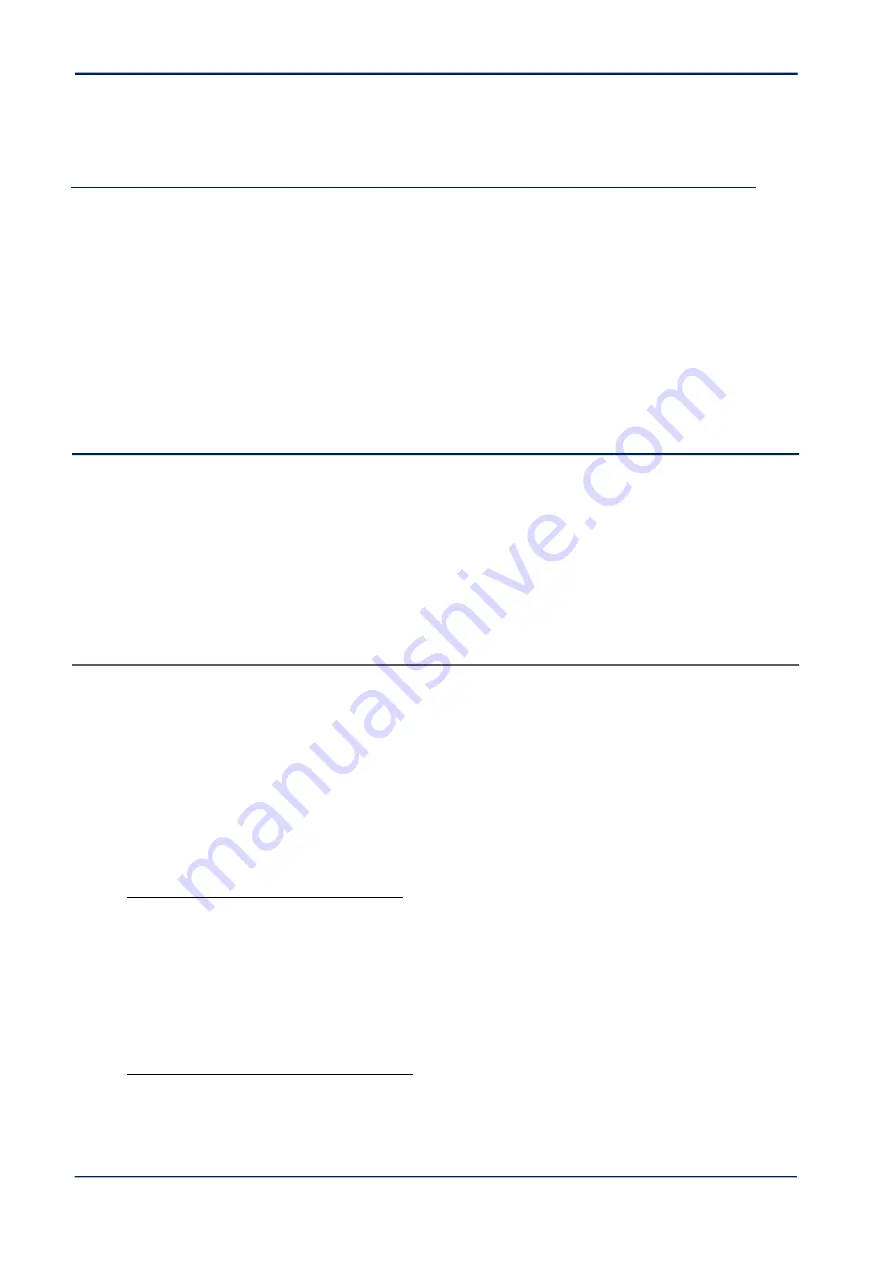
ISOBUS ARTEMIS - SEED DRILL CONTROLLER
4
5.3
Calibrating systems with ‘Accord’ type metering mechanisms.
20
6.
ALARM CODES
21
1 Introduction
This manual provides operator
basic
instructions for both single-channel and multi-
channel generic Isobus “Artemis” Seed
Drill Controller application. It also includes settings in the “Drill Setup” menu accessible by the operator. Information on
Technician and Factory level settings are not included in this manual.
NOTE:
Illustrations in this manual are based on a Topcon X25 terminal. The actual Artemis app screen display/button layout and
functions may vary slightly from that shown, depending on the specific implement being controlled, the UT the app is being
run on, its GUI and user-defined settings. If necessary, please refer to the manufacturers user manual for setup and loading
the Artemis app on other UT’s.
1.1 System Overview
The Artemis is an ISOBUS-compatible, monitoring and application control system for seed drills. It may be configured with
up to 4 control channels. Forward speed measurement and cutout sensing enables full proportional control, to maintain
(within limits) a set application of one or more products irrespective of changes in forward speed.
In its simplest application, the Artemis may be setup in a single-channel configuration to control a single motor as shown in
figure 1. Additional CAN modules enable multi-channel configurations for combined seed/fertiliser/pellet application
(including electro-hydraulic control), to suit a wide range of drill makes and models.
1.1.1 System Components
The system will vary depending on the drill make and model, but will be some combination of one or more of the following,
The main electronic components are,
▪
ISOBUS UT
▪
ISOBUS/CAN Bridge Module
–
the “brains” of the
system, containing the control software. It also contains the graphics
(the ‘Object Pool”), for the GUI to be displayed on any ISOBUS
-compliant terminal.
▪
Motor Control (MCM) CAN Module
–
CANBUS interface for a gearmotor and sensors.
▪
Applicator Control (APM) CAN Module
–
CANBUS interface for an Applicator system (optional).
▪
I/O (HBM) CAN Module
–
CANBUS interface for other switches, sensors and actuators.
Connected via the Motor Control Module (‘MCM’)
▪
Gearmotor
–
driving either single or multiple metering units.
▪
Shaft Speed Confirmation sensor
–
a magnetic sensor that confirms that the motor is driving the metering unit.
▪
Forward Speed Sensor
–
Speed signal sent from ISOBUS UT.
▪
Area Cutout Switch(s)
- one or two magnetic sensors or finger switch positioned to detect when the drill is lowered/raised
into or out of work. It can be configured to also provide the tramline advance signal.
▪
Priming Switch
–
manually operates the metering motor to dispense product for calibration purposes.
Connected via the Tramline Co
ntrol Module (‘HBM’)
▪
Fan Speed Sensor(s)
- a magnetic sensor on the fan drive.
Содержание ISOBUS Artemis
Страница 1: ...859 UK ISOBUS Artemis Seed Drill Controller Calibration and Operation Manual ...
Страница 2: ......
Страница 27: ......