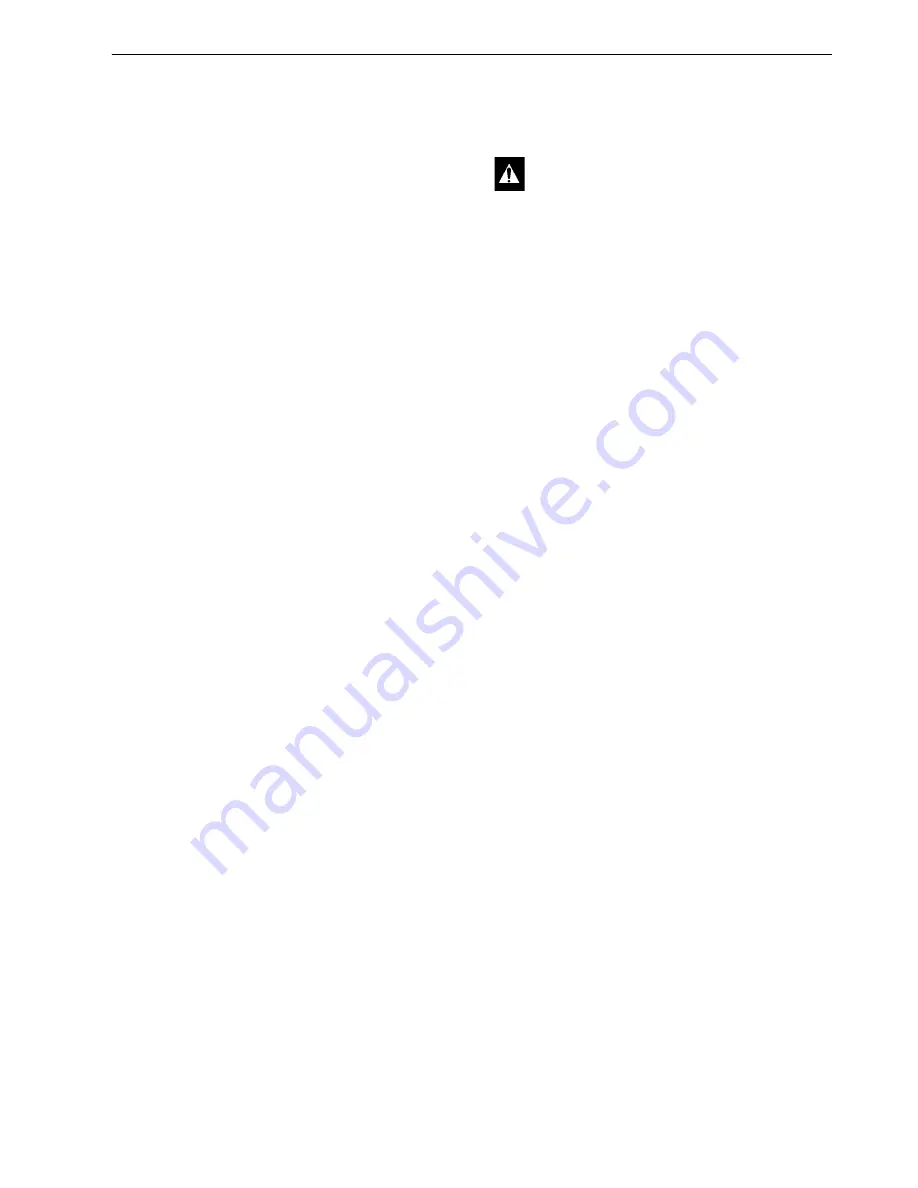
Refrigeration Service Procedures
151
Installation
1. Apply a refrigerant Loctite to the threads of
the HPCO.
2. Install and tighten the HPCO and reconnect
the wires.
3. Pressurize the system and test for leaks.
4. If no leaks are found, evacuate the
system.
5. Recharge the unit with refrigerant and check
the compressor oil.
High Pressure Relief Valve
Replacement
NOTE: Determine the cause of extremely high
discharge pressure before replacing the High
Pressure Relief Valve.
Removal
1. Recover the refrigerant charge.
2. Unscrew and remove the high pressure relief
valve from the receiver tank.
Installation
1. Apply a refrigerant oil to the O-ring of the
high pressure relief valve.
2. Install and tighten the high pressure relief
valve.
3. Pressurize the system and test for leaks.
4. If no leaks are found, replace the liquid line
drier then evacuate the
system.
5. Recharge the unit with refrigerant and check
the compressor oil.
6. Verify proper unit operation.
Hot Gas Solenoid (HGS) Test
1. Attach a gauge manifold to the suction service
valve and the discharge service port. Attach
another low pressure gauge to the suction
access port located in the suction line near the
accumulator inlet. Low loss fittings must be
used on the hoses connected to the discharge
service port and the suction access port.
2. Operate the unit in low speed cool.
3. Front seat the receiver tank outlet valve and
allow the low side to pump down to 0 to 5 in.
Hg vacuum (0 to -17 kPa).
4. Turn the unit Off.
5. Front seat the suction service valve to isolate
the low side while it is still in a vacuum.
6. Watch the low pressure gauge attached to the
suction access port. The low side pressure
should not rise. It it does, there could be a leak
through one (or more) of following
components: hot gas solenoid, liquid injection
solenoid, purge valve, or receiver tank
pressure check valve.
7. Check the temperatures of the refrigeration
lines on each side of the HGS by hand. A
temperature difference between the two sides
of the HGS indicates it is leaking.
8. Use the Mechanics/Premium HMI Control
Panel to enter the Interface Board Test Mode.
Refer to the appropriate Microprocessor
Diagnostic Manual for specific information
about the Interface Board Test Mode.
9. From the Interface Board Test Mode select
Hot Gas Solenoid.
10. Momentarily (for approximately 1 second)
energize the HGS with the Interface Board
Test Mode. The low side pressure should rise
slightly. If the low side pressure does not rise,
the HGS is not opening. Check the continuity
of the wiring and the solenoid coil before
assuming the solenoid is faulty.
11. Back seat the receiver tank outlet valve and
the suction service valve. Perform a
“Refrigerant Gauge Removal” procedure.
In-Line Check Valve
Replacement
This unit uses some in-line check valves. An
in-line check valve is not repairable and must be
replaced if it fails. A heat sink must be used on the
in-line check valve when it is being soldered in
place to prevent damage to the neoprene seal.
CAUTION: Do not run scroll compressor
in a vacuum for more than 1 minute.
Содержание T-1080S
Страница 102: ...Engine Maintenance 101 Figure 182 Fuel and Oil System Components ...
Страница 182: ...Index 181 Unit Options 23 W wiring 79 wiring diagrams index 182 ...
Страница 184: ...183 Schematic Diagram Page 1 of 2 RELEASED 06 Jul 2015 13 52 47 GMT 7 ...
Страница 185: ...184 Schematic Diagram Page 2 of 2 RELEASED 06 Jul 2015 13 52 47 GMT 7 ...
Страница 186: ...185 Wiring Diagram Page 1 of 5 ...
Страница 187: ...186 Wiring Diagram Page 2 of 5 RELEASED 06 Jul 2015 13 52 47 GMT ...
Страница 188: ...187 Wiring Diagram Page 3 of 5 ...
Страница 189: ...188 Wiring Diagram Page 4 of 5 RELEASED 06 Jul 2015 13 52 47 GMT ...
Страница 190: ...189 Wiring Diagram Page 5 of 5 ...