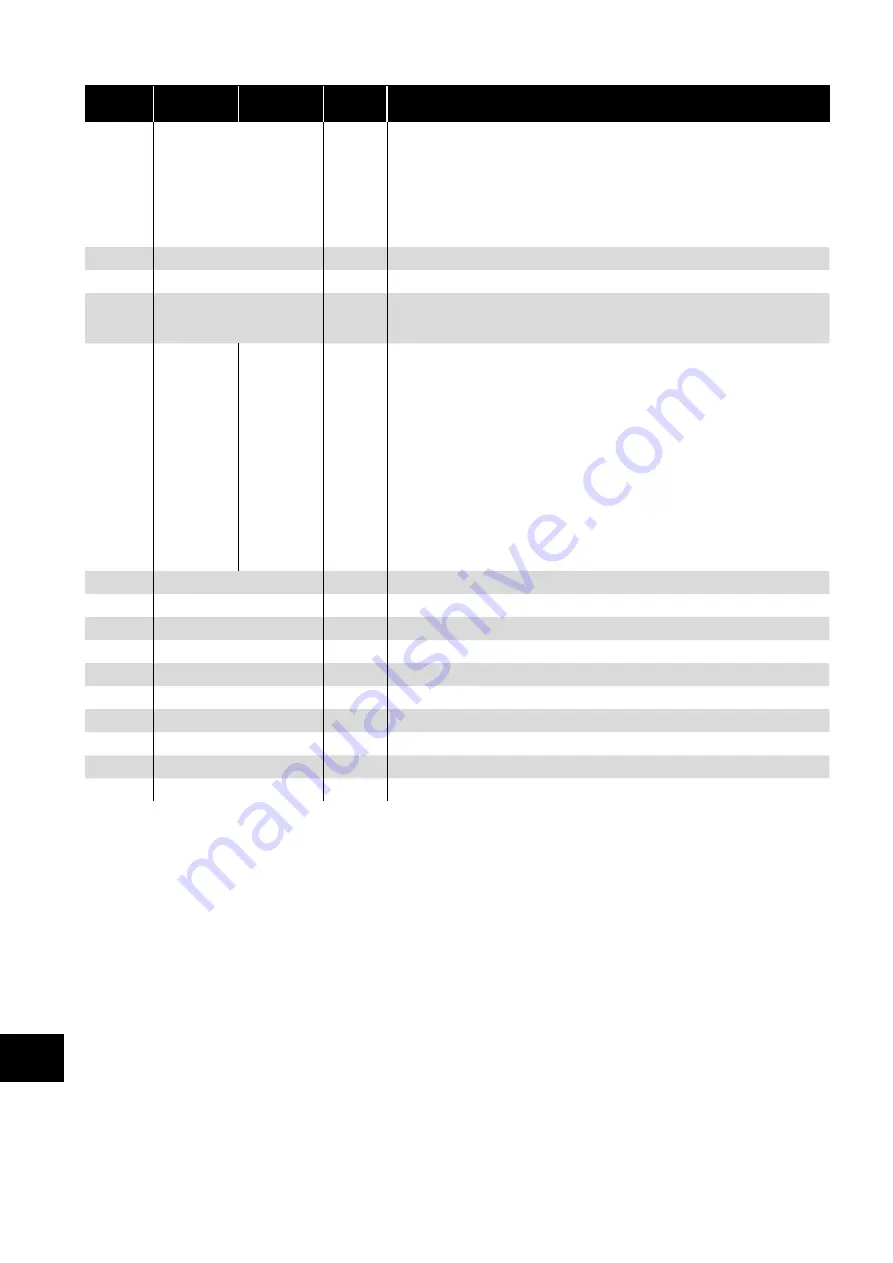
66
| Optidrive P2 User Guide |
Version 3.07
www.invertekdrives.com
Register
Number Upper Byte Lower Byte
Read
Write
Notes
1
Command Control Word
R/W
Command control word used to control the Optidrive when operating with Modbus
RTU. The Control Word bit functions are as follows:
Bit 0 : Run/Stop command. Set to 1 to enable the drive. Set to 0 to stop the drive.
