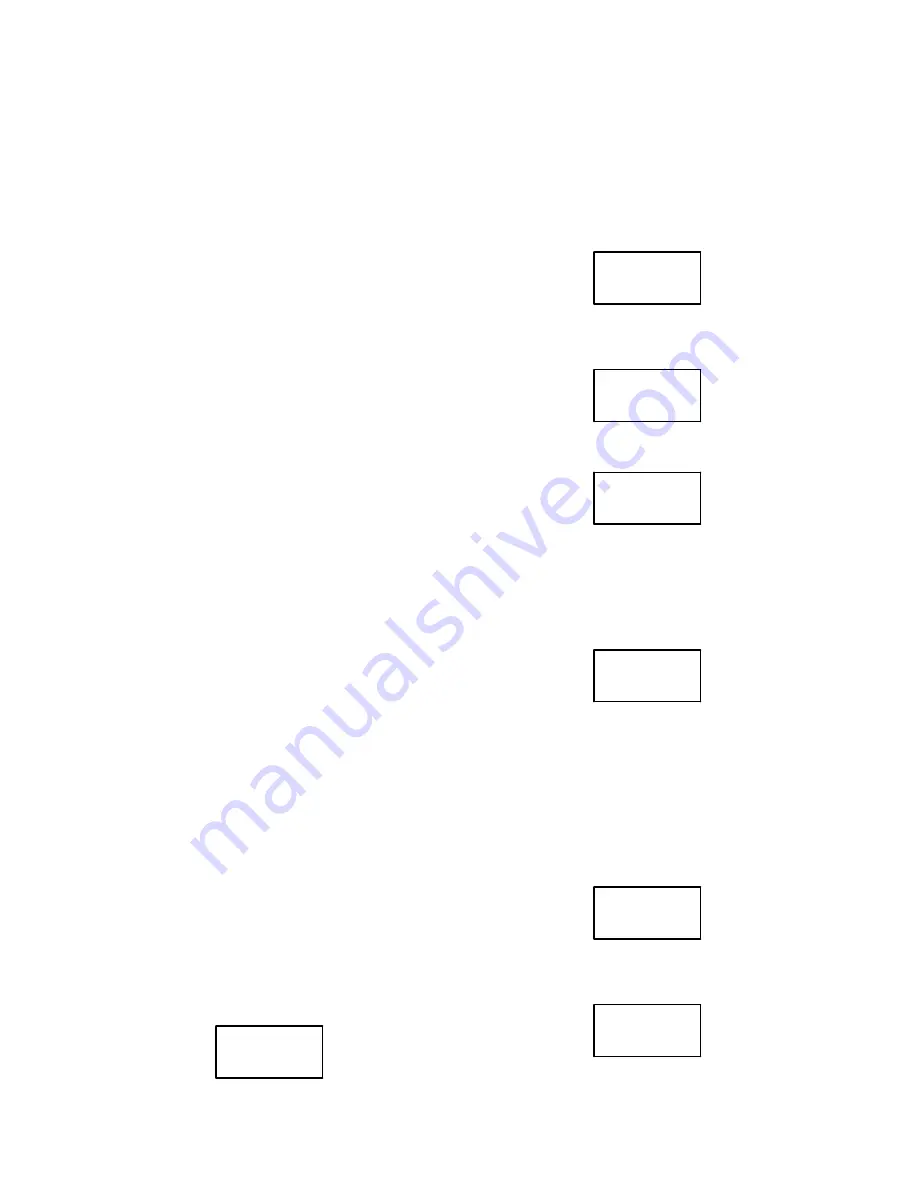
Section 5
OPERATION
23
6. Slowly close the shut---off valve and check that
the setting on the pressure switch is set correct-
ly. If set correctly, the compressor will unload at
the desired unload pressure. If adjustments are
necessary, see Control System Adjustment in
the Maintenance Section 7.7 of this manual.
7. Observe the operating temperature. If the oper-
ating temperature exceeds 205
_
F (96
_
C), the
cooling system or installation environment
should be checked.
8. Observe return line sight glass and maintenance
indicators.
9. Open shut---off valve to service line.
10. Reinspect the compressor for temperature and
leaks the following day.
5.4 SUBSEQUENT
START--UP
PROCEDURE--
STANDARD ELECTRO/MECHANICAL
On subsequent start---ups, check that fluid level is
visible in the fluid sight glass and simply press the
START button. When the compressor is running,
observe the instrument panel and maintenance in-
dicators.
5.5 SHUTDOWN PROCEDURE--STANDARD ELEC-
TRO/MECHANICAL
To shut the compressor down, simply press the
STOP button.
5.6 GENERAL INTRODUCTION -- SUPERVISOR
II
Reference Section 6, Supervisor
II
. While Sullair
has built into this compressor a comprehensive
array of controls and indicators to assure you that it
is operating properly, you will want to recognize
and interpret the readings which will call for service
or indicate the beginning of a malfunction. Before
starting your Sullair compressor, read this section
thoroughly and familiarize yourself with the con-
trols and indicators --- their purpose, location and
use.
5.7 SUPERVISOR
II
PARAMETER SETUP
Pressing the program key enters parameter dis-
play and edit mode. To move to the next parameter
press the program key. To increment a parameter
press the up arrow key or logo key. The logo key
will increment by 10. To decrement the value press
the down arrow key.
