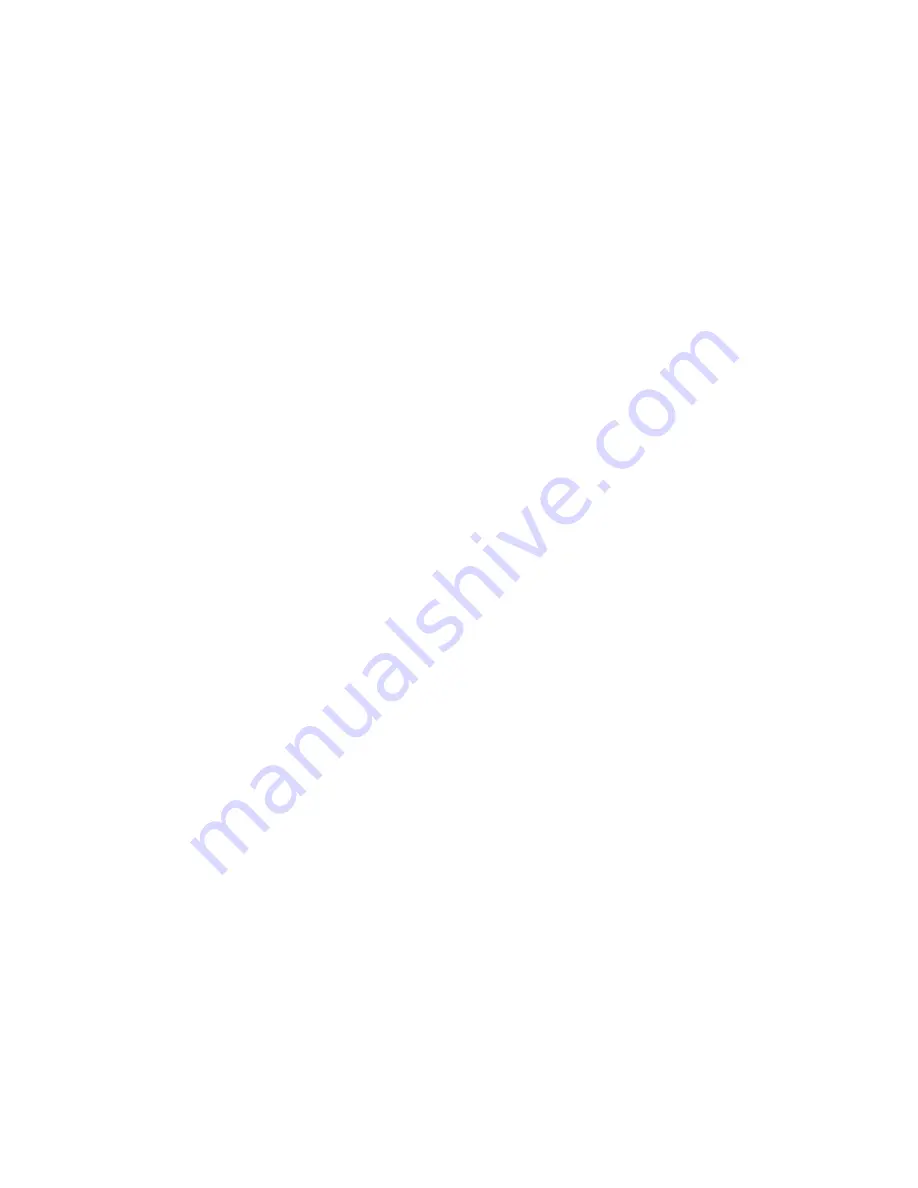
Section 1
SAFETY
3
C.
Operate the compressor only in open or ade-
quately ventilated areas.
D.
Locate the compressor or provide a remote inlet
so that it is not likely to ingest exhaust fumes or oth-
er toxic, noxious or corrosive fumes or substances.
E.
