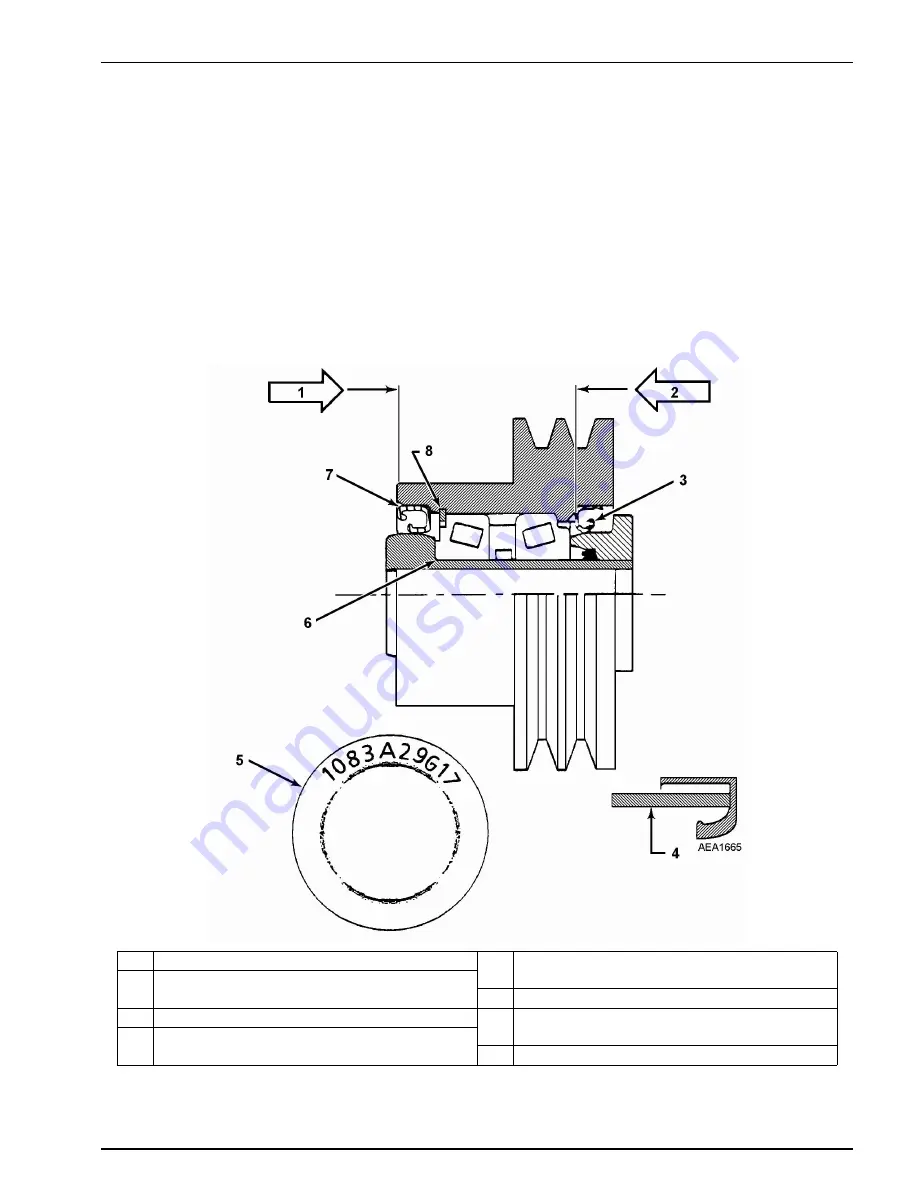
Engine Maintenance (Rev. 04/03)
85
Installation Procedure
To perform a seal change the following procedure is recom-
mended:
1.
Remove idler pulley from the unit.
2.
Remove the two seals and the retaining snap ring
(DISCARD OLD SEALS AND SNAP RING).
KD-II SR IDLER PULLEY SEAL
INSTALLATION
NOTE: KD-II SR Idler Pulleys use seal assembly P/N
33-1924. The retaining spring is deleted and to prevent
pressure buildup in the pulley assembly, the seals are
installed with the seal lip facing outward. See diagram
below.
1.
MAJOR: FLUSH SEAL THIS SIDE
5.
Thermo King Drawing Number on Seal
(P/N 33-1924)
2.
MAJOR: INSTALL SEAL SEATED AGAINST
SHOULDER
6.
Bearing F(P/N 77-0889)
3.
Apply Grease to Lip of Seal (P/N 203-386)
7.
Install Seal with Seal Lip Facing Outward
“Backwards”
4.
Use a Pipe with a 1-3/4 in. O.D. and 1/8 in. Wall
Thickness to Install the Seal
8.
Snap Ring
KD-II SR Idler Pulley Seal Installation
Содержание KD-II SR
Страница 4: ......
Страница 8: ......
Страница 13: ...Safety Precautions Rev 04 03 v AEA40...
Страница 14: ...Safety Precautions Rev 04 03 vi AEA38...
Страница 33: ...Unit Description Rev 04 03 19 1 Evaporator 2 Access Door Rear View Curbside KD II SR 1 2 AEA38...
Страница 37: ...Unit Description Rev 04 03 23 Power Receptacle Box KD II SR 50 AEA42...
Страница 38: ...Unit Description Rev 04 03 24 1 Keypad 2 LED Display THERMOGUARD Remote Control Panel AEA43 1 2...
Страница 42: ...P T System Description Rev 04 03 28 High Voltage Tray No Options High Voltage Tray with Phase Correction...
Страница 44: ...P T System Description Rev 04 03 30 High Voltage Tray with Single Phase Power and Electric Heater...
Страница 58: ...Remote Control Panel Features Rev 04 03 44...
Страница 112: ...Refrigeration Maintenance Rev 04 03 98...
Страница 120: ...106...
Страница 146: ...132...
Страница 156: ...142...
Страница 162: ...148...
Страница 170: ...156...
Страница 172: ...158...
Страница 173: ...159 KD II 30 Schematic Diagram Page 1 of 2...
Страница 174: ...160 KD II 30 Schematic Diagram Page 2 of 2...
Страница 175: ...161 KD II 30 Wiring Diagram Page 1 of 2...
Страница 176: ...162 KD II 30 Wiring Diagram Page 2 of 2...
Страница 177: ...163 KD II 50 Schematic Diagram Page 1 of 2...
Страница 178: ...164 KD II 50 Schematic Diagram Page 2 of 2...
Страница 179: ...165 KD II 50 Wiring Diagram Page 1 of 2...
Страница 180: ...166 KD II 50 Wiring Diagram Page 2 of 2...
Страница 181: ...167 KD II 50 SR 230 1 60 Wiring Diagram Page 1 of 2...
Страница 182: ...168 KD II 50 SR 230 1 60 Wiring Diagram Page 2 of 2...