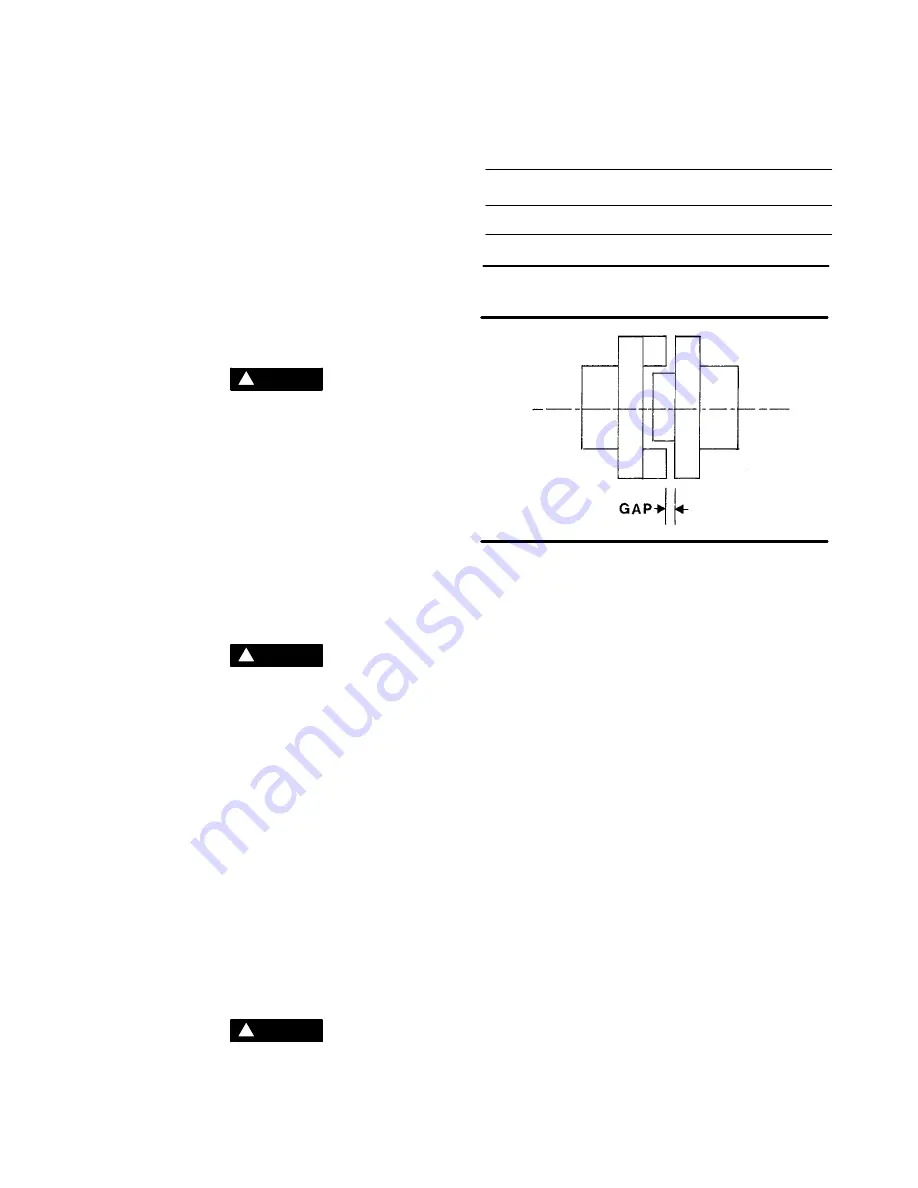
Section 7
MAINTENANCE
36
5. Open the service valve so the line pressure is 115
psig (7.9 bar). Machine is now set for operation.
Recheck the unload pressure by closing of the
service valve. Machine should unload via the
pressure switch at 125 psig (8.6 bar).
After the control pressures have been adjusted, the
“unloaded” sump pressure should be checked. It
will be necessary to shut the compressor down, re-
move the pressure switch cover, and disconnect
one of the two lead wires that are connected to the
micro---switch (contact block). After disconnecting
the lead, tape the exposed wire with electrician’s
tape to make sure that it does not come in contact
with any metallic surface.
DANGER
!
DO NOT touch the electrical contacts, terminal or
leads with any metallic object. Severe electrical
shock may occur.
With the lead taped, you may start the compressor
again. Allow the sump pressure to stabilize.
The sump pressure should read 30 to 35 psig (2.1 to
2.8 bar).
Once this is checked, shut the compressor down
once again and reconnect the taped lead and re-
place the pressure switch cover. At this time, start
the compressor and cycle the Control System sev-
eral times and re---check all pressure settings and
adjustments.
DANGER
!
DO NOT touch the pressure switch, electrical con-
tacts, terminal board or leads with any part of the
body or any un---insulated metallic object. Severe
electrical shock may occur.
PRESSURE REGULATOR ADJUSTMENT
Start the compressor and adjust the service valve to
maintain service air pressure at rated pressure (115
psig for example). Turn the adjusting screw on the
regulator until air just begins to escape from the
control air orifice. The regulator is now properly set.
DRIVE COUPLING INSTALLATION AND MAIN-
TENANCE
Refer to Figures 7---5 and 7---6. For coupling installa-
tion and maintenance the tools required will be a
measuring scale, one set of standard Allen
wrenches, and one set of standard socket
wrenches.
For installation and maintenance of the drive cou-
pling, follow the steps explained below.
DANGER
!
Disconnect all power at source, before attempting
maintenance or adjustments.
TABLE 1 INSTALLATION DATA
SERIES 10 (25---40HP/ 18---30 KW)
Horsepower
Coupling
Element
Coupling
Hub Gap
Tightening
Torque (Wet)
25 & 30 HP/
045672
.09---.125 in
55 ft.---lbs.
60, 75, 100
250004---638
110 ft.---lbs.
(75Nm)
(149Nm)
18 & 22 KW
(45, 55, 75 KW)
2.4---3.2 mm
.09---.125 in
2.4---3.2 mm
Figure 7---5 Drive Coupling “Hub” Gap Check
STEP 1 -- COUPLING GUARDS
There are three 5/16” screws from each of the wire
guards located on each side of the unit/motor adap-
tor for the 25/30 HP (18/22 KW) packages, or the two
3/8” bolt/nut/washer assemblies from the plate
guard and adaptor located on the top side.
STEP 2 -- MOUTING HUBS/ELEMENT
The coupling halves have a unique bore for the mo-
tor and the air---end. The air---end half is to be lo-
cated so that the hub is positioned against the shaft
shoulder and secured in place by two set---screws.
The motor half should remain free floating until the
element is in its proper location. The motor half is
then positioned within assembly maintaining an ax-
ial coupling gap as listed in Figure 7---5. There are
two set---screws located on the motor coupling half
also. Prior to starting of package, assure the set---
screws are secure to eliminate potential movement
of the hub.
7.9 TROUBLESHOOTING-- STANDARD ELECTRO/
MECHANICAL
The information contained in the Standard Electro-
Mechanical Troubleshooting chart has been com-
piled from field report data and factory experience. It
contains symptoms and usual causes for the de-
scribed problems. However,
DO NOT
assume that
these are the only problems that may occur. All avail-
able data concerning a problem should be system-
atically analyzed before undertaking any repairs or
component replacement procedures.
A detailed visual inspection is worth performing for
almost all problems and may avoid unnecessary
Содержание LS-10 18KW 24KT
Страница 6: ...NOTES...
Страница 15: ...Section 2 DESCRIPTION 9 Figure 2 3 Control System...
Страница 18: ...12 NOTES...
Страница 22: ...16 NOTES...
Страница 26: ...20 NOTES...
Страница 34: ...28 NOTES...
Страница 37: ...Section 6 SUPERVISOR II 31 MESSAGE DISPLAY SYSTEM GRAPHIC DISPLAY KEYPADS Figure 6 1 Supervisor II Panel...
Страница 38: ...32 NOTES...
Страница 48: ...Section 7 MAINTENANCE 42 Figure 7 7 Piping and Instrumentation Diagram Standard...
Страница 49: ...Section 7 MAINTENANCE 43 Figure 7 8 Piping and Instrumentation Diagram Supervisor II...
Страница 50: ...44 NOTES...
Страница 52: ...Section 8 ILLUSTRATIONS AND PARTS LIST 46 8 3 MOTOR COMPRESSOR FRAME AND PARTS...
Страница 54: ...Section 8 ILLUSTRATIONS AND PARTS LIST 48 8 3 MOTOR COMPRESSOR FRAME AND PARTS...
Страница 56: ...Section 8 ILLUSTRATIONS AND PARTS LIST 50 8 4 COOLER ASSEMBLY...
Страница 58: ...Section 8 ILLUSTRATIONS AND PARTS LIST 52 8 5 AIR INLET SYSTEM...
Страница 60: ...Section 8 ILLUSTRATIONS AND PARTS LIST 54 8 6 COOLING AND LUBRICATION SYSTEM...
Страница 62: ...Section 8 ILLUSTRATIONS AND PARTS LIST 56 8 6 COOLING AND LUBRICATION SYSTEM...
Страница 68: ...Section 8 ILLUSTRATIONS AND PARTS LIST 62 8 8 CONTROL SYSTEM AND ELECTRICAL PARTS...
Страница 70: ...Section 8 ILLUSTRATIONS AND PARTS LIST 64 8 8 CONTROL SYSTEM AND ELECTRICAL PARTS...
Страница 72: ...Section 8 ILLUSTRATIONS AND PARTS LIST 66 8 9 INSTRUMENT PANEL...
Страница 76: ...Section 8 ILLUSTRATIONS AND PARTS LIST 70 8 11 DECAL GROUP 1 2 3 4 5 6 7 8 9 10 11...
Страница 78: ...Section 8 ILLUSTRATIONS AND PARTS LIST 72 8 11 DECAL GROUP 12 13 14 15 16 17 18 19 20...
Страница 80: ...Section 8 ILLUSTRATIONS AND PARTS LIST 74 8 11 DECAL GROUP 21 22 23 24 25 26 27...
Страница 82: ...Section 8 ILLUSTRATIONS AND PARTS LIST 76 8 11 DECAL GROUP ADD FULL 29 28 30 31...
Страница 84: ...Section 8 ILLUSTRATIONS AND PARTS LIST 78 8 12 WIRING DIAGRAM ELECTRO MECHANICAL AIR COOLED WATER COOLED...
Страница 85: ...Section 8 ILLUSTRATIONS AND PARTS LIST 79 8 13 WIRING DIAGRAM SUPERVISOR II DELUXE AIR COOLED WATER COOLED...
Страница 88: ...NOTES...
Страница 89: ...NOTES...