Coolants and lubricants used in this compressor
are typical of the industry. Care should be taken to
avoid accidental ingestion and/or skin contact. In
the event of ingestion, seek medical treatment
promptly. Wash with soap and water in the event of
skin contact. Consult the compressor operator’s
manual lubrication section for information pertain-
ing to compressor fluid fill.
F.
Wear goggles or a full face shield when adding
antifreeze compound to air line anti---icer systems.
G.
If air line anti---icer system antifreeze compound
enters the eyes or if fumes irritate the eyes, they
should be washed with large quantities of clean
water for 15 minutes. A physician, preferably an
eye specialist, should be contacted immediately.
H. DO NOT
store air line anti---icer system anti-
freeze compound in confined areas.
I.
The antifreeze compound used in air line anti-
freeze systems contains methanol and is toxic,
harmful, or fatal if swallowed. Avoid contact with the
skin or eyes and avoid breathing the fumes. If swal-
lowed, induce vomiting by administering a table-
spoon of salt, in each glass of clean, warm water
until vomit is clear, then administer two teaspoons
of baking soda in a glass of clean water. Have pa-
tient lay down and cover eyes to exclude light. Call
a physician immediately.
1.8 ELECTRICAL SHOCK
A.
This compressor should be installed and main-
tained in full compliance with all applicable Federal,
State and Local codes, standards and regulations,
including those of the National Electrical Code, and
also including those relative to equipment ground-
ing conductors, and only by personnel that are
trained, qualified and delegated to do so.
B.
Keep all parts of the body and any hand---held
tools or other conductive objects away from ex-
posed live parts of electrical system. Maintain dry
footing, stand on insulating surfaces and
DO NOT
contact any other portion of the compressor when
making adjustments or repairs to exposed live
parts of the electrical system. Make all such adjust-
ments or repairs with one hand only, so as to mini-
mize the possibility of creating a current path
through the heart.
C.
Attempt repairs in clean, dry and well lighted and
ventilated areas only.
D. DO NOT
leave the compressor unattended with
open electrical enclosures. If necessary to do so,
then disconnect, lock out and tag all power at
source so others will not inadvertently restore pow-
er.
E.
Disconnect, lock out, and tag all power at source
prior to attempting repairs or adjustments to rotat-
ing machinery and prior to handling any un-
grounded conductors.
F.
Dry test all shutdown circuits prior to starting the
compressor after installation.
1.9 LIFTING
A.
If the compressor is provided with a lifting bail,
then lift by the bail provided. If no bail is provided,
then lift by sling. Compressors to be air lifted by he-
licopter must not be supported by the lifting bail but
by slings instead. In any event, lift and/or handle
only in full compliance with Federal, State and Lo-
cal codes.
B.
Inspect points of attachment for cracked welds
and for cracked, bent, corroded or otherwise de-
graded members and for loose bolts or nuts prior to
lifting.
C.
Make sure entire lifting, rigging and supporting
structure has been inspected, is in good condition
and has a rated capacity of at least the weight of
the compressor. If you are unsure of the weight,
then weigh compressor before lifting.
D.
Make sure lifting hook has a functional safety
latch or equivalent, and is fully engaged and
latched on the bail or slings.
E.
Use guide ropes or equivalent to prevent twisting
or swinging of the compressor once it has been
lifted clear of the ground.
F. DO NOT
attempt to lift in high winds.
G.
Keep all personnel out from under and away
from the compressor whenever it is suspended.
H.
Lift compressor no higher than necessary.
I.
Keep lift operator in constant attendance when-
ever compressor is suspended.
J.
Set compressor down only on a level surface ca-
pable of safely supporting at least its weight and its
loading unit.
K.
When moving compressors by forklift truck, uti-
lize fork pockets if provided. Otherwise, utilize pal-
let if provided. If neither fork pockets or pallet are
provided, then make sure compressor is secure
and well balanced on forks before attempting to
raise or transport it any significant distance.
