Loop
, parameter 100.
Description of choice:
The factory setting is
On
, which means that the error integrator is
cleared if either the current limit, the voltage limit or the maximum or
minimum frequency has been reached. The integrator will not function
again until regulation is possible. Select
Off
if the integrator is to
continue integrating even if it is not possible to correct the error.
422
PID Start-up Frequency
(PID START VALUE)
Value:
Minimum frequency to maximum frequency
(set by parameters 201 and 202)
★
0 Hz
Function:
Each time the drive is given a start command, the start-up frequency is
the speed the drive accelerates to before PID control is activated. The
drive will follow the acceleration ramp when a start signal is received as
if in open loop. When the programmed start-up frequency is reached, it
will change to closed loop operation.
Used in
Closed Loop
, parameter 100.
Description of choice:
Set the required start frequency. For software versions prior to 2.0, do
not set this frequency between 0.1 and 7.7 Hz.
NOTE
If drive is running in current limit before desired
start frequency is obtained, PID control will not
be activated. To avoid this, start frequency must
be low enough to ensure drive does not go into
current limit. This can be done during operation.
✭
I
ndicates factory default setting. Numbers in brackets [ ] represent selection as displayed on the serial bus.