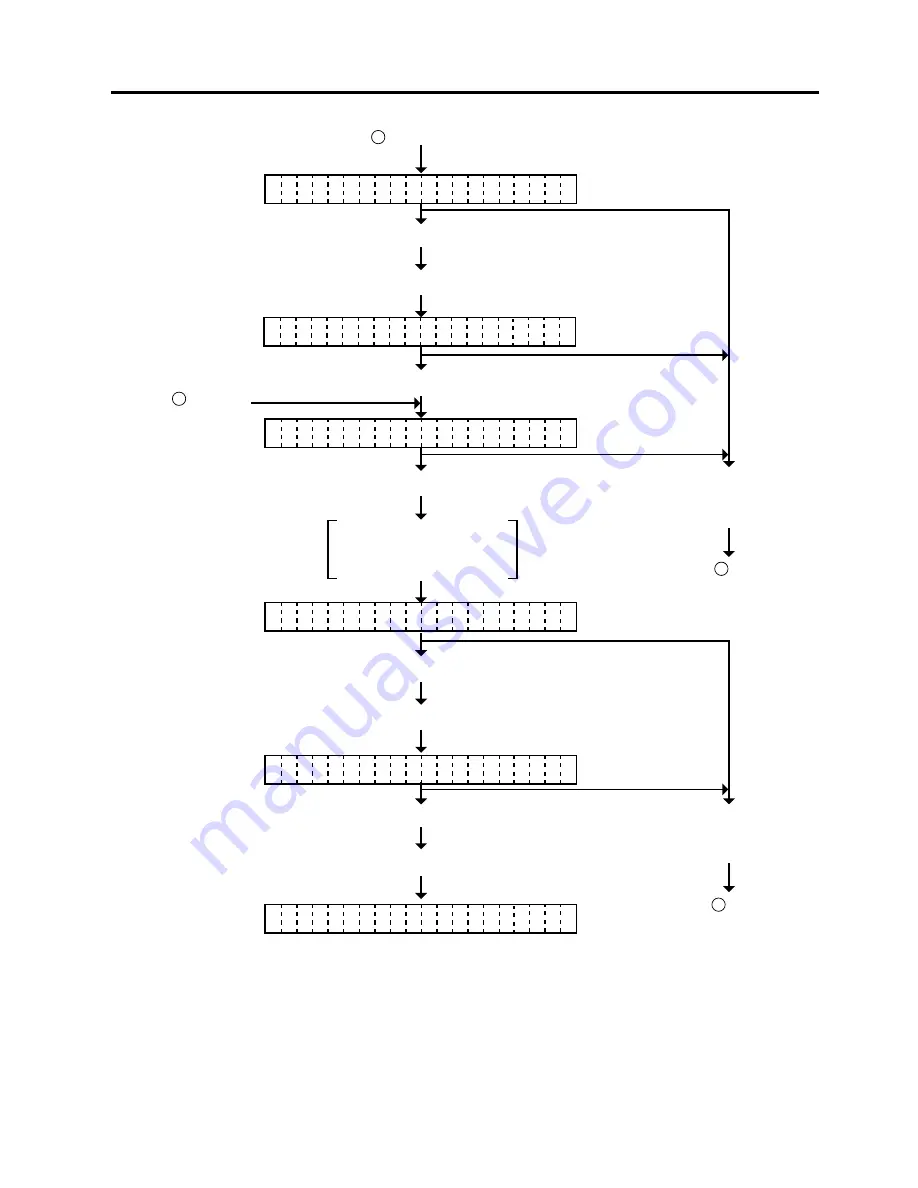
6-61
6. DIAG. TEST OPERATION
EO18-33007
6.4 TEST PRINT MODE
Press the [PAUSE] key.
Press the [PAUSE] key.
Press the [PAUSE] key.
[Bar code are printed on 5 labels.]
Press the [FEED] key
and [RESTART] key at
the same time.
Press the [PAUSE] key.
Press the [PAUSE] key.
[Characters are printed on 5 labels.]
Press the [FEED] key.
and [RESTART] key at
the same time.
[Characters are printed on 5 labels.]
From
B
of the next page.
From
A
of the
preceding page.
To
C
of the
preceding page.
After feeding one label,
slant lines (3 dots) are
printed on 5 labels.
To
C
of the
preceding page.
A U
O P R I N T ( T R A N S
T
. )
A U
O P R I N T ( T R A N S
T
. )
< 3
T E S T P R I N T
>
A U
O P R I N T ( R E F L E
T
C T . )
A U
O P R I N T ( T R A N S
T
. )
< 3
T E S T P R I N T
>
Содержание B-880 series
Страница 3: ...TEC Thermal Printer B 870 880 QQ SERIES Owner s Manual ...
Страница 35: ......
Страница 36: ...PRINTED IN JAPAN EO1 33017 ...
Страница 56: ......
Страница 57: ......
Страница 58: ...PRINTED IN JAPAN EO10 33008 ...
Страница 146: ...6 59 6 DIAG TEST OPERATION EO18 33007 Fig 6 25 Bar code AUTO PRINT Fig 6 24 ...
Страница 176: ......
Страница 177: ......
Страница 178: ...PRINTED IN JAPAN EO18 33007 ...
Страница 179: ......
Страница 180: ......