L.
Make sure forklift truck forks are fully engaged
and tipped back prior to lifting or transporting the
compressor.
M.
Forklift no higher than necessary to clear ob-
stacles at floor level and transport and corner at
minimum practical speeds.
N.
Make sure pallet---mounted compressors are
firmly bolted or otherwise secured to the pallet prior
to attempting to forklift or transport them.
NEVER
attempt to forklift a compressor that is not secured
to its pallet, as uneven floors or sudden stops may
Содержание LS-10 18KW 24KT
Страница 6: ...NOTES...
Страница 15: ...Section 2 DESCRIPTION 9 Figure 2 3 Control System...
Страница 18: ...12 NOTES...
Страница 22: ...16 NOTES...
Страница 26: ...20 NOTES...
Страница 34: ...28 NOTES...
Страница 37: ...Section 6 SUPERVISOR II 31 MESSAGE DISPLAY SYSTEM GRAPHIC DISPLAY KEYPADS Figure 6 1 Supervisor II Panel...
Страница 38: ...32 NOTES...
Страница 48: ...Section 7 MAINTENANCE 42 Figure 7 7 Piping and Instrumentation Diagram Standard...
Страница 49: ...Section 7 MAINTENANCE 43 Figure 7 8 Piping and Instrumentation Diagram Supervisor II...
Страница 50: ...44 NOTES...
Страница 52: ...Section 8 ILLUSTRATIONS AND PARTS LIST 46 8 3 MOTOR COMPRESSOR FRAME AND PARTS...
Страница 54: ...Section 8 ILLUSTRATIONS AND PARTS LIST 48 8 3 MOTOR COMPRESSOR FRAME AND PARTS...
Страница 56: ...Section 8 ILLUSTRATIONS AND PARTS LIST 50 8 4 COOLER ASSEMBLY...
Страница 58: ...Section 8 ILLUSTRATIONS AND PARTS LIST 52 8 5 AIR INLET SYSTEM...
Страница 60: ...Section 8 ILLUSTRATIONS AND PARTS LIST 54 8 6 COOLING AND LUBRICATION SYSTEM...
Страница 62: ...Section 8 ILLUSTRATIONS AND PARTS LIST 56 8 6 COOLING AND LUBRICATION SYSTEM...
Страница 68: ...Section 8 ILLUSTRATIONS AND PARTS LIST 62 8 8 CONTROL SYSTEM AND ELECTRICAL PARTS...
Страница 70: ...Section 8 ILLUSTRATIONS AND PARTS LIST 64 8 8 CONTROL SYSTEM AND ELECTRICAL PARTS...
Страница 72: ...Section 8 ILLUSTRATIONS AND PARTS LIST 66 8 9 INSTRUMENT PANEL...
Страница 76: ...Section 8 ILLUSTRATIONS AND PARTS LIST 70 8 11 DECAL GROUP 1 2 3 4 5 6 7 8 9 10 11...
Страница 78: ...Section 8 ILLUSTRATIONS AND PARTS LIST 72 8 11 DECAL GROUP 12 13 14 15 16 17 18 19 20...
Страница 80: ...Section 8 ILLUSTRATIONS AND PARTS LIST 74 8 11 DECAL GROUP 21 22 23 24 25 26 27...
Страница 82: ...Section 8 ILLUSTRATIONS AND PARTS LIST 76 8 11 DECAL GROUP ADD FULL 29 28 30 31...
Страница 84: ...Section 8 ILLUSTRATIONS AND PARTS LIST 78 8 12 WIRING DIAGRAM ELECTRO MECHANICAL AIR COOLED WATER COOLED...
Страница 85: ...Section 8 ILLUSTRATIONS AND PARTS LIST 79 8 13 WIRING DIAGRAM SUPERVISOR II DELUXE AIR COOLED WATER COOLED...
Страница 88: ...NOTES...
Страница 89: ...NOTES...