Bit 1 : Fast stop request. Set to 1 to enable drive to stop with 2nd deceleration ramp.
Bit 2 : Reset request. Set to 1 in order to reset any active faults or trips on the drive.
This bit must be reset to zero once the fault has been cleared.
Bit 3 : Coast stop request. Set to 1 to issue a coast stop command.
2
Command Speed Reference
R/W
Setpoint must be sent to the drive in Hz to one decimal place, e.g. 500 = 50.0Hz.
3
Command Torque Reference
R/W
Setpoint must be sent to the drive in % to one decimal place, e.g. 2000 = 200.0%.
4
Command Ramp times
R/W
This register specifies the drive acceleration and deceleration ramp times used when
Fieldbus Ramp Control is selected (P5-08 = 1) irrespective of the setting of P1-12. The
input data range is from 0 to 60000 (0.00s to 600.00s).
6
Error code
Drive status
R
This register contains 2 bytes.
The Lower Byte contains an 8 bit drive status word as follows:
Bit 0 : 0 = Drive Disabled (Stopped), 1 = Drive Enabled (Running).
Bit 1 : 0 = Drive Healthy, 1 = Drive Tripped.
Bit 2 : No Function.
Bit 3 : 0 = Drive Ready (STO Input Closed), 1 = Drive Inhibit (STO Input Open).
Bit 4 : Maintenance Time Not Reached, 1 = Maintenance Time Reached.
Bit 5 : 0 = Not In Standby (Sleep), 1 = Standby (Sleep) mode active.
Bit 6 : 0 = Drive Not Ready, 1 = Drive Ready (Mains Power applied, No Inhibit, No
Trip, Enable Input Present).
Bit 7 : No Function.
The Upper Byte will contain the relevant fault number in the event of a drive trip.
for a list of fault codes and diagnostic information.
7
Output Frequency
R
Output frequency of the drive to one decimal place, e.g.123 = 12.3 Hz.
8
Output Current
R
Output current of the drive to one decimal place, e.g.105 = 10.5 Amps.
9
Output Torque
R
Motor output torque level to one decimal place, e.g. 474 = 47.4 %.
10
Output Power
R
Output power of the drive to two decimal places, e.g.1100 = 11.00 kW.
11
Digital Input Status
R
Represents the status of the drive inputs where Bit 0 = Digital Input 1 etc.
20
Analog 1 Level
R
Analog Input 1 Applied Signal level in % to one decimal place, e.g. 1000 = 100.0%.
21
Analog 2 Level
R
Analog Input 2 Applied Signal level in % to one decimal place, e.g. 1000 = 100.0%.
22
Pre Ramp Speed Reference
R
Internal drive frequency setpoint.
23
DC bus voltages
R
Measured DC Bus Voltage in Volts.
24
Drive temperature
R
Measured Heatsink Temperature in °C.
9.2.3. Modbus Parameter Access
All User Adjustable parameters (Groups 1 to 5) are accessible by Modbus, except those that would directly affect the Modbus
communications, e.g.
P5-01 Drive Fieldbus Address – see also P5-16 Drive Modbus Address.
P5-03 Modbus RTU Baud Rate.
P5-04 Modbus RTU Data Format.
All parameter values can be read from the drive and written to, depending on the operating mode of the drive – some parameters
cannot be changed whilst the drive is enabled for example.
When accessing a drive parameter via Modbus, the Register number for the parameter is the same as the parameter number,
e.g. Parameter P1-01 = Modbus Register 101.
Modbus RTU supports sixteen bit integer values, hence where a decimal point is used in the drive parameter, the register value will be
multiplied by a factor of ten,
e.g. Read Value of P1-01 = 500, therefore this is 50.0Hz.
For further details on communicating with Optidrives using Modbus RTU, please refer to your local Invertek Sales Partner.
9
Serial Communications