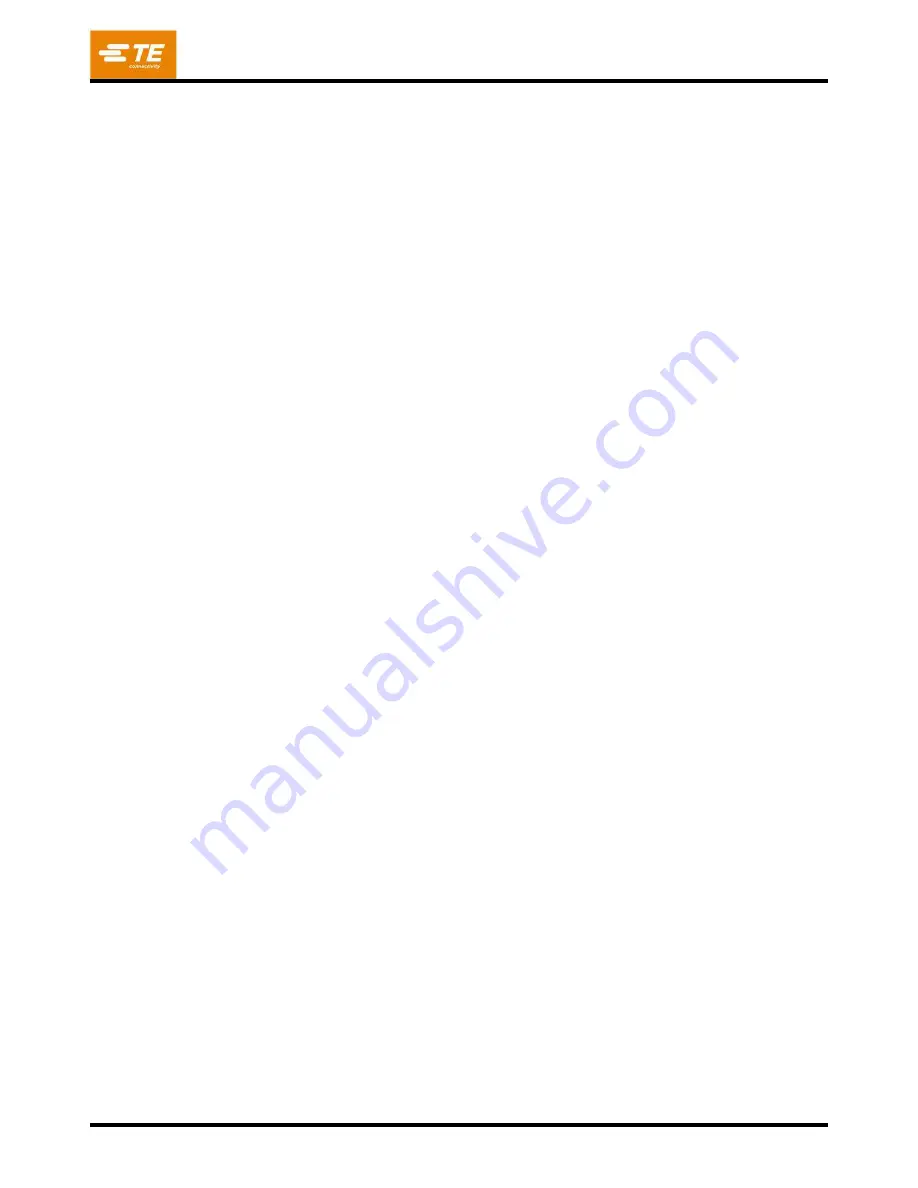
409-32048
Rev A
25
of 64
“Fixture ID” –
The fixture may be identified with an ID number. If a value is entered in this field, the user
will be prompted to verify the correct fixture ID when the cycle is started. This entry is not required.
“No. of Char. Req’d for Serial Number” –
The serial number of the board, if entered, is stored with the
raw pressing data. The force for each connector will be stored with this serial number and XY coordinates.
This feature has three types of entry: A zero (0) means no serial number prompt will be given. A positive
number means exactly that number of characters is required for a valid serial number, and a negative
number means at least that number of characters is required.
Bar code scanning is the preferred method of data entry.
“No. of Char. To Clear Between Boards” –
This feature is used in conjunction with the serial number
entry. In the case of sequential serial numbers, the program will clear this number of characters from the
end of the previous serial number. This is generally used when manual serial number entry is used.
“Verify Text” –
This feature is intended to verify that the correct board type is used with its press data
editor. If text is entered in this cell, board identification (type, name, model, etc,) will be required when first
entering the run screen, and each time a new board is started. Any text or number can be used, but
ideally, a bar code label will be available. Text can also be entered manually.
To enter the name, type “%V” followed by the string of characters.
“Prompt for Connector Substitution” –
This check box enables substitution connectors to be selected
at run time. For example, manufacturer “A” may be the prime source for a given connector, but “B” is also
approved as interchangeable on this board. If this box is checked, the operator will be offered a selection
of possible alternates for the connector at run time. This selection will drive the tools and profile identified
for pressing that connector. Thus, it is possible to press an alternate connector that requires different tools
and profile than the primary connector. The alternates are associated with each other through use of
“substitution codes” that are defined in the connector database. Each associated connector must be
individually entered into the database, but will be “linked” b
y the common substitution code.
“First Article Signoff” –
This feature stops the pressing cycle after the first board is complete. An
approval is required from a person other than the operator of the machine.
“Load/Unload Time per Board (s)”
-
This Administrative tool allows the entry of a set time (in seconds)
for a specific board run cycle. If machine run performance is not kept within this specific time allotment, an
alarm situation will occur. In addition, an audible Alarm Duration set time (in seconds) has been made
available.
“Alarm Duration (s)”
-
The alarm situation described above has an audible alarm in addition to the
machine stack-light system. Enter the desired audible Alarm Duration (seconds) in the box provided.
“Board Width”
-
This is the dimension of the board in the Y axis direction (front to back) as mounted in
the machine. It may or may not be the smaller board dimension, depending on how the board is oriented
in the machine. The maximum PCB width is 762 mm [30 in.].
“Board
Length”
-
This is the dimension of the board in the X axis direction (left to right) as mounted in
the machine. It may or may not be the larger board dimension, depending on how the board is oriented in
the machine. The maximum PCB length is 914.4 mm [36 in.].
“Measure Board Thickness”
-
The check box calls for board thickness to be measured on each board.
The X & Y entries provide the location on the board for the thickness to be measured. Only one point on
the board is measured.
“Board Edge to Datum”
-
This entry is used by the program to properly display the connectors on the
board. It is the nominal distance from the lower left edges of the board, in the X & Y directions, to the
board’s Datum described below.
“Machine 0 To Datum”
-
It is the distance fr
om the machine’s origin (0,0) point to the boards Datum. The
Machine 0 is the most lower-left Dowel hole in the table top. The Datum is normally a tooling hole in the
board used to locate the board to the support fixture. This distance can be determined by using the
distance from Machine 0 to one of the dowel hole locations used to mount/locate the fixture to the table
top. Then, take the distance from this dowel hole, to the locating pin on the fixture that engages the