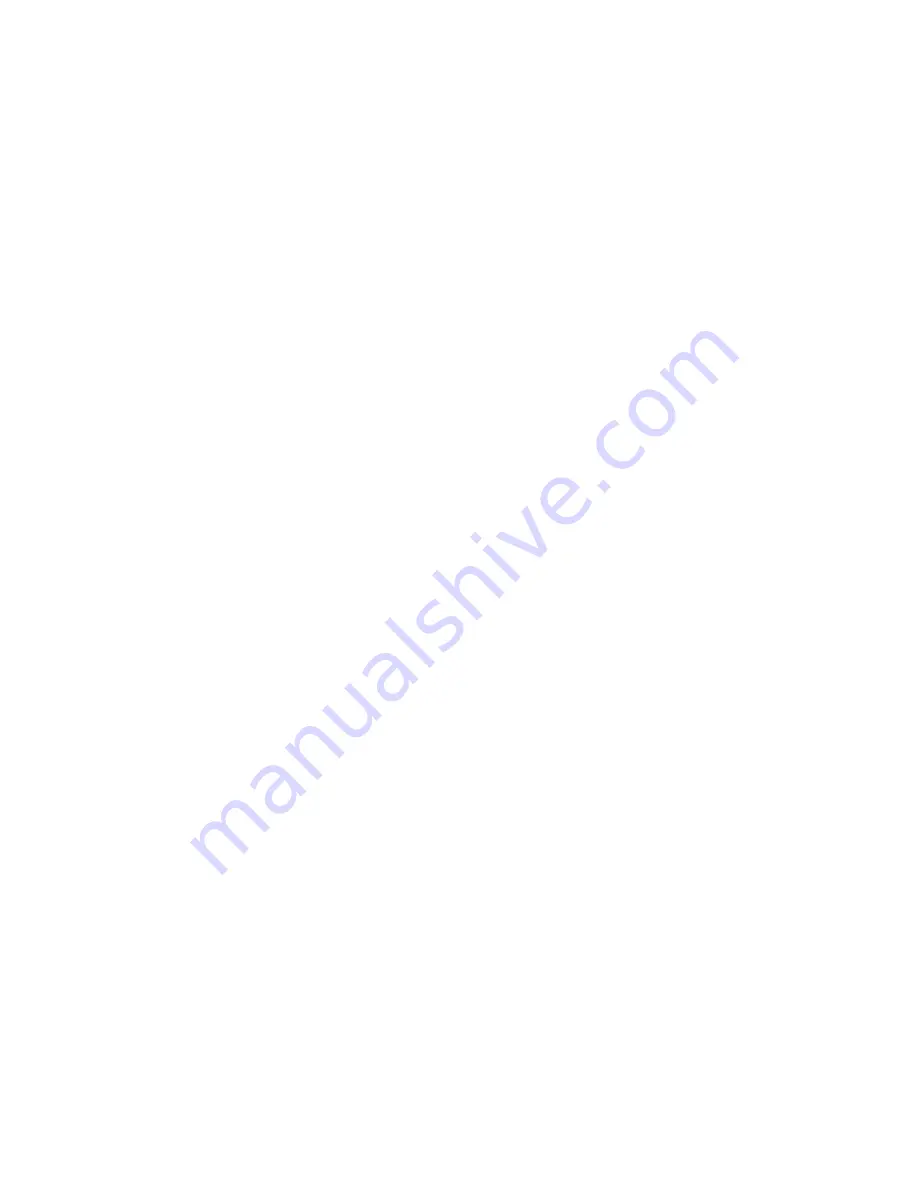
21
Installation
•
Mount the fluidised bath in the position where it is to be used. It is important to ensure
that the bath is level, otherwise it will fluidise incorrectly. This will lead to the formation of
large temperature gradients across the bath which results in premature heater failure and
possible damage to the porous plate and inner container assemblies.
•
Connect any associated fume treatment equipment to the fluidised bath effluent gas
extract duct. See section which follows on Fume Cleaning.
•
Check that the heater isolation resistance (measured from the load side of the solid state
relay, to earth) is at least 2.5M ohm before connecting the electrical circuit to the
electrical supply. See attached circuit diagram for connection details and the unit rating
plate for details of the electrical supply required.
•
The compressed air supply to the fluidised bath must be clean, dry, and free from oil.
•
If a manual control option is fitted, close the air flow adjusting valve which is situated on
the front of the control console, and connect the air inlet port at the rear of the control
console to a suitable dry, clean air supply. Make sure that the pressure delivered to the
fluidized bath is between 204kPa (30psi) and 1030kPa (150psi), and that the compressed
air line is capable of supplying sufficient air to fluidise the bath (see specification details).
•
Fill the fluidised bath with a sufficient quantity of aluminium oxide so that, when fluidised,
the distance between the top of the aluminium oxide and the top of the bath is 120mm
when the bath is fully loaded.
•
Should the fluidised bath be stored for long periods of time under damp or humid
conditions, moisture maybe absorbed by the alumina which is hydroscopic. To avoid
violent fluidisation which occurs when damp alumina is heated above 100ºC, operate the
bath for a period of approximately 8 hours at 90ºC prior to operation at elevated
temperatures.
•
NEVER ADD COLD OR DAMP ALUMINA TO A HOT BATH AS THIS WILL ALSO
•
CAUSE VIOLENT FLUIDISATION WHICH CAN BE DANGEROUS. Allow the bath to
cool then add the fresh alumina. If this fresh alumina is a large proportion of the charge
then dry the whole charge as above.
•
Set the air pressure regulator, which is situated within the pneumatic section of the
control console to 204kPa (30 psi).
•
The following table shows the recommended fluidising air flow rates which should be
used to achieve the correct level of fluidisation.
§
100
°
C to 200
°
C
220 l/min
§
200
°
C to 400
°
C
180 l/min
§
400
°
C to 600
°
C
150 l/min
The figures quoted are approximate and may need to be varied depending upon the
working load, eg the bath may have to be .overfluidised. to avoid the creation of dead
spots above the immersed object.
•
To safeguard the fluidised bath from damage two safety features are included in the
control console: an overtemperature cut-out (set at 630
°
C) which guards against
controller failure, and an air pressure switch which inhibits operation if the compressed air
supply to the fluidised bath fails. Both of these devices isolated the electrical supply to the
heater elements and illuminate the cut-out indicator in a fault condition.
Содержание IFB-201
Страница 1: ...IFB 201 OPERATOR S MANUAL...
Страница 3: ...3 Spare Parts 31 Accessories 31 Circuit Diagrams 32...
Страница 31: ...32 Circuit Diagrams...
Страница 32: ...33...
Страница 33: ...34...