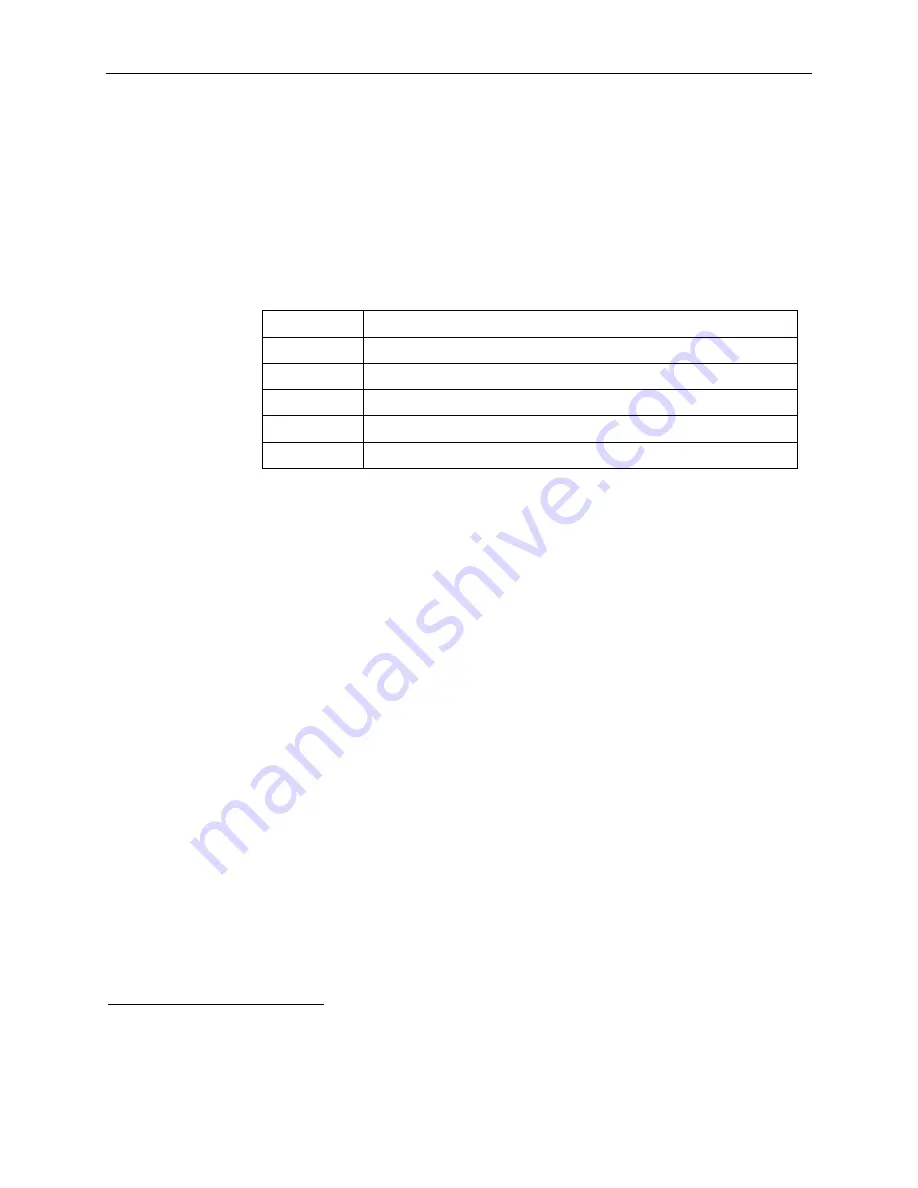
2-10
Chapter 2: Installation and Wiring
User’s Manual Pub. 0300246-01 Rev. C
Section 2.7
Module Indicators
The 1762 output module uses a single green LED to show operational status of
the module. The LED will illuminate solid when the PLC is in run mode and the
module properly configured. If the module is not properly configured, or if the
PLC is not in run mode, the LED will blink rapidly. The following blink codes
are the only exception:
Table 2-2 (LED Blink Codes)
Blink Code
Description
Rapid Blink
5
PLC not in run mode, or no valid module configuration present
Solid
Module is in run mode (Normal Operation)
3
Factory calibration in progress
4
Factory calibration invalid
5
Module is in command mode
5
All outputs are disabled until the PLC goes into run mode, and the module receives a valid configuration.
Содержание 1762sc-OF8
Страница 1: ......
Страница 6: ...vi MicroLogix 1200 8 Ch Output Module User s Manual Pub 0300246 01 Rev C ...
Страница 33: ...Chapter 3 Configuring the 1762sc OF8 for RSLogix 500 3 13 User s Manual Pub 0300246 01 Rev C ...
Страница 38: ...A 4 Appendix A Specifications User s Manual Pub 0300246 01 Rev C ...
Страница 40: ...User s Manual Pub 0300246 01 Rev C ...
Страница 41: ...User s Manual Pub 0300246 01 Rev C ...