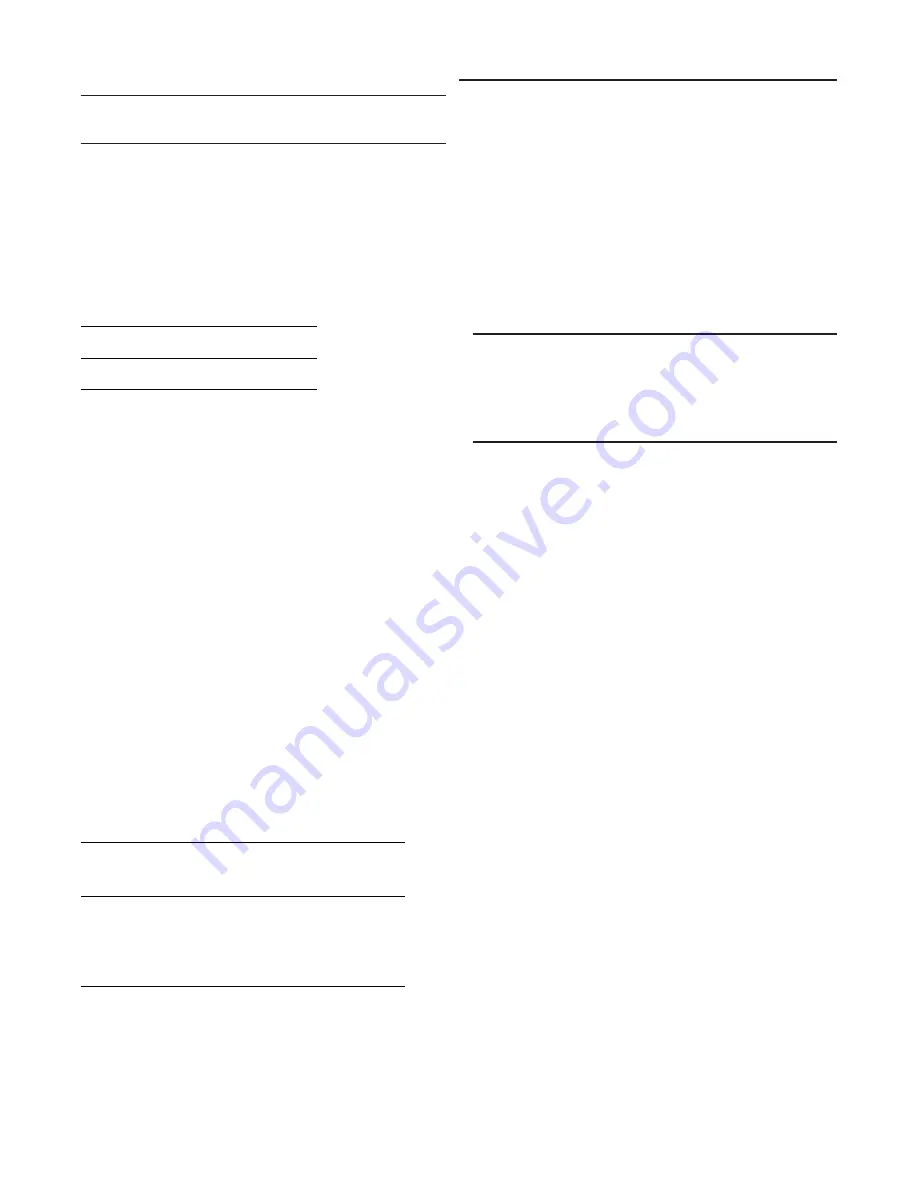
34
Installation
Note: Resistance in excess of 2.5 ohms per
conductor can cause deviations in the accuracy of
the controls.
b. Ensure that the wiring between the binary and
analog controls and the unit’s termination point does
not exceed two and a half (2.5) ohms/conductor for
the length of the run.
c.
Do not run the electrical wires transporting DC
signals in or around conduit housing high voltage
wires.
Table 6
DC Conductors
Distance from Unit Recommended
to Control
Wire Size
000 - 499 feet
16 gauge
500 - 1000 feet
14 gauge
Controls using DC Communication Links
Before installing any connecting wiring between the unit
and components utilizing a DC communication link, refer to
the connection diagram that shipped with the unit for the
electrical access and connection locations provided on the
unit.
a. Wiring for the components utilizing a DC
communication link must be shielded cable (Belden
8760 or equivalent). Ground the shield at one end
only.
b. Table 2 lists the conductor sizing guidelines that
must be followed when interconnecting a
communication link to the unit.
c. Communication link must not exceed 5,000 feet
maximum for each link.
d. Communication link must not pass between
buildings.
e.
