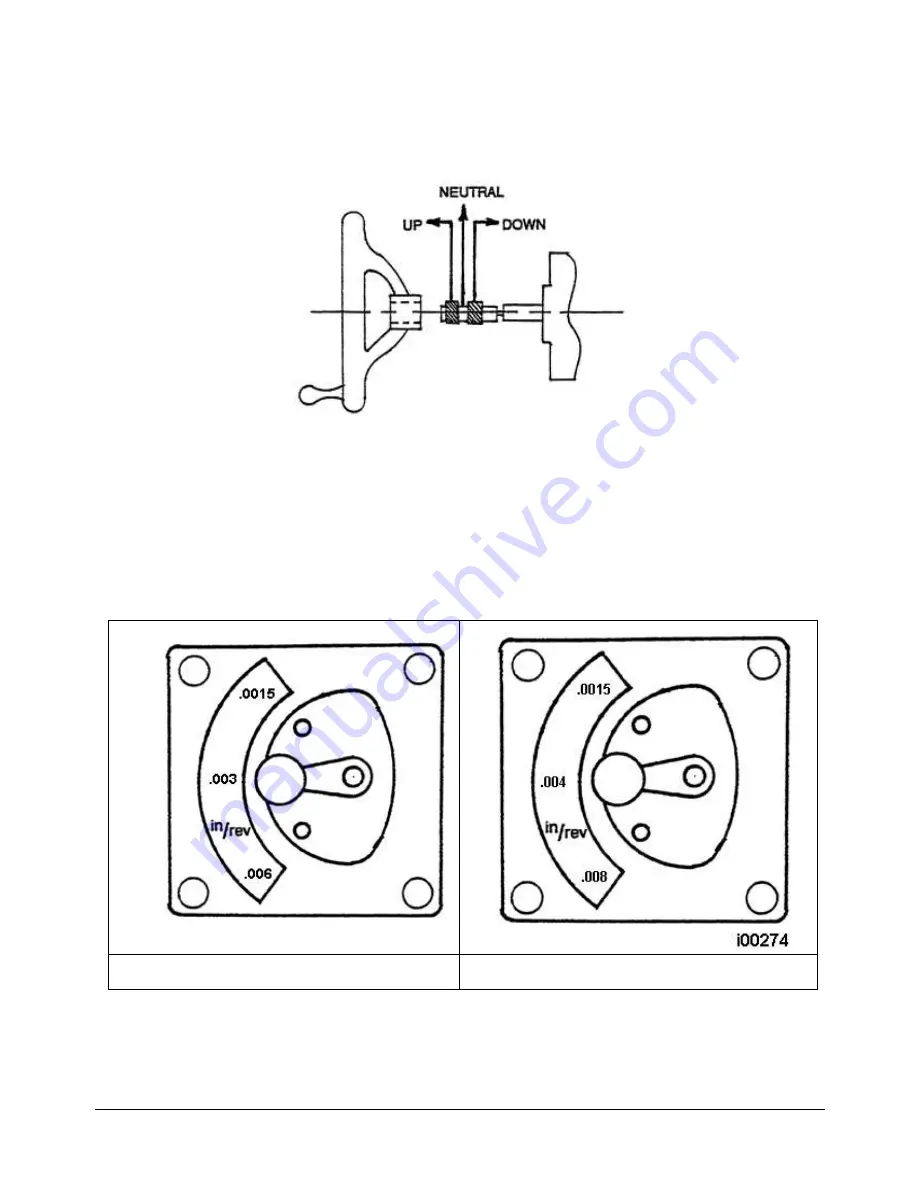
24
Southwestern Industries, Inc.
TRAK
EMX Knee Mill, Bed Mill & ProtoTRAK
EMX CNC Retrofit Safety, Programming, Operating & Care Manual
4.2.11 Fine Feed Direction Shaft
Figure 4.2.10.2
The direction of the fine feed is set by the position of the fine feed direction shaft. IN sets
the direction down, OUT sets the direction up, and NEUTRAL in the middle.
4.2.12
Quill Feed Selector
Figure 4.2.10.3 Quill Feed Selector for the K2, K3 &
DPMEX2
Figure 4.2.10.4 Quill Feed Selector for the K4
This selector is used to set the quill feed speed.
i00166