The parameters are displayed in the following or-
der:
S
Unload pressure
--- The pressure where
the machine is unloaded. For example if
this parameter is set to 110 psi (7.6 bar) the
machine will unload when the line pressure
is above 110 psi (7.6 bar).
UNLOAD
100 PSI
S
Load differential
--- The pressure differ-
ential below the unload pressure where the
machine is loaded. For example, if the un-
load pressure is set to 110 psi (7.6 bar) and
the load differential is set to 10 psi (0.7 bar),
the machine will load when the line pres-
sure goes below 100 psi (6.9 bar).
LOAD
10 PSI
S
P1 Max
--- Maximum sump pressure. An
alarm and shut down will occur when the
sump pressure rises above this pressure.
P1 MAX
135 PSI
S
Wye to delta transition timer
--- For full
voltage starters this parameter is set to 0.
WYE DELT
10 SEC
S
Restart time
--- Time to wait after power up
before starting machine. This parameter is
used to keep several machines from start-
ing at the same time after power up, or to
delay start until other equipment is started.
If disabled the machine will not automati-
cally start after power up.
RST TIME
10 SEC
S
Unload Stop Timer
--- If the machine is
running in AUTO mode, this parameter
specifies the amount of time that the ma-
chine will run unloaded before shutting off.
If the time is set less than 15 minutes (for
example five minutes), there may be times
when the machine will run unloaded for
more than five minutes. This is because
there is another timer that keeps the ma-
chine from being started more than four
times an hour.
UNLD TIM
15 MIN
S
Language select
--- English, German,
Spanish, Italian and French may be se-
lected for display language.
LANGUAGE
ENGLISH
S
Units
--- English or metric units may be se-
Содержание LS-10 18KW 24KT
Страница 6: ...NOTES...
Страница 15: ...Section 2 DESCRIPTION 9 Figure 2 3 Control System...
Страница 18: ...12 NOTES...
Страница 22: ...16 NOTES...
Страница 26: ...20 NOTES...
Страница 34: ...28 NOTES...
Страница 37: ...Section 6 SUPERVISOR II 31 MESSAGE DISPLAY SYSTEM GRAPHIC DISPLAY KEYPADS Figure 6 1 Supervisor II Panel...
Страница 38: ...32 NOTES...
Страница 48: ...Section 7 MAINTENANCE 42 Figure 7 7 Piping and Instrumentation Diagram Standard...
Страница 49: ...Section 7 MAINTENANCE 43 Figure 7 8 Piping and Instrumentation Diagram Supervisor II...
Страница 50: ...44 NOTES...
Страница 52: ...Section 8 ILLUSTRATIONS AND PARTS LIST 46 8 3 MOTOR COMPRESSOR FRAME AND PARTS...
Страница 54: ...Section 8 ILLUSTRATIONS AND PARTS LIST 48 8 3 MOTOR COMPRESSOR FRAME AND PARTS...
Страница 56: ...Section 8 ILLUSTRATIONS AND PARTS LIST 50 8 4 COOLER ASSEMBLY...
Страница 58: ...Section 8 ILLUSTRATIONS AND PARTS LIST 52 8 5 AIR INLET SYSTEM...
Страница 60: ...Section 8 ILLUSTRATIONS AND PARTS LIST 54 8 6 COOLING AND LUBRICATION SYSTEM...
Страница 62: ...Section 8 ILLUSTRATIONS AND PARTS LIST 56 8 6 COOLING AND LUBRICATION SYSTEM...
Страница 68: ...Section 8 ILLUSTRATIONS AND PARTS LIST 62 8 8 CONTROL SYSTEM AND ELECTRICAL PARTS...
Страница 70: ...Section 8 ILLUSTRATIONS AND PARTS LIST 64 8 8 CONTROL SYSTEM AND ELECTRICAL PARTS...
Страница 72: ...Section 8 ILLUSTRATIONS AND PARTS LIST 66 8 9 INSTRUMENT PANEL...
Страница 76: ...Section 8 ILLUSTRATIONS AND PARTS LIST 70 8 11 DECAL GROUP 1 2 3 4 5 6 7 8 9 10 11...
Страница 78: ...Section 8 ILLUSTRATIONS AND PARTS LIST 72 8 11 DECAL GROUP 12 13 14 15 16 17 18 19 20...
Страница 80: ...Section 8 ILLUSTRATIONS AND PARTS LIST 74 8 11 DECAL GROUP 21 22 23 24 25 26 27...
Страница 82: ...Section 8 ILLUSTRATIONS AND PARTS LIST 76 8 11 DECAL GROUP ADD FULL 29 28 30 31...
Страница 84: ...Section 8 ILLUSTRATIONS AND PARTS LIST 78 8 12 WIRING DIAGRAM ELECTRO MECHANICAL AIR COOLED WATER COOLED...
Страница 85: ...Section 8 ILLUSTRATIONS AND PARTS LIST 79 8 13 WIRING DIAGRAM SUPERVISOR II DELUXE AIR COOLED WATER COOLED...
Страница 88: ...NOTES...
Страница 89: ...NOTES...