Do not run the electrical wires transporting DC
signals in or around conduit housing AC voltage
wires.
Table 7
Maximum Communications Wiring Length
Maximum
Communication Link
Wiring Length
Maximum Capacitance
Between Conductors
1,000 feet
Up to 60 PF/FT
2,000 feet
Up to 50 PF/FT
3,000 feet
Up to 40 PF/FT
4,000 feet
Up to 30 PF/FT
5,000 feet
Up to 25 PF/FT
PF/FT = Picofarads/foot
BAS/NETWORK Communication Link
This option allows the unit control module (UCM) in the unit
to exchange information (i.e., operating setpoints and
AUTO/STOP commands) with a higher level control device,
such as a Tracer or a third party BAS. Twisted-pair conduc-
tors establish the bi-directional communications link be-
tween the unit’s control module and Tracer or a third party
BAS.
1. Refer to the Tracer installation literature to determine
proper communication link termination connections at the
Tracer unit. Multiple UCM’s on the communication link
can be connected in a “daisy chain” configuration.
2. Connect the shield of the communication link wiring to
the designated shield terminal at the Tracer 100.
3. Connect the shielded, twisted pair leads from the Tracer
to the proper terminals on the UCM. There is no polarity
requirement for this connection.
4. At the UCM, the shield should be cut off and taped to
prevent any contact between the shield and ground.
Note: On multiple unit installations, connect the
shield between each “daisy- chained” UCM in the
system to the shield of the twisted-pair leads going
to the next unit in line. Tape the spliced connection
to prevent any contact between the shield and
ground. At the last UCM on the link, the shield
should be cut off and taped.
Ice Building Control Option
The CGM provides auxiliary control for a customer speci-
fied/installed contact closure for ice making. When this field
installed normally open contact (5K86) is provided, the
chiller will run normally. Upon contact closure, the unit will
operate fully loaded until the entering water temperature
falls below the preprogrammed ice building setpoint. High
quality silver or gold-plated contacts are recommended.
The field supplied contacts must be compatible with 24
VDC, 12 mA resistive load.
Connect the 5K86 relay contacts to the proper terminals on
1TB4 as illustrated in Figure 12A.
Compressor Inhibit / KW Limit
When a unit is equipped with a TCI module, the Demand
Limit request is comunicated from Tracer. When a unit is
equipped with GBAS (0-5V and/or 0-10V), a customer pro-
vided/installed remote contact (5K89) initiates the demand
limit function. When the contact is “Open”, the chiller will
operate normally. When the contact closes, the unit will be
limited to the programmed operating capacity (25%, 50%,
75%, or 100%). When the contact opens, normal chiller op-
eration is restored.
High quality silver or gold-plated contacts are recom-
mended. These customer-supplied contacts must be com-
patible with 24 VDC, 12 mA resistive load. Refer to the wire
selection Table 6 for proper wire size and Figure 12B or Fig-
ure 12C for proper termination points.
Connect the wiring from the field supplied normally open
contacts between terminals 5 and 6 on 1TB16, if 0 - 5 Volt
GBAS is installed.
Connect the wiring from the field supplied normally open
contacts between terminals 1 and 2 on 1TB17, if 0 - 10 Volt
GBAS is installed.
Connect the wiring from the field supplied normally open
contacts between the proper terminals on 1TB16 and
1TB17 when both GBAS modules are installed. Refer to the
appropriate wiring diagram illustrated in Figure 12B and
Figure 12C for connections.
Содержание IntelliPak CG-SVX02B-EN
Страница 10: ...10 General Information Module Mounting Locations Screw Hole...
Страница 12: ...12 Figure 1 Typical Installation Clearances for Single Multiple or Pit Applications...
Страница 13: ...13 Figure 2 C20 Ton Unit Dimensional Data Recommended Clearances...
Страница 14: ...14 Figure 2 C25 Ton Unit Dimensional Data Recommended Clearances...
Страница 15: ...15 Figure 2 C30 Ton Unit Dimensional Data Recommended Clearances...
Страница 16: ...16 Figure 2 C40 Ton Unit Dimensional Data Recommended Clearances...
Страница 17: ...17 Figure 2 C50 Ton Unit Dimensional Data Recommended Clearances...
Страница 18: ...18 Figure 2 C60 Ton Unit Dimensional Data Recommended Clearances...
Страница 35: ...35...
Страница 36: ...36 Figure 12B Typical GBAS 0 5 Volt Connections Diagram...
Страница 37: ...37...
Страница 38: ...38...
Страница 63: ...63...
Страница 64: ......