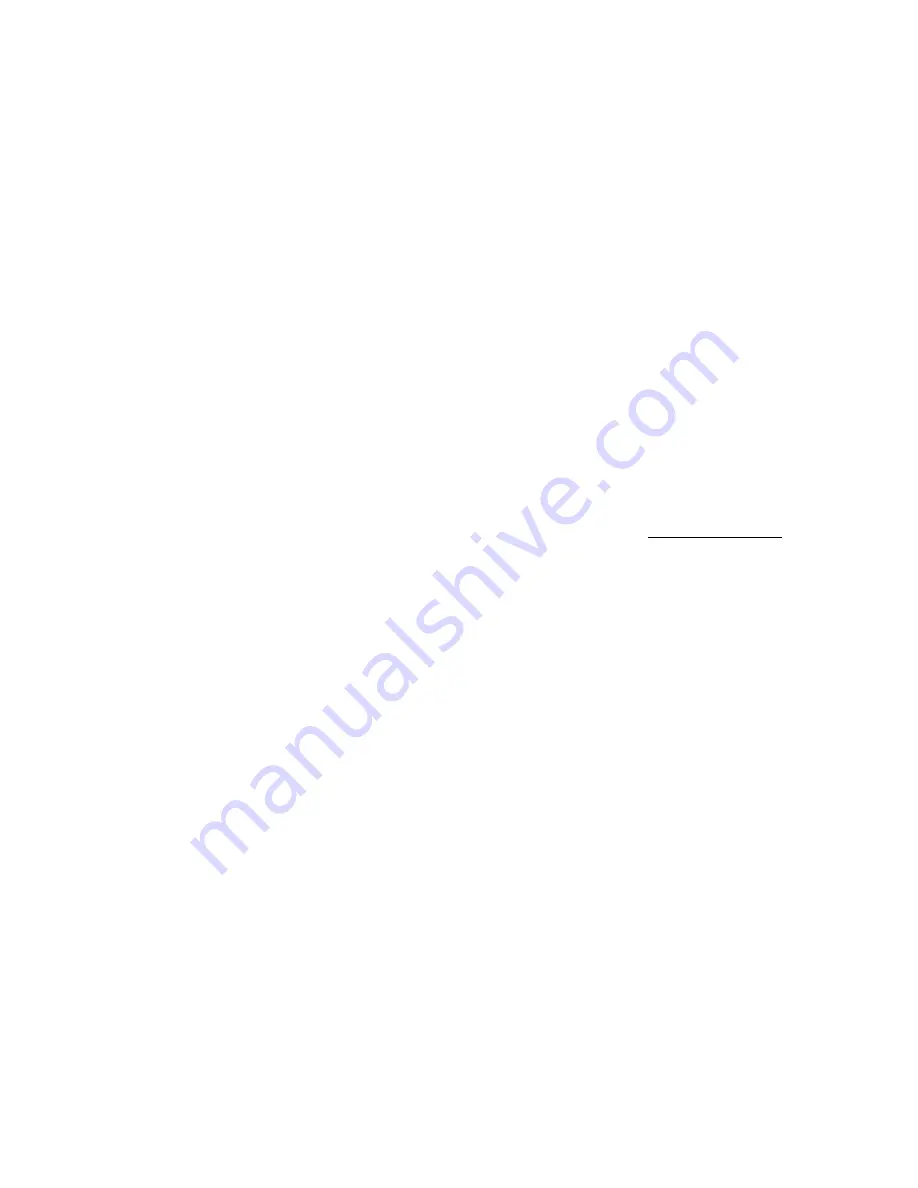
5
SECTION IV - PRE START-UP
A. Pre Start-Up
All equipment has been factory tested, adjusted, metered
and inspected to meet conditions set at the time the order
was placed. Only minimal adjustments should be required.
All information in this service manual is typical. All products
are semi-custom and changes may occur.
Suggested Tools and Instruments
Volt/Ohm Meter
Thermometer
Tachometer
Ammeter
Manometer (0-10" W.C.)
Microammeter
Standard Hand Tools
D.C Volt Meter
Gas Pressure Gauge (0-35 lbs.)
NOTE: All servicing and adjustments of the Direct
Gas-Fired unit should be performed by a qualified
service engineer.
1. The owner’s representative or equipment operator
should be present during start-up to receive instructions
on care and adjustments of the equipment.
2. Remove all shipping blocks, brackets and bolts from
supply fan base with optional isolation base.
3. Check all wiring for loose connections and tighten if
necessary.
CAUTION: Line side of disconnect may be
energized.
4. Inspect all fan and motor bearings and lubricate if
necessary.Tighten setscrews on pulleys, bearings, and fans.
CAUTION: Do not rupture grease seals.
5. Inspect pulleys and belts for tightness, tension and
alignment. Do not over tighten belts.
6. Check set screws on all bearings, pulleys and fans for
tightness.
7. Check voltage supplied to disconnect switch. The
maximum voltage variation should not exceed ±10%.
Phase voltage unbalance must not exceed 2%.
8. Check thermostat(s) for normal operation.
9. Check that system duct work is installed and free from
obstructions.
10. Check that fans turn free in housing.
11. Check burner for proper location and alignment.
12. Check that filters and accessories are installed correctly.
13. Check that vent lines have been run to atmosphere on
indoor units. Note that some units will use vent
limiters and vent lines are not required.
14. Check that all manual gas shut-off valves are closed.
15. When failure or malfunction of this heater creates a
hazard to other fuel burning equipment, (e.g. when the
heater provides make-up air to a boiler room), the
heater is to be interlocked to open inlet air dampers
or other such devices.
16. If inlet duct is attached to the heater, a purge
timer must be provided and set to purge 4 times
the inlet duct volume.
Purge time in seconds = 4 x L x W x H x 60
SCFM
L = duct length in feet,W = duct width in feet,
H = duct height in feet, SCFM = rating plate air
throughput.
Refer to the electrical schematic for the proper
circuit placement. Purge timer P/N 65.